
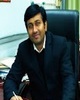
- Open Access
- Authors : Ashutosh Kumar Pandey , Richa Arya , Shweta Singh , Ashutosh Pandey, Vinay Pratap Singh
- Paper ID : IJERTV9IS050544
- Volume & Issue : Volume 09, Issue 05 (May 2020)
- Published (First Online): 28-05-2020
- ISSN (Online) : 2278-0181
- Publisher Name : IJERT
- License:
This work is licensed under a Creative Commons Attribution 4.0 International License
A Sustainable Challenges of Abrasive Jet Machining (AJM): Art-of-Review
Ashutosh Kumar Pandey1, Richa Arya2, Shweta Singp, Ashutosh Pandey2, Vinay Pratap Singp 1
Assistant Professor, Department of Mechanical Engineering
2 Student, UG, Department of Mechanical Engineering
Institute of Technology & Management Gida Gorakhpur, Uttar Pradesh, India (273209)
Abstract:- Abrasive jet machining technology has been proven for several present & future applications in many manufacturing industries and R&D sectors like cutting, drilling & engraving of brittle material. It is one of the versatile materials processing technique & is applied in abrasive jet machining, debarring, shot peening, erosion testing, fast cleaning, surface preparation & polishing. Abrasive jet machining (AJM) is a manufacturing technology based on Erosion localization and intensification. AJM has a progressively important influence on the machining technology market. Over the past 25 years, there has been an exponential growth in the number of papers that discuss AJM. Various innovations and process developments such as intermittent, submerged and thermally assisted and other jet conditions were proposed. This paper examines AJMs technological advantages and the variety of machining operations in different industries where AJM is utilized. Particular attention is devoted to the micro-texturing capabilities of powder blasting and its application in tribology. New evidence of ductile and brittle material removal mechanisms are reviewed together with recently discovered elastic removal mode.
Keywords: Abrasive jet machining, Micromachining, Material removal mechanism, Process parameters, Nozzle wear
INTRODUCTION
Abrasive jet machining (AJM), also knownias abrasive micro-blasting, pencil blasting and micro-abrasive blasting, is an abrasive blasting machining process that uses abrasive propelled by a high velocity gas to erode material from the work piece. Brittle materials such as glass, ceramics, silicon, and germanium, have been widely used in semiconductor, optical, biosensors, micro-electronics, micro-fluidic devices and other fields. Traditional machining approaches such as milling and drilling are not very effective at machining brittle materials. Abrasive jet micromachining (AJM) is a promising non-traditional machining technology for the cost effective fabrication of micro-structures on brittle and hard materials. The AJM process is based on the erosion of substrate by an abrasive-laden air jet or abrasive air jet (AAJ). The abrasive particles are accelerated to a high velocity by applying pressurized air in a fi ne nozzle, and the nozzle moves relative to the work substrate for making a structure on it. The removal of materials in AJM is achieved by means of micro plastic deformation and/or brittle fracture. For hard and
brittle materials, the impact force of the abrasive particle causes localized cracks at the work surface.
The target material is removed by the formation and propagation of cracks with the subsequent impact events (Slikkerveer et al, 2000; Ligthart et al, 1996; Li et al, 2008). Modelling of the erosion rate is usually based on the studies of deformation caused by sharp indenters for brittle materials. According to the well-established erosion model for brittle materials (Ligthart et al, 1996; Lawn et al, 1980; Marshall et al, 1982; Marshall, 1984; Chiang et al, 1982), when a brittle material is loaded by a sharp indenter, a plastic zone is formed beneath the indent. At higher loads, a radial crack may propagate downwards from the base of the plastic zone. This crack does not contribute to the material removal but can degrade the material strength. On unloading, a lateral crack propagates at the base of the plastic zone. The lateral crack formation literally takes place parallel to the material surface, and strongly relates to the material removal phenomenon. It is believed that the normal component of impact energy is responsible for material removal in the brittle nature. In the 1930s, a low-pressure water jet system was patented and successfully used to cut paper [1]. Twenty years later, a high- pressure hydraulic seal from aviation industry was adopted to water jet machining, that noticeably increased the process productivity [2]. The continuous increase of working pressure in the next few decades allowed the cutting of hard alloys and carbides. On the other hand, a high pressure led to severe nozzle wear, making abrasive jet machining (AJM) economically non-competitive. From the 1970s, after ceramic nozzles were introduced, abrasive jet systems became commercially available and, within a short span of time, became the industrial mainstream and were mainly utilised for cutting and cleaning purposes. Further developments of AJM technology have been made, mainly based on material science progress and CNC conception. In the 21st century, AJM development deviated its track to technology miniaturization, wherein the nozzle diameter plunged from macro to micro scale. Today, sapphire orifice, super- hard abrasives and reliable high- pressure pumps combined with a 6-axis, precisely manage and process monitored systems, making AJM one of the most promising micro-manufacturing technologies despite the fact that it has been used for a century. In the last 25 years, there is a solid growing trend of industrial interest in micro-AJM.
