
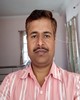
- Open Access
- Authors : K. C. Santhosh , Dr. B. K. Muralidhara
- Paper ID : IJERTV10IS040323
- Volume & Issue : Volume 10, Issue 04 (April 2021)
- Published (First Online): 04-05-2021
- ISSN (Online) : 2278-0181
- Publisher Name : IJERT
- License:
This work is licensed under a Creative Commons Attribution 4.0 International License
A Study on Tribological Properties of Thermally Oxidized Titanium alloy
K. C. Santhosp
1 Research Scholar, Department of Mechanical Engineering, UVCE, K.R. Circle, Bangalore University,
Bangalore-560001, Karnataka, India
Dr. B. K. Muralidhara2
2 Professor and Former Dean, Bangalore University, Bangalore-560001, Karnataka, India
Abstract:- Titanium alloy sample Ti8Al1Mo1V in As Received condition(ASR) is subjected to solutionising and ageing heat treatment followed by air cooling(STA) are subjected to Thermal oxidation at 600°C, 750°C and 900°C temperature for 6 hours, 15 hours and 24 hours duration each in a resistance furnace in presence of air followed by furnace cooling. The samples To6-600, To6-750, To6-900, To15-600, To15-750, To15-
900, To24-600, To24-750 and To24-900 are subjected to two different wear tests: 1. Dry sand Abrasive wear in ducoms abrasive tester. 2. Pin on disc wear test under dry sliding conditions. The abrasive wear samples and Pin on disc wear samples are examined in scanning electron microscope to study the mechanism of wear.3.Surface roughness factor is measured in order to analyse the surface finish achieved due to solutionising and ageing heat treatment and thermal oxidation heat treatment.
Thermal oxidation is helpful in achieving good surface finish for Titanium alloy Ti8Al1Mo1V at temperature of 600°C and duration of time up to 15 hours beyond which it degrades with temperature and duration. From wear tests the thermally oxidized titanium samples exhibit very good wear resistance up to 900°C temperature irrespective of duration of oxidation. At 750°C temperature and 24 hours duration it shows good wear resistance.
Keywords: As received (ASR), Solution treated and Aged (STA), Thermal oxidation, Titanium, surface roughness
-
INTRODUCTION
Titanium and its alloys are widely used in Aerospace applications due to combination of high strength, stiffness, good toughness, fatigue strength, low density and excellent corrosion resistance at service temperatures ranging from very low(-250°C) to moderately elevated temperature(560°C) with considerable weight savings. Titanium has two allotropic forms namely Alpha-titanium (hcp crystal structure), below 882°C, and Beta Titanium (bcc crystal structure), above this temperature. Alloying elements which raise the transition temperature are called alpha-stabilizers, while those lowering it are known as beta-stabilizers. Aluminum, carbon, oxygen and nitrogen are alpha-stabilizers. While chromium, cobalt, copper, iron, manganese, molybdenum, nickel and vanadium are beta stabilizers. Zirconium and Hafnium have no effect on alpha/beta phases. Depending on the type and quantity of alloying elements, titanium alloys may have fully alpha or beta phase or a mixture of alpha and beta phases at ambient temperatures and are classified into groups such as, alpha() alloys, near alpha() alloys alpha-beta() alloys and beta() alloys. Alpha alloys are non-heat treatable. They possess medium strength, good oxidation resistance up to 550°C, and
excellent fracture toughness under cryogenic conditions and are structurally very stable in prolonged elevated temperature exposures. Near alpha alloys have similar characteristics as alpha alloys except that these alloys can be strengthened by solution treatment and ageing. These alloys exhibit good creep and elevated temperature fatigue strength. Alpha-beta alloys are widely used for aerospace applications. These can be strengthened by solution treatment and ageing, and exhibit superplasticity under certain processing conditions. These alloys are less stable at high temperature and show poorer creep characteristics than alpha and near alpha alloys. Beta alloys develop very high strengths on solution heat treatment and ageing heat treatment. Strength levels obtained on heat treatment are however, sensitive to prior thermal processing history. These alloys have excellent tensile strength up to 370°C but above this temperature these have poor creep and tensile properties. Titanium alloys have some disadvantages, the most significant of which are a high cost, a low surface hardness, and a low wear resistance. The low surface hardness and wear resistance limit the use of titanium alloys under conditions of friction and contact loads. The Tribological characteristics of titanium alloys are improved by various means which include plasma methods, laser methods, ion implantation, and PVD and CVD technologies. All these surface treatment can be divided into three