
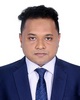
- Open Access
- Authors : Jayanta Bhusan Deb , Shuvrodeb Barman , Avijit Paul
- Paper ID : IJERTV12IS030196
- Volume & Issue : Volume 12, Issue 03 (March 2023)
- Published (First Online): 06-04-2023
- ISSN (Online) : 2278-0181
- Publisher Name : IJERT
- License:
This work is licensed under a Creative Commons Attribution 4.0 International License
Aerodynamics of Airfoil Upon Introduction of a Circular Rotary Trailing Edge
Jayanta Bhusan Deb
Department of Aeronautical Engineering Military Institute of Science and Technology Dhaka, Bangladesh
Avijit Paul
Department of Electronics and Communication Engineering West Bengal University of Technology
Kolkata, India
Shuvrodeb Barman
Department of Aeronautical Engineering Military Institute of Science and Technology Dhaka, Bangladesh
Abstract Aerodynamics of 0012 model airfoil designed by National Advisory Committee for Aeronautics, was experimented after placing a circular rotary cylinder at its trailing edge. First the cylinder was allowed to rotate in an anti-clockwise direction at a certain rpm. The simulation showed that there was a significant improvement of lift in modified airfoil. Parametric approach showed that, at zero degree angle of attack, when a symmetric airfoil typically doesnt generate any lift at all, due to the introduction of a rotary cylinder, positioned at the trailing edge of the modified airfoil, there was a finite amount of lift origination. The second set of simulation was done airfoil at different revolution per minute keeping the angle of attack constant and in all cases significant improvement of lift was noticed. This research can lead to a plethora of opportunities in front of the aviation industry in terms of fuel-efficient design of aircraft wings.
Keywords Airfoil; aerodynamics; lift; drag; aviation; simulation; algorithms; fuel-efficiency; design
-
INTRODUCTION
Introduction of the boundary-layer concept developed by Ludwig Prandtl (1904), there have been numerous research on boundary-layer control after facing a lot of challenges by scientists & engineers to increase lift and delay stall of wing [1]. Many methods such as suction, blowing, vortex generators, turbulence promoters, oscillatory surface flaps etc. have been applied in practical problems with a varying level of success. The concept of moving surface boundary-layer control (MSBC) is comparatively new and has not attained much popularity. However, lift augmentation of bluff bodies can be possible by this method [2]. A trailing edge cylinder (having an anti-clockwise rotation) is used as moving surface of the wing. The main objective for instigating the cylinder is to delay the separation of boundary-layer from the airfoil wall. Stagnation point moves downwards by using this trailing edge rotating cylinder resulting in an increase of lift and delay of stall at the trailing edge. NASA Ames Research Center conducted several successful flight tests to verify the MSBC concept and it was proved that this method had high potential at lift augmentation and reduction components, incorporating the applicable criteria that follow [3]. A good amount of research has been done seeking the aerodynamic potentiality of leading-edge rotating cylinder by Professor V.J. Modi at University of British Columbia; his experiments showed promising results,
effectively aiding in our current research motivation using updated tools and softwares [4].
If a non-rotating cylinder is placed in a wind tunnel it should give zero lift and finite amount of drag theoretically [5]. Giving anticlockwise rotation over the cylinder moves the stagnation point downwards making the flow over the upper surface larger than the lower one and hence making upper surface flow velocity higher than the lower surface flow velocity, subsequently generating a finite amount of lift [6]. This phenomenon is commonly known as the Magnus effect (as shown in Fig. 1).
Again, from Bernoullis equation, at any point in the flow field the amalgamation of the static and dynamic pressure is always constant. Mathematically,
P + ½V2 + gh = constant (1)
According to this equation, upper surface pressure must be less than the lower surface pressure and thus creating a net upward force known as lift force [7]. This theory coupled with the Magnus effect can help effective lift augmentation in modified airfoil models. The circular shape of the cylinder can easily bring about the advantages of Magnus effect while not necessarily making the experimental setup too impractical [8]. Also, the rotational speed was kept optimal for reducing any adverse effect due to the complex mechanical setup that would be required for the cause.