Fig: 1 working of abrasive jet machining
MATERIAL REMOVAL MECHANISM:
Erosion is conventionally considered as a negative phenome-non, producing damage to structures. In the conception of free abrasive machining, erosion becomes an instrument, where AJM is a manufacturing technology, which is based on erosion localization and intensification. Directed flow of hard micro-particles splits-off the tiny chips from the substrate, removing workpiece mass to required geometrical conditions. Depending on materials proper- ties and process parameters, ductile or brittle removal mecha-nisms may dominate during erosion. The third one, namely elastic removal mode was discovered recently. The understanding of material removal mechanism is essential for machining efficiency enhancement.
BRITTLE MATERIAL REMOVAL MODE:
Numerous studies were devoted to an explanation of MRM in brittle materials after directive works of Marshall, Lawn,
and Evans. Briefly, the deformation and cracking model that occur during particles impact with a surface are typically those known from quasi-static Vickers- indentation theory. The ideal cracks pattern is represented schematically in Figure. Particles indentation creates compressive stress in the material beneath that forms a plastically deformed area. When the fracture threshold is exceeded, a radial crack perpendicular to the surface propagates downwards and aside from the base of the deformed area. During unloading stage, the lateral crack occurs at bottom of the plastically deformed volume and extends parallel to the surface. The radial crack does not affect the chip formation, nevertheless it degrades the surface integrity. It is generally accepted that the lateral crack determines the removed volume, assuming the chip size as a hemisphere with a volume dependent on lateral crack radius and depth of origination. Correspondingly, the radius of lateral crack and the depth of its initiation are considered to be the explanation of erosion phenomenon.
Fig: 2 Fragmentation from the single impact of SiC particle with Al2O3 substrate
PLASTIC MATERIAL REMOVAL MODE:
The primary ductile removal mechanism at normal impact is still under discussion. In contrast to shalow impact angles, where material removal is well explained through the cutting process, ductile erosion at normal impact is a polyhedral combination of process kinematics with dynamic material properties. After a final summary of the basic mechanisms by which solid particles may remove soft material pointed out by Finnie, no great fundamental
clarifications were introduced. The low-cycle fatigue mechanism was used to introduce erosion ductility, which is conceived to be an as essential material characteristic responsible for the critical plastic strain. Another erosion parameter was formulated considering the energy criterion during erosion and incorporates the materials hardness, along with the high-strain-rate stress strain response of the substrate. However, these approaches are targeted on quantitative evaluation of
volume removal and shined little light on the physical mechanism of material removal. A new elasticplastic analysis was proposed to predict the crater parameters and rebound velocity that can be used to calculate the amount of plastically deformed material appearing at the edges of the impact crater. It is known that the deeper into the crater, the more resistant the substrate becomes. The work of hardening during impact is very difficult to evaluate. Dynamic hardness widely applied in erosion models, e.g. reveals to be more of a functional value rather than a material property, depending greatly on erosion conditions such as particle material, size, and velocity, coating thickness, etc. For instance, dynamic hardness of PMMA may vary from 970 MPa to 2600 MPa depending on testing conditions. It is unlikely that current micro-blasting conditions (3 30-mm particles) can be reliably imitated in dynamic hardness testing.
