
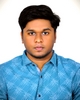
- Open Access
- Authors : Agadheesh S , Dhuruva P , Lakshman Ragavendar. N , Jim Ebenezar Manickam. M, Dr. Asad Ahamed. R
- Paper ID : IJERTV10IS060422
- Volume & Issue : Volume 10, Issue 06 (June 2021)
- Published (First Online): 03-07-2021
- ISSN (Online) : 2278-0181
- Publisher Name : IJERT
- License:
This work is licensed under a Creative Commons Attribution 4.0 International License
Aerodynamic Performance of Co Flow Jet At Different Angle of Attacks
Dr. Asad Ahamed. R*1, Dhuruva. P#1, Agadheesh. S#2, Lakshman Ragavendar. N#3, Jim Ebenezar Manickam. M#4
*1Assistant Professor (Sr Scale), #1, #2, #3, #4UG Student,
*1, #1, #2, #3, #4Department of Aeronautical and Aerospace engineering, KCG College of Technology, Karapakkam.
Abstract – The active flow control over aerofoil using co-flow jet (CFJ). With injection and suction slot on upper surface in leading edge (LE) and trailing edge (TE) of the aerofoil. To achieve high efficiency, the co-flow jet is analyzed with different angle of attack. The NACA 4412 aerofoil is used for both baseline and co-flow jet, where the CFJ can be work with any aerofoil [1]. The high angle of attack is achiever at lower speed without stalling. The Ansys CFD software is used with the 2-equation turbulence. The overall performance is increased by 33% to 66% compared to baseline airfoil.
Keywords Aerofoil, Angle of attack, Ansys CFD, co-flow jet
Fig.2: Baseline
GEOMETRY SETUP
(CFJ), LE&TE
INTRODUCTION
The CFD software is a used to simulate and study the
flow over the aerofoil. The k- turbulence (two equation)
In order to achieve high performance, the active flow control method is used. Where the co-flow jet (CFJ) with injection slot and suction slot at leasing edge (LE) and trailing edge (TE) As a reference, The CFJ aerofoil is compared with a Baseline aerofoil series NACA-4412. where the aerofoil is designed with CFJs injection and suction slot. the chord length is 0.151m, the CFJ aerofoil is modified design of Baseline aerofoil by translating the modified surface lowered vertically 1.67% ± 0.05% of chord [2]. The injection is located at 6.72%
± 0.05% and suction slot is located at 88.72% ± 0.05% of the chord from the LE. The area of injection slot is 1.50% ± 0.05% and suction slot is 1.60% ± 0.05% of the chord.
Where here we use the slot area as same 1.56% of chord which is 0.00236m
Fig.1: Co-flow jet
module is used as wall function to save CPU time. The turbulence equation is same through all the condition, in order to reduce the time taken by the computer 2 turbulence equation is used [3].The Reynolds number taken here is 50,000 which is lowest number for the aerofoil NACA 4412 as per the database which is 50 m/s. Where the aim is to achive higher angle of attack with minimum speed
Where Re is the Reynolds number, a dimensionless number used in fluid mechanics to indicate whether fluid flow past a body or in a duct is steady or turbulent [4].
Fig.3
Considering the pressure, velocity, area and mass flow rate at the injection and suction slot of CFJ, the co-efficient of jet (Cµ) varies with respect to Ao
Cµ-coefficient of cfj
mj- mass flow rate of cfj – density of air
U- velocity of free stream
S- area
Where Cµ varies with AoA. The value of Cµ varies from 0.08 to 0.25 with respective to AoA of the airfoil. At mach 0.145, Cµ=0.08 at 0° which is more efficient in comparison, the Cµ is estimated by comparison of value at every condition [5].
Fig.4: AOA v/s Cµ
RESULTS
Fig.5(a): Pressure contour at AoA 0°
Fig.5(b): Velocity contour at AoA 0°
The Fig. 5 (a), (b) shows the pressure and velocity contour respectively. The operating condition is mach number 0.145 which is the minimum velocity of the airfoil as per the data base. The velocity is same is all the angle of attack. Where the force generated is we found through the journal paper we gone through.
There is force produced on aerofoil due co-flow jet in both x and y axis.
F- momentum force mj- mass flow
Vj- velocity at slot Pj- pressure at slot Aj- area at the slot
– angle between slot to perpendicular to chord
Fig.6(a)
Fig.6(b)
The lift coefficient with respective to AoA where in the Baseline aerofoil the Cl stops to drop gradually beyond 15°, where in CFJ aerofoil the Cl value stay high at AoA of 30°. The drag coefficient with respective to AoA, where the Cd at 0° and 5° are in negative because due to the CFJ there is a momentum produced in the aerofoil which is in x direction
After 50° it starts to drop in larger amount which is greater than the drag produced beyond that angle. In accordance with the journal paper the flow separation havent take place up to AoA of 20° so we go beyond the AoA of 20° to check the flow seperation taken place
In comparison of base line aerofoil the CL range from
0.356 to 1.0076, where in CFL the CL range from 0.374 to
1.105 which is comparatively higher. The drag coefficient is range from 0.0204 to 0.401(at 20°) and in CFJ due to the momentum force negative drag formation take place where 0.03314 to 0.20877(at 20°) which is much more lover than the base line aerofoil and the drag produced by the baseline aerofoil at 20° is produced Co-flow jet at 30° [6].