-
METHODOLOGY
Keeping the above background in mind it was decided to modify the NACA 0012 airfoil in such a way that the rotating cylinder could be placed at the rear of it. Numerical simulation using the Navier-Stokes Equations had to be done upon this modified airfoil model. In order to achieve that, such a modified airfoil which has the option to fit a cylinder of certain dimension in rear of it had to be designed. Also it should have enough space to rotate with minimum friction. The details design procedures are discussed in subsequent section:
-
Design of the Modified Airfoil
The trailing edge cylinder was placed at the 0.72 chord length for optimum shape and the cylinder diameter was chosen 0.067 chord to match the airfoil profile. Also, an
allowance of 3mm was left as an air gap for ensuring smooth rotation of the cylinder without colliding with the airfoil body. The factors that determined the cylinder size and position was the profile of the trailing edge of the base airfoil. For airfoil choice the most common airfoil was chosen for easy reference. The cylinder was mounted at the trailing edge because flow is most likely to start its separation from that region.
Fig. 1. Example showing the Magnus effect.
Fig. 2. Example showing typical flow over a symmetric airfoil
-
Simulation Setup
For flow conditions, standard atmospheric pressure and temperature was taken. Air was used as primary fluid with a velocity of 50 m/sec and the boundary conditions were given as real wall to capture the effect of boundary layer. For numerical simulation the Navier-Stokes equations were used and approximately 100,000 cells were generated by the structured mesh. The first set of simulation was done varying the angle of attack from 0 deg up to 36 deg with a step size of 4 deg. For the second set of simulation revolution per minute was varied from 1000 to 10,000 for a fixed 4 deg angle of attack.
-
-
RESULTS AND DISCUSSION
Astounding results have been found in terms of lift augmentation and delaying of stall angle in both sets of simulation. This can easily lead to fuel efficient wing design process and help reduce overall cost for the flight. The results for the simulation are shown in the following figures.
-
Results of Simulation at different angle of attack
Due to the effect of applying a rotating cylinder at the trailing edge of the airfoil, the natural tendency of the flow to separate from airfoil wall is delayed. This leads to a significant increase in lift force due to augmented pressure difference between the upper and lower surface.
Pressure contour for 8 deg AOA with 5000 revolution per minute. All the simulations were done keeping the revolution per minute fix at 5000. The availability of motors to produce the required angular velocity with minimal usage was the determining factor for this choice. Later, some hypothetical cases with even more revolution per minute were analyzed to validate the scope of this choice and find the revolution for the cylinder for optimal performance.
-
Tables and Graphs Showing Lift Augmentation
The tabulation clearly shows that upon the introduction of a rotating cylinder at the trailng edge of the airfoil, the lift to drag ratio has drastically increased. Also, the stall angle has been delayed from 28 deg to 38 deg. The increased lift to drag ratio means more lift force can be generated for the same amount of power. Also, It can be seen from table 2 that the choice of revolution per minute of 5000 is valid as we see a huge generation of drag as we go for 9000 plus rpm.
II. CONCLUSION
By the computational analysis with a symmetrical NACA- 0012 airfoil using a trailing-edge rotating cylinder, several revolutionary ideas have emerged:
-
The analysis showed that lift augmentation is possible by mounting a rotating cylinder at the rear of a conventional airfoil. And it has been proven for different flight data. But drag has also been increased a bit in this process due to more fictional occasions. But the increased lift-to-drag ratio negates this phenomenon.
-
The introduction of a trailing-edge cylinder extends the lift curve without essentially changing its slope, thus significantly increasing the maximum lift coefficient.