groups. The first group is aimed primarily at changing the microstructure of the surface layer (without changing the chemical composition) by using high temperatures and heating and cooling rates. The second group includes methods of creating a coating on the matrix material. The third and largest group includes various kinds of thermochemical treatment (TCT) of titanium alloys such as nitriding, carburizing, oxidizing, and nitro oxidizing [7]. The thermal oxidation process is one of the most important advances in the field of surface engineering of Ti- based materials due to its capability of enhancing the Tribological properties of Ti alloys [1]. Ti-6Al-4V alloy treated using thermal oxidation exhibited low coefficient of friction and low wear rate, which is attributed to both the formation of a useful oxide and hardened diffusion layer. Many non metallic elements are used to enhance the titanium alloy surface to improve its Tribological properties, which can form a hardened, interstitially enriched alpha-case layer with or without an outer surface layer of hard compound. [2] Thermal oxidation is one of the widely used thermochemical treatment for titanium alloys. In the process oxygen is incorporated in to the surface layers of titanium base alloys at elevated temperatures and yields various combinations of
improved properties. In principle it is possible to improve the surface hardness, wear resistance and fatigue resistance and improve the appearance of the surface of treated parts. In the present investigation Ti8Al1Mo1V alloy is considered for study which is a near alpha alloy. The applications of Ti8Al1Mo1V include compressor blades, turbine discs, housing inner skin and frame for nozzle assembly of Jet engines. Literature review indicates that published information not available regarding systematic reporting of improvement in tribological properties of Ti-8Al-1Mo-1V through thermal oxidation. Hence in the present investigation it is proposed to take up systematic study on improving the tribological properties of Ti-8Al-1Mo-1V alloy through solutionising and ageing followed by air cooling and thermal oxidation heat treatments.
-
EXPERIMENTAL DETAILS:
Titanium alloy received in the form of Rectangular bar of 45mm*50mm*500mm is cut in to pieces of required dimension. The cut pieces of alloy are cleaned thoroughly using cleaning agent and applied two layers of protective coating before loading to furnace for solutionising heat treatment. The alloy pieces are subjected to solutionising heat treatment at 899 to 1010 ºC for 1 hour followed by stabilization treatment at temperatures of 595 ºC for 8 hours followed by air cooling in a resistance furnace as per AMS4933F standard. Further the solutionised, heat treated and air cooled specimens (designated as STA) are machined to prepare specimens for abrasive wear test, pin on disc wear test and microstructure studies with the dimensions explained below as per ASTM standards.
For abrasive wear test the specimen dimension is 25mm*75mm*10mm rectangular plate, for pin on disc wear test the specimen dimensionis 10mm dia with 25mm length and one end of it is machined to hemisphere of 5 mm nose radius. For microstructure study the dimension of sample is 10mm*10mm*10mm.
The prepared specimens are subjected to thermal oxidation in presence of air in a resistance furnace at 600°C, 750°C and 900°C temperatures for durations of 6 hours, 15 hours and 24 hours each. The thermally oxidized samples are designated as To6-600, To6-750, To6-900, To15-600, To15-750, To15- 900, To24-600, To24-750 and To24-900.
The Surface roughness factor or Ra factor of Ti8Al1Mo1V alloy samples in As received condition (ASR), solutionised aged and air cooled (STA) samples and thermally oxidized conditions were determined in Taylor Hobson surface roughness measuring instrument at a depth of 0.25 micro meters.
-
Pin on disc wear test 🙁 Metal to Metal wear test)
The thermally oxidized samples are subject to friction and wear test on Ducoms Pin on Disc Apparatus under dry sliding conditions as per ASTM standards G99-95a. The pin on disk apparatus is having a steel disc with hardness of 63 HRC, and the load applied for the test is 2kgf (19.62N). The track radius and speed of rotation of the disc is 60 mm and 400rpm respectively. The prepared specimen with the dimensions explained above is fixed in a tool holder with the hemispherical surface towards the rotating disc and the wear test is carried out by bringing hemispherical surface to be in
contact with rotating steel disc by adding weight as per the process parameters explained above for 20 minutes duration. After the wear test the wear scar diameter of each sample is measured and the wear weight loss is estimated and presented in table 2. The wear surfaces are studied in scanning electron microscope and the micrographs obtained are presented in figure 4.