ELASTIC REMOVAL MODE:
Material removal in ductile or brittle mode, based on deformation and consequent crack propagation, inevitably lead to a change of sub-surface structure. Surface integrity mostly depends on particle size. Finer grains produce smaller plastic flow and depth of impaired surface. Reduction of particles size from 120 nm down to 40 nm still have an influence over MRR, although produce no statistical effect on surface roughness. In other words, material removal with nanoparticles may not be related to deformation and cracking. It was concluded that the removal mechanism was shifted from indentation mechanism to surface-area mechanism. The particles
trajectory model demonstrates that the abrasive particle with a diameter less than 100 nm, turns away with the fluid flow just above the collision surface.
PROCESS PARAMETERS:
AJM process is affected by the number of settings. Some factors may contribute differently depending on the combination of other factors and materials properties. Although, several dominating tendencies can be underlined. The independent process param-eters involved in AAJM were classified by Hashish into two general groups and later into three groups by the Nouraei et al., which are discussed below.
Nozzle pressure: Pressure directly affects flow velocity and, as an aftermath, the kinetic energy of the in-flow particles. Thus, an increase in pressure leads to the growth of MRR and surface roughness. In AAJM, working pressure may vary from 0.2 to 1 MPa, that usually corresponds to 100- 300 m/s of particle velocity. During pre-coating machining for improvement of coated layer bonding to zirconia substrate, a working pressure less than
-
MPa was recommended.
Jet velocity: Due to boundary conditions between air jet and stable surroundings, abrasive jet velocity is non- uniform in both radial or axial direction. Li et al. conditionally divided air flow into three velocity regions. In the initial region, jet velocity preserves its speedinaformofconuswithabaseatthenozzleexit.Thehighness of the conus is independent of the jet velocity at the nozzle exit. Instead, it is proportional to its diameter and flow viscosity.
Fig: 3 Scheme of the conditional division of jet velocity regions (left) and microscope images of the AJM jet (right)
Traverse speed: Traverse speed is a speed of the reciprocal motion of the blasting nozzle relative to the machined surface. The speed selection is based on requirements of feature geometry. In precise etching by micro-blasting, the speed may fall down to 0.25 mm/s. The slower speed provides deeper erosion spot. Particle distribution in a flow cross section has normal character, consequently, the abrasive jet produces Gaussian shape footprint with a bottom at the distribution centre. However, at some conditions, the machined profile can turn to the flat or even convex pattern, as was reported recently.
Feed step: Feed step is a length of nozzle axis shift for each path alongside the previous one. Correct sequential
groves overlapping with a small erosion depth may be considered as polishing. With an eye to provide a small pick to valley value of machined surface, the feed step should be small enough to conjugate the flat regions of two bottoms, otherwise, sinusoidal surface profile occurs.
Stand-off-distance: Stand-off-distance is the distance between the nozzle exit and machined surface. Moving from conventional sand-blasting to powder-blasting, SOD was shortened from a few meters to several hundreds of micrometres.
Incidence angle: Incidence or impact angle is an angle between nozzle axis and machined surface. Depending on the target hardness, nozzle inclination causes different
aftermaths. Large angles (close to 90°) provide higher MRR in brittle materials, particularly in ceramics, while the soft workpiece is cut more efficiently with the angles at around.
Abrasive size: Abrasive size is one of the most influential factors in any AJM modification. By increasing the particles size, the single grain obtains bigger mass and volume, that directly affect its kinetic energy, which in turn
influences MRR. An increase in particle size is limited by the nozzle diameter. Particles interactions within the stream can reveal a problem, even when the particle diameter is 15 times less than that of nozzle. In general, the increase of abrasive fraction leads to chips enlarging and surface roughening. However, machining the sintered ceramics using 25-mm and 10-mm alumina particles at the same conditions.
Fig: 4 Particles trajectory at first- and second-strike
Abrasive hardness: Abrasive hardness directly exerts to MRR. Wakuda et al. blasted various ceramic substrates by abrasives with comparable angular shape and size, but different Knoop hardness. As it can be seen from Table 1, in the case of ZrO2 substrate, the erosion rate was almost independent of the abrasives hardness, such as workpiece hardness which was substantially lower than the hardness of any abrasives. For harder ceramics, the erosion rates were noticeably less for aluminium oxide and silicon carbide particles, although, not for synthetic diamonds. It was concluded that when the hardness of abrasives is close to substrates hardness, some part of the kinetic energy may be converted to deformation, heating, and fracture of the particles itself. On the other hand, when superhard particles were directed to the soft substrate, above described embedding phenomenon may take place.