Where the significant increase in efficiency at M=0.4 but, here the efficient value of Co-flow jet is found at lower velocity M=0.145 for higher angle of attack.
Fig7(a)
Fig.7(b)
In Fig.7(a) shows the stream line of the flow from injection slot to suction slot where the flow is attached to the surface of the aerofoil, but in the Fig7(b) the flow separates and not attached to the surface of the airfoil which results in larger amount of increase in drag and massive drop in lift beyond that AoA [8].
CONCLUSION
The co-flow jet aerofoil design in this report is capable to reduce drag force and convert streamline vortices to additional thrust, which is much more effective up to AoA of 45° and at lower velocity M=0.145. The obtained results from the analysis proves that the CFJ airfoil will produce more lift coefficient than the baseline airfoil. This is because the downstream gets energized due to the injection air. So that the airflow remains attached over to the body, and it increases the lift coefficient [9].
Where there is no change in flow separation beyond the AoA od 50°, even though coefficient of CFJ is tested with higher value up to Cµ=0.5 the flow separation remains constant.
ACKNOWLEDGEMENTS
We thank our management and our Principal Dr. P. DEIVASUNDARI for the opportunities given to us for our career development.
We feel indebted to the Head of the Department Dr. K. VIJAYARAJA, Department of Aeronautical and Aerospace Engineering, KCG College of Technology, for all his encouragement, which has sustained our labor and efforts. We express our deepest gratitude to the internal guide Dr. ASAD AHAMED Assistant Professor, Department of Aeronautical Engineering, KCG College of Technology, for his valuable guidance, ideas and support.
We would like to thank all other faculty members of our Department for their help and advice throughout our life in this campus.
Finally, we are thankful to all our friends and all others who encouraged us and helped us in doing this project
REFERENCES
-
Novel Flow Control Method for Airfoil Performance Enhancement Using Co-Flow Jet Ge-Cheng Zha and Craig D. Paxton, University of Miami, Coral Gables, Florida.
-
Jet Effects on Coflow Jet Airfoil Performance Ge-Cheng Zha,S Wei Gao, and Craig D. Paxton, University of Miami, Coral Gables, Florida 33124 PAPER 1222 -1230.
-
Numerical Investigations of Injection Slot Size Effect on the Performance of Co-Flow Jet Airfoil Baoyuan Wang, Bahaa Haddoukessouni, Jonathan Levy, Ge-Cheng Zha Dept. of Mechanical and Aerospace Engineering University of Miami, Coral Gables, Florida 33124.
-
Experimental nvestigation of Jet Mixing of a Co-Flow Jet Airfoil B.
P. E. Dano, D. Kirk and G.-C. Zha Dept. of Mechanical and Aerospace Engineering University of Miami, Coral Gables, FL 33124.
-
Wind Tunnel Testing of NACA 0021 Aerofoil with Co- Flow Jet Emilon Zeon Rajan1, T S Gowthaman2, C Ganesan3, K Balaji4, K M Kiran Babu , Depart- 79 ment of Aeronautical Engineering Karpagam Institute of Technology, Coimbatore, Tamilnadu, India[ICSSCCET 2015].
-
Ge-Cheng Zha, G.-C., and Paxton, D. C., %A Novel Flow Control Method for Airfoil Performance Enhancement Using Co-Flow Jet, Applications of Circulation Control Technologies, edited by Joslin, R.
-
and Jones, G. S., Progress in Astronautics and Aeronautics, Vol. 214, AIAA, Reston, VA, 2006, pp. 293314, Chap.10.
-
-
Aerodynamic performance enhancement for flapping airfoils by co- flow jet Tao WU a, Bifeng SONG , Wenping SONG , Wenqing YANG a,Zhonghua HAN a School of Aeronautics, Northwestern Polytechnical University, Xi#an 710072, China b Yangtze River Delta Research Institute, Northwestern Polytechnical University, Taicang 215400, China.
-
Performance and Energy Expenditure of Coflow Jet Airfoil with Variation of Mach Number A. Lefebvre,$B. Dano, W. B. Bartow, M.
-
Fronzo, and G. C. Zha University of Miami, Coral Gables, Florida 33124. DOI: 10.2514/1.C033113.
-
-
Application of Co-Flow Jet Concept to Aircraft Lift Increase Sai Likitha Siddhanath Application of Co-Flow Jet Concept to Aircraft Lift Increase