-
Abrasive wear test:
Abrasive wear test was carried out on sample of rectangular plate of 25 mm*75mm*10mm thickness prepared as per ASTM standard by fixing the sample in the specimen holder of ducoms dry abrasion tester and the test is carried out with the process parameters explained below.
Abrasion tests were carried out on Ducoms Dry Abrasion Tester (TR-50) equipment as per ASTM G65 standard with the following process parameters:
-
Sand flow rate is 60 gram/minute
-
Load Applied is 28.56 N(3 kgf)
-
Dia of Rubber disc 228.6 mm
The test is carried out for different revolutions of rubber wheel i.e. for different contact distance to study the wear volume loss at different intervals. The samples are cleaned thoroughly and washed in cleaning agent and weighed to four decimal accuracy in an electronic weighing scale before and after each test. The abrasive used for the test is rounded quartz sand grains of AFS 50/70 grade. The results obtained are presented in table 4. Further the abraided surfaces of samples subjected to abrasive test are examined in scaning electron microscope to understand the wear pattern of the alloy which is presented in figure 9.
-
-
Surface roughness factor (Ra):
Surface roughness factor Ra is measured for samples subjected to thermal oxidation at 600°c, 750°c and 900°c for
6 hours, 15 hours and 24 hours duration. Also surface roughness factor is measured for samples in As received condition (ASR) and Solution treated aged and air cooled condition (STA). The results are presented in table 1.and the comparative graph is plotted with Alloy condition against surface roughness factor Ra which is presented in figure 10.
3. RESULTS AND DISCUSSION
-
Pin on disc wear test
Pin on disc test was carried out with the following process parameters.
Table 1. Process parameters for pin on disc wear test
Test parameter
value
Radius of pin head mm
5
Revolutions/ Minute of disc
400
Track radius, mm
60
Duration of test, minutes
20
Sliding distance, m
6031.85
Sliding velocity, m/sec
5.026
The coefficient of friction is calculated from the results obtained from pin on disc wear test and the coefficient of friction values are plotted against the type of alloy conditions which are represented in figure 1. It is found that the alloy sample oxidised to 900°C temperature for 6 hours duration shows the coefficient of friction value as the highest.
Table 2. Wear volume loss and coefficient of friction in POD test of Ti8Al1Mo1V alloy in thermally oxidised condition
Sl. N
o.
Sample designation
Wear scar diamet er, mm
Wear volume loss/unit sliding distance
Coefficient of friction
Value mm3/ m
Change in propert y percent age*
value
Change in property percentag e*
(1)
(2)
(3)
(4)
(5)
(6)
(7)
1
ASR
6.280
15.26
0.671
0.2897
6.35
2
STA
5.685
10.25
0
0.2713
0
3
To-6-600
6.425
16.729
0.612
0.2898
6.38
4
To-15-600
6.765
20.56
0.498
0.3008
9.8
5
To-24-600
7.125
25.3
0.405
0.2854
4.94
6
To-6-750
6.465
17.15
0.5976
0.2969
8.62
7
To-15-750
6.695
19.72
0.519
0.3029
10.43
8
To-24-750
1.510
0.0510
200.98
0.3820
28.97
9
To-6-900
1.895
0.1266
80.96
0.4533
40.15
10
To-15-900
1.140
0.0165
8
618.21
0.3831
29.18
11
To-24-900
1.370
0.0362
5
282.7
0.3873
29.95
*As compared to the value of respective property of the alloy in STA condition, which is given as follows: wear volume loss/unit sliding distance=10.25mm3/m, coefficient of Friction=0.2713
Figure 1. Plot of coefficient of friction against sample condition
Figure 2. Plot of weight loss against sample condition
Pin on disc wear test reveals the coefficient of friction value of thermally oxidized sample is 67% more (To6-900) than the specimen in STA condition. The coefficient of friction of
To15-900 is 41.2% more, To24-900 is 42.75% more and To24-750 is 40.8% more than samples in STA condition. The coefficient of friction value increases with temperature irrespective of time duration. The least weight loss value is noticed in sample To15-900 which is 98% less than the alloy in STA condition. The low weight loss value noted in samples To6-900 is 87.7%, To24-750 is 95% and To24-900 is 146% less as compared to the alloy in STA condition. In contrast the highest weight loss value is noticed in sample To24-600 which is 1.5 times more than the value in the alloy in STA condition due to non uniform oxidized outer layers which are non adherent to subsurface to titanium alloy. At 750°C, and 900°C temperatures and 24 hours duration of thermal oxidation, the wear resistance exhibited by the alloy is excellent as compared to the alloy in STA condition.