Flow rate: Abrasive flow rate is the mass of abrasive powder supplied to a mixing chamber per unit time. Typically, flow rate varies from around 1 g/min to 1 kg/min, depending on nozzle diameter and pressure. For micro-AAJM, it is typically up to 5 g/ min. In water-based AJM, flow rate may be expressed in particle mass per
volume of liquid, for instance, 40 g/l, or as a percentage of particles concentration in a slurry, where a range from 0.25% to 10% is usually investigated.
Nozzle Wear mechanism: Like most of the other machining technologies, all AJM methods are related to the issue of tool wear. The nozzle is the most vulnerable component of any abrasive jet system. The typical working scheme of the nozzle with a miing chamber is presented in Figure. High pressured energy carrier moves through the orifice to the inner chamber, where it is mixed with abrasive particles. Then, the mixture enters the nozzle tube, obtaining a directed motion and exits in a form of an abrasive jet. The wall of the mixing tube is multiply impacted by particles during the process, that leads to internal nozzle erosion and changes in the tube profile. Continuous increase of nozzle hole diameter leads to process instability due to rise in air flow rate, jet divergence, and footprint size. Such circumstances affect the MRR, surface waviness and preciseness in general. Therefore, the nozzle wear mechanism became an important technological topic in the improvement of AJM economic indicators.
Fig: 5 Typical constriction of AAJM nozzle with mixing chamber
Some referred work on abrasive jet machining
Used materials
Process parameters
Observations
References
Abrasive: Al2O3, Nozzle : WC
Nozzle dia.: 0.712 mm , Pressure:(9.81-29.43)×104
N/m2
Abrasive size: 25,30,38, 48 m
Larger SOD is useful for deburring and finishing whereas micro drilling should be carried out at smaller SOD.
Verma et al. (1984)
Work piece:ZrO2 ,, Al2O3, SiC
Abrasive:Al2O3,SiC, Synthetic diamond (SD)
Nozzle : WC
Nozzle dia.: 0.6 mm Pressure: 0.3 MPa Abrasive flow rate: 2
gm/min Machining time: 10 s
Abrasive: 5-25 m
In this work, strength degradation of surface did not take place for the AJM of ceramic materials. The radial cracks did not propagate downwards by particle impacts during the machining process which result in damage free surface.
Wakuda et al. (2002)
Work piece: Glass fibre reinforced plastic Abrasive: SiC Nozzle: WC
Nozzle dia.: 1.2, 1.5, 2.3mm
Air pressure: 55, 60, 65 psi
SOD: 8, 10& 12 mm
Abrasive : 70 m
The MRR increases with increasing pressure and nozzle dia. but with increasing SOD decreases MRR.
Overcut and taper cut decreases with increase in pressure and nozzle diameter and decrease in SOD.
Sharma et al. (2014)
Work piece: Glass Abrasive: SiC, sand Nozzle: Brass
Pressure: 4, 4.3, 4.6, 4.8,
5.2 bar
Nozzle dia. : 1.5 mm
The pressure had direct impact on MRR.
Rout et al. (2014)
Work piece: Glass Abrasive: SiC Nozzle: WC
Pressure: 7, 7.5, 8 bar
SOD: 6, 8 , 10 mm
Abrasive size : 50, 90 m
Designed, developed and fabricated a model of AJM for performing drilling experiments.
The MRR depends significantly on abrasive size and pressure whereas taper angle only depends on pressure.
Shriyan et al. (2015)
MRR EVALUATION:
MRR can be evaluated by Equation (1); where the weight loss over the test period is divided by the time of the test in minutes.
MRR = (w b wa)t (g/min)
Where wb is the mass of work piece before the process began, wa is the mass of work piece after the process ended, and t is the machining time in minutes. The machining time for each trial was the time taken to obtain a hole completely through the
test piece. This, of course, varied depending on the given cutting conditions.
SOME FUTURE SCOPE OF ABRASIVE JET MACHINING:
By using dust collecting system and air filter, the environmental loading and hazards can be eliminated for eco-friendly machining. Beyond a number of traditional applications, some futuristic applications of abrasive jet are,
-
Cutting tools blasting after grinding.
