
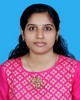
- Open Access
- Authors : Anjali P , Sajitha Beegom A
- Paper ID : IJERTV11IS010039
- Volume & Issue : Volume 11, Issue 01 (January 2022)
- Published (First Online): 17-01-2022
- ISSN (Online) : 2278-0181
- Publisher Name : IJERT
- License:
This work is licensed under a Creative Commons Attribution 4.0 International License
A Study on the Utilization of Activated Steel Slag as Partial Replacement of Cement in Concrete
Anjali P
-
ech Scholar, Dept. of Civil engineering College of Engineering Trivandrum
Kerala- 695016, India
Sajitha Beegom A
Assistant Professor, Dept. of Civil Engineering College of Engineering Trivandrum
Kerala 695016, India
Abstract Steel slag is an industrial by-product of steel manufacturing, characterized as highly calcareous, siliceous and ferrous. They are found to be useful in many fields, such as road construction, asphalt concrete, agricultural fertilizer, and soil improvement. Due to its ever increasing production and hazardous effects due to dumping of slag there is a need to study its effect on mortar and concrete with higher replacement ratios. The chemical composition of steel slag showed potential for use as cementitious component. However, the increased initial setting time and low early strength limits its widespread application in cement and concrete industries.
This paper explores the use of partially replacing cement with locally available steel slag activated with chemicals for making of cement mortar. The effects of steel slag fines on the initial setting time and compressive strength of cement mortar were studied. The suitability of steel slag using various chemical activators on improving the compressive strength and initial setting were also evaluated. The results showed that 18% steel slag fines and 4 % Na2SO4 results similar results to that of OPC.
KeywordsSteel slag fines, Alkali activators, Initial setting time, Compressive strength
-
INTRODUCTION
Global warming and environmental destruction have become the major issue in recent years. Emission of lots of greenhouse gases from industries results in several adverse impact on climate and this has changed the mind set of people. So currently people are trying to convert the mass-production, mass-consumption, mass waste society of the past decades to a zero-emission society. This target can be achieved by utilizing industrial wastes which in turn leads to conservation of natural resources. Preventing the depletion of available natural resources and thereby enhancing the usage of waste materials has become a challenge to the scientist and engineers. A number of studies have been conducted concerning the protection of natural resources, prevention of environmental pollution and contribution to the economy by using the waste materials.
Nowadays, concrete is one of the most preferred and the single largest building material used by the construction industry. The constituent materials of concrete includes coarse aggregate, fine aggregate, potable water and finally cement , which act as the binding agent that helps to glue these together. Each one of these constituents of concrete has a negative environmental impact and pose a threat to environmental sustainability. However the current concrete construction practice is unsustainable. This is because, production of
concrete not only it consumes enormous quantities of stones, sand, and potable water, but also billion tons of cement. Cement is not an environment friendly material. For production of cement huge amount of energy is needed and it leads to greater CO2 emissions. During production of cement around 8% CO2 is released to the atmosphere. In fact, many by- products and solid wastes can be used in concrete mixes as aggregates as well as cement replacement, depending on their chemical and physical characterization, if they are adequately treated.
Steel slag is a by-product of steel making and is produced when the molten steel is separated from impurities in the furnaces. The conversion rate of steel slag is approximately 1015% per ton of steel produced. This has created a serious environmental and social hazard in several aspects such as the occupation of agricultural land and the contamination of ground water and soil by the leached heavy metals contained in steel slag. Utilization of steel slag in civil engineering applications can alleviate the need for their disposal and reduce the use of natural resources. Research shows that SS has similar chemical and mineral compositions to Portland cement clinker, so it can be used as an active cement admixture. However, if the addition amount of SS reaches more than30%, the early strength of the cementitious material decreases drastically. Currently, the excitation methods used to improve the early strength and hydration activity of the SS cementitious material can be divided into three categories: (1) physical excitation, which refers to the use of physical methods to increase the specific surface area and lattice defect of SS to improve the lattice free energy and hydration activity (2) chemical excitation (alkali excitation), which refers to the addition of the early strength agent to increase the liquid alkalinity to promote the dissolution of vitreous of SS and improve the hydration activity and (3) thermodynamic excitation, which refers to increasing the temperature of the SS hydration reaction to increase the hydration rate and hydration activity.
-
MATERIALS AND METHODS
In order to investigate the influence of steel slag fines on the performance of cement mortar an experimental program was carried out. In this research program locally available steel slag fines were used. The steel sag used in the present investigation was collected from Sri Rengaraj Ispat Industries, Perundurai, Erode. The steel slag had reddish brown colour Steel slag fines were sieved to a size of cement particle (90 microns). By conducting Le Chatliers test the specific gravity of steel slag fines was found as 3.21 which is comparable to that of specific gravity of cement. Ordinary Portland Cement of
53 grade conforming to IS 12269-2013 was used for the study. Manufactured sand of fineness modulus 3.9 conforming to grade II was used as fine aggregate.
TABLE 1. CHEMICAL AND MINERALOGICAL COMPOSITION OF STEEL SLAG
Parameters
Slag (%)
IS 12089 limits
SiO2
37.63
Al2O3
14.32
Fe2O3
1.12
CaO
37.44
MgO
8.72
17% max
MnO
0.03
5.5% max
Sulphide
0.38
2% max
Glass content (%)
92.96
85%max
In order to evaluate the degree of activation under different chemical activators the four different activators of sodium hydroxide (NaOH), sodium sulphate (Na2SO4), sodium carbonate (Na2CO3), and sodium silicate (Na2SiO3·9H2O) were used. All were of pure analytical grade.
-
EXPERIMENTAL PROGRAMME
Here, standard mortar mixes with a ratio of 1:3 was prepared using different percentages of steel slag fines and cement as binder mix and M sand as fine aggregate. Then its properties like consistency, Initial setting