The SEM micrographs of samples of Pin on disc test represented in figure3 shows, the samples undergo plastic deformation due to repeated sliding of samples over the steel disc. In case of thermally oxidized samples, wearing out of outer surface layers and mild plastic deformation of the inner layers are the common features to be noticed in the worn out surfaces. The wearing out of outer surface layer takes place by the process of delamination. It is found that the material is abraided layer by layer. For the samples in ASR, STA, To6- 600, To6-750, To15-600, To15-750 and To24-600 a series of wear tracks and ripped surfaces are found along with delaminated layers and cracked edges is noticed. But the samples To6-900, To15-900, To24-750, To24-900 exhibits surface with very less marks of delaminated surface.
POD scar of ASR
POD scar of STA
POD scar of TO6-600
POD scar of TO6-750
POD scar of TO6- 900
POD scar of TO15-600
POD scar of TO15-750
POD scar of TO15- 900
POD scar of TO24-600
POD scar of TO24-750
POD scar of TO24- 900
Figure 3. SEM micrographs of alloy samples after POD test
-
Free body Abrasive Wear Test: The free body abrasive wear test is carried out with following process parameters with different contact distance which are presented in Table 3.
From The abrasion test for sliding distance of 35.93m, the samples To6-750 and To24-900 showed very minimum wear weight loss and at 600°C temperature of oxidation the variation in wear weight loss is negligible irrespective of duration of oxidation. For sliding distance of 71.78m except To6-600 remaining oxidized samples shown negligible wear weight loss. For sliding distance of 143.63m except To6-600 and To6-750 remaining samples shown very negligible wear weight loss. For sliding distance of 287.26m except To6-600 and To15-600 remaining samples showed very negligible wear weight loss. The minimum wear weight loss exhibited by thermally oxidized samples after abrasion test is 99% as compared to the alloy sample in STA condition. The wear scar of Abrasive wear test are subjected to SEM analysis and the micrographs are presented below in figure 9.
Table 3. Process parameters for Abrasive wear test
Sl no
Number of Revolutions of rubber wheel
Number of Rotations per Minute (RPM)
Contact Distance, m
1
200
50
35.93
2
100
100
71.78
3
50
50
143.63
4
400
150
287.26
Figure 5 plot of wear weight loss for sliding distance of 35.93m against alloy condition
Figure 6. plot of wear weight loss for sliding distance of 71.78m against alloy condition
Figure 7. plot of wear weight loss for sliding distance of 143.63m against alloy condition
Figure 8. plot of wear weight loss for sliding distance of 287.26m against alloy condition
SEM of abraided ASR
SEM of abraided STA
SEM of abraided TO6-600
SEM of abraided TO6-750
SEM of abraided TO6-900
SEM of abraided TO15-600
SEM of abraided TO15-750
SEM of abraided TO15-900
SEM of abraided TO24-600
SEM of abraided TO24-750
SEM of abraided TO24-900
SEM of abraided ASR
SEM of abraided STA
SEM of abraided TO6-600
SEM of abraided TO6-750
SEM of abraided TO6-900
SEM of abraided TO15-600
SEM of abraided TO15-750
SEM of abraided TO15-900
SEM of abraided TO24-600
SEM of abraided TO24-750
SEM of abraided TO24-900
Table 5. Surface roughness factor measured for different alloy condition
SAMPLE DESIGNATION
SURFACE ROUGHNESS FACTOR
Ra µm
ASR
0.9645
STA
1.4621
TO-6-600
0.2115
TO-6-750
0.3166
TO-6-900
0.6193
TO-15-600
0.2695
TO-15-750
0.3617
TO-15-900
0.7191
TO-24-600
0.7341
TO-24-750
0.7222
TO-24-900
0.3507
SAMPLE DESIGNATION
SURFACE ROUGHNESS FACTOR
Ra µm
ASR
0.9645
STA
1.4621
TO-6-600
0.2115
TO-6-750
0.3166
TO-6-900
0.6193
TO-15-600
0.2695
TO-15-750
0.3617
TO-15-900
0.7191
TO-24-600
0.7341
TO-24-750
0.7222
TO-24-900
0.3507
Figure 9. SEM Micrographs of abraided surfaces after abrasive test for various alloy conditions
SEM Micrographs of abraided surfaces after abrasive test revealed the samples in thermally oxidized condition, wearing of outer surface layers and mild plastic deformation of inner layers are common features to be noted in worn out surfaces. The wearing of outer layer takes place by the process of delamination and material is abraided layer by layer, wear debris are also seen. Compound layer of TiO2 is formed in layers for samples thermally oxidized at 600°C for different duration and wear occurs, by delamination layer by layer and at 900°C there are only faint wear marks as the diffusion layer is not easily susceptible for wear.