-
Abrasive jet etching.
-
Surface cleaning prior to welding.
-
Cryogenic abrasive jet for machining polymers.
-
CONCLUSIONS:
AJM is a progressive manufacturing method with a growing role in the satisfaction of recent and oncoming industrial demands. With that, future investigations on technology enhancements are required. The trend of AJM developments is a shift from the macro to micro scale. Further reduction of machining spot, precise erosion predictability and process controlling are current challenges in AJM. A variety of AJM methods and developments have been analyzed. Submerged, intermittent and multi-jet conditions were found to be beneficial for environmental purposes, deep patterning and large area machining, correspondingly. AAJM is highly competitive in fabrication of surface micro-texture for tribological purposes. The minimum width of channel achieved by masked micro-blasting is 10 mm. Nevertheless, a feature size less than 5 mm was suggested for further improvements in surface frictional behaviour. Therefore, the increase of surface micro- patterning resolution presents an interest in several industries. Liquid-based abrasive jet polishing has lower MRR than AAJM but provides better surface roughness. With an eye to combine both advantages, an attempt to build a bridge between air and water- based abrasive jet systems was presented as CAAJM.
REFERENCES:
-
Achtsnick, M., Geelhoed, P. F., Hoogstrate, A. M. & Karpuschewski, B. 2005, Modeling and evaluation of the micro abrasive blasting process, Wear, Vol. 259, No. 1-6, pp. 84-94.
-
Chiang, S. S., Marshall, D. B. & Evans, A. G. 1982, The response of solids to elastic/plastic indentation. I. Stresses and residual stresses, Journal of Applied Physics, Vol. 53, No. 1, pp. 298-311.
-
Farimani, A. F. 2010, Abrasive Jet Micromachining of Quartz Crystals, ME Thesis, The University of New South Wales.
-
Ghobeity, A., Ciampini, D. & Papini, M. 2009, An analytical model of the effect of particle size distribution on the surface profile evolution in abrasive jet micromachining, Journal of Materials Processing Technology, Vol. 209, No. 20, pp. 6067-6077.
-
Syazwani, H., Mebrahitom, G., Azmir, A., 2016, A Review on Nozzle Wear in Abrasive Water Jet Machining Application. IOP Conference Series: Materials Science and Engineering, 114:210. http://dx.doi.org/10.1088/1757-899X/ 114/1/012020.
-
Molitoris, M., Pitel, J., Hosovsky, A., Tothova, M., Zidek, K., 2016, A Review of Research on Water Jet with Slurry Injection. Procedia Engineering, 149:333 339. http://dx.doi.org/10.1016/j.proeng.2016.06.675.
-
Kalpana, K., Mythreyi, O.V., Kanthababu, M., 2015, Review on Condition Monitoring of Abrasive Water Jet Machining System. Proceeding of 2015 International Conference on Robotics Automation Control and Embedded Systems (RACE), 2015. http://dx.doi.org/10.1109/RACE.2015.7097254.
-
Wakuda, M., Yamauchi, Y., Kanzaki, S., 2002, Effect of Workpiece Properties on Machinability in Abrasive Jet Machining of Ceramic Materials. Precision Engineering, 26:193 198. http://dx.doi.org/10.1016/S0141-6359(01)00114-3.
-
Li, Z.Z., Wang, J.M., Peng, X.Q., Ho, L.T., Yin, Z.Q., Li, S.Y., Cheung, C.F., 2011, Removal of Single Point Diamond-turning Marks by Abrasive Jet Polishing. Applied Optics, 50:2458. http://dx.doi.org/10.1364/AO.50.002458.
-
Haghbin, N., Spelt, J.K., Papini, M., 2015, Abrasive Waterjet Micro-machining of Channels in Metals: Comparison Between Machining in Air and Submerged in Water. International Journal of Machine Tools and Manufacture, 88:108 117. http://dx.doi.org/10.1016/j.ijmachtools.2014.09.012.
-
Li, H.-C., Chen, W.-S., 2017, Recovery of Silicon Carbide from Waste Silicon Slurry by Using Flotation. Energy Procedia, 136:5359. http://dx.doi.org/ 10.1016/J.EGYPRO.2017.10.281.