Fig. 3. Pressure contour for 0 deg (left) and 4 deg (right) AOA with 5000 revolutions per minute
Fig. 4. Pressure contour for 8 deg (left) and 12 deg (right) AOA with 5000 revolutions per minute
Fig. 5. Pressure contour for 16 deg (left) and 20 deg (right) AOA with 5000 revolutions per minute
Fig. 6. Pressure contour for 24 deg (left) and 28 deg (right) AOA with 5000 revolutions per minute
Fig. 7. Pressure contour for 32 deg (left) and 36 deg (right) AOA with 5000 revolution per minute
Fig. 8. Pressure contour for 4 deg AOA with 1000 revolutions (left) and 2000 revolutions (right) per minute
Fig. 9. Pressure contour for 4 deg AOA with 3000 revolutions (left) and 4000 revolutions (right) per minute
Fig. 10. Pressure contour for 4 deg AOA with 6000 revolutions (left) and 8000 revolutions (right) per minute
Fig. 11. Pressure contour for 4 deg AOA with 9000 revolutions (left) and 10000 revolutions (right) per minute
Angle of
Lift for base
Drag for
Lift for
Drag for
Attack
airfoil
base airfoil
modified
modified
airfoil
airfoil
0
0.0205
0.0565
1.1382
1.3662
4
1.6520
0.1182
12.2113
1.4324
8
2.6434
0.2616
17.6180
1.7644
12
3.4584
0.8002
20.6362
1.8937
16
4.8220
1.8614
27.2669
2.1945
20
5.4077
2.5148
35.4399
3.0671
24
6.7527
3.1492
38.0270
3.5749
28
9.0662
5.1748
44.2971
3.8069
32
8.1722
5.4158
58.7592
3.9969
36
1.1303
8.7845
46.2576
15.6322
TABLE I. LIFT AND DRAG VALUES FOR BASE AIRFOIL AND MODIFIED AIRFOIL AT DIFFERENT ANGLE OF ATTACK
5000
13.7978
1.4341
6000
13.8398
1.4342
7000
14.2694
1.4851
8000
14.3853
1.4875
9000
15.3300
127.31
10,000
25.5400
142.31
TABLE II. LIFT AND DRAG VALUES FOR BASE AIRFOIL AND MODIFIED AIRFOIL AT DIFFERENT REVOLUTIONS PER MINUTE
-
The 2-D flow visualization study confirmed the concepts significance in a remarkable fashion. It gave a better appreciation of the complex flow.
-
The challenge for this project is to design effective methods for the rotating arrangements, which can turn a bit complex for higher rotation; this was the main reason for choosing 5000 rpm, though up to 8000 rpm, the augmentation in the lift-to-drag ratio was beneficial. If the proper system for achieving higher rpm can be designed, this effect can be utilized even more.
-
Revolution per minute |
Lift for modified airfoil |
Drag for modified airfoil |
1000 |
11.7373 |
1.3906 |
2000 |
11.9201 |
1.4157 |
3000 |
12.1426 |
1.4257 |
4000 |
12.4216 |
1.4313 |
REFERENCES
[1] V. Modi, F. Mokhtarian, and T. Yokomizo, Effect of moving surfaces on the airfoil boundary-layer control, J. Aircr., vol. 27, no. 1, pp. 42 50, 1990. [2] V. Modi, F. Mokhtarian, M. Fernando, and T. Yokomizo, Moving surface boundary-layer control as applied to two-dimensional airfoils, J. Aircr., vol. 28, no. 2, pp. 104112, 1991. [3] M. A. I. Yousuf, N. A. M. J. B. Deb, and M. H. Bappy, A Research Framework of Supply Chain Logistics using Horizontal Collaboration for Developing Countries, presented at the MESSAGE FROM THE CONFERENCE CHAIRS, p. 167. [4] V. Modi et al., Movi-ng-Surface Boundary-Layer Control for Aircraft Operation at High Incidence, J. Aircr., vol. 18, no. 11, pp. 963968, 1981. [5] S. A. Ratna, F. Rahman, M. A. I. Yousuf, and J. B. Deb, An Explanatory Study of the Present Scenario of Credit Risk Management in the Banking Sector, presented at the MESSAGE FROM THE CONFERENCE CHAIRS, p. 177. [6] J. Preston, Boundary Layer and Flow Control. Edited by GV LACHMANN. London: Pergamon Press, 1961. Vol. I, 600 pp.; vol. II,750 pp.£ 10. 10s. per set of two volumes., J. Fluid Mech., vol. 13, no. 2, pp. 315320, 1962.
[7] J. Deb, N. Ahsan, and S. Majumder, Modeling the Interplay Between Process Parameters and Part Attributes in Additive Manufacturing Process With Artificial Neural Network, in IMECE2022, Volume 2A: Advanced Manufacturing, Oct. 2022. doi: 10.1115/IMECE2022-95120. [8] A. Favre, Contribution à létude expérimentale des mouvements hydrodynamiques à deux dimensions, no. 137. E. Blondel La Rougery, 1938.