-
surface roughness factor Ra
Figure 10. Plot of surface roughness factor against alloy condition
From surface roughness factor measurement it is revealed that the surface roughness of thermally oxidized samples is less compared to specimens in ASR and STA condition. The surface roughness factor is reduced by 85 % for the sample thermally oxidized sample To6-600, 81% for To15-600 and 75.4% for To24-600 samples as compared to sample in solutionised aged and air cooled condition (STA).
The surface roughness factor keeps increasing with temperature and duration of oxidation resulting in poor surface finish due to oxide layers formed have no uniform adherence to the subsurface and have tendency of peel off partially leaving a rough surface.
-
CONCLUSION:
Thermal oxidation is helpful in achieving surface finish for Titanium alloy Ti8Al1Mo1V at temperature of 600°C and duration of time up to 15 hours beyond which it degrades with temperature and duration due to peeling off of oxide coating formed during thermal oxidation.
From wear tests the thermally oxidised titanium samples exhibit very good wear resistance up to 900°C temperature irrespective of duration of oxidation. At 750°C temperature and 24 hours duration it shows good wear resistance out of the samples tested. The coefficient of friction value exhibited by the sample oxidized At 900°C temperature and 6 hours duration is the maximum at around 40% more than the sample in STA condition.
REFERENCES
-
Effect of thermal oxidation process on fatigue behavior of Ti-4Al- 2V alloy A.R. Ebrahimi, F. Zarei, R. A. Khosroshahi, Department of Materials Enginnering, Sahand University of Technology, Tabriz, Iran 23August2008,
-
Thermal Oxidised Coating on Surface of Titanium Alloy for improvement of Tribological Properties in Vacuum Yong Liu, Zhuyu Ye, Dezhuang Yang, Shiyu He Space Materials and Environmental Engineering Lab., Harbin Institute of Technology,
Harbin 150001, china
-
Analysis of friction and wear of titanium alloys Adarsh Mishra,
ISSN 2278-0149 www.ijmerr.com vol.3, No.3, july 2014
-
Tribological properties of titanium alloys Kenneth G. Budinski, Eastman Kodak company, Building 23, 5th Floor, Kodak park,
Rochester, NY14650(U.S.A) April 30, 1991
-
surface hardening of titanium by thermal oxidation W. YAN,
X.X. WANG Materials Science and Engineering, Zhejiang University, Hangzhou 310027, peoples republic of china
-
Influence of nitriding and oxidation on the wear of titanium alloys
-
M. Pohrelyuk, V. M. Fedirko, and V.M. Dovhunyk Materials Science, Vol., No.3, 2000
-
-
Nitriding of titanium and aluminium alloys-relation between the microstructure and properties of commertial titanium alloys and the parameters of gas nitriding S. Malinov, A. Zhecheva, and W. Sha Translated from Metallovedenie I Termicheskaya Obrabotka Metallov, No.7, pp.21-28, July, 2004.
-
Studies on Mechanical and Tribological Properties of Titanium Alloys Unpublished Thesis work By K. C. Santhosh, under guidance of Dr. B. K. Muralidhara, Bangalore University, Bangalore-560001, INDIA, 2021
-