-
Kim, J.-Y., Kim, U.-S., Byeon, M.-S., Kang, W.-K., Hwang, K.- T., Cho, W.-S., 2011, Recovery of Cerium from Glass Polishing Slurry. Journal of Rare Earths, 29:10751078. http://dx.doi.org/10.1016/S1002-071(10)60601-1.
-
Nouraei, H., Wodoslawsky, A., Papini, M., Spelt, J.K., 2013, Characteristics of Abrasive Slurry Jet Micro-machining: A Comparison with Abrasive Air Jet Micro-machining. Journal of Materials Processing Technology, 213:1711 1724. http://dx.doi.org/10.1016/j.jmatprotec.2013.03.024.
-
Matsumura, T., Muramatsu, T., Fueki, S., 2011, Abrasive Water Jet Machining of Glass with Stagnation Effect. CIRP Annals Manufacturing Technology, 60:355358. http://dx.doi.org/10.1016/j.cirp.2011.03.118.
-
Kowsari, K., Papini, M., Spelt, J.K., 2017, Selective Removal of Metallic Layers from Sintered Ceramic and Metallic Plates Using Abrasive Slurry-jet Micro-machining. Journal of Manufacturing Processes, 29:252264. http://dx.doi. org/10.1016/j.jmapro.2017.08.005.
-
Narayanan, C., Balz, R., Weiss, D.A., Heiniger, K.C., 2013, Modelling of Abrasive Particle Energy in Water Jet Machining. Journal of Materials Processing Technology, 213:22012210. http://dx.doi.org/10.1016/j.jmatpro- tec.2013.06.020.
-
Gupta, V., Pandey, P.M., Garg, M.P., Khanna, R., Batra, N.K., 2014, Minimization of Kerf Taper Angle and Kerf Width Using Taguchis Method in Abrasive Water Jet Machining of Marble. Procedia Materials Science, 6:140149. http://dx. doi.org/10.1016/j.mspro.2014.07.017.
-
Vasanth, S., Muthuramalingam, T., Vinothkumar, P., Geethapriyan, T., Murali, G., 2016, Performance Analysis of Process Parameters on Machining Titanium (Ti-6Al-4V) Alloy Using Abrasive Water Jet Machining Process. Procedia CIRP, 46:139142. http://dx.doi.org/10.1016/j.procir.2016.04.072.
-
Shukla, R., Singh, D., 2017, Experimentation Investigation of Abrasive Water Jet Machining Parameters Using Taguchi and Evolutionary Optimization Techniques. Swarm and Evolutionary Computation, 32:167183. http://dx. doi.org/10.1016/j.swevo.2016.07.002.
-
Ahmed, D.H., Naser, J., Deam, R.T., 2016, Particles Impact Characteristics on Cutting Surface During the Abrasive Water Jet Machining: Numerical Study. Journal of Materials Processing Technology, 232:116130. http://dx.doi.org/ 10.1016/j.jmatprotec.2016.01.032.
-
Hejjaji, A., Zitoune, R., Crouzeix, L., Le Roux, S., Collombet, F., 2017, Surface and machining induced damage characterization of abrasive water jet milled carbon/epoxy composite specimens and their impact on tensile behavior. Wear, 376377:13561364. http://dx.doi.org/10.1016/j.wear.2017.02.024.
-
Kumaran, S.T., Ko, T.J., Uthayakumar, M., Islam, M.M., 2017, Prediction of Surface Roughness in Abrasive Water Jet Machining of CFRP Composites Using Regression Analysis.
Journal of Alloys and Compounds, 724:10371045. http:// dx.doi.org/10.1016/j.jallcom.2017.07.108.
-
Cojbasic, Z., Petkovic, D., Shamshirband, S., Tong, C.W., Ch, S., Jankovic, P., Ducic, N., Baralic, J., 2016, Surface Roughness Prediction by Extreme Learning Machine Constructed with Abrasive Water Jet. Precision Engineering, 43:86 92. http://dx.doi.org/10.1016/j.precisioneng.2015.06.013.
-
Lathabai, S., Pender, D.C., 1995, Microstructural Influence in Slurry Erosion of Ceramics. Wear, 189:122135. http://dx.doi.org/10.1016/0043-1648(95) 06679-9. [25] Levy, A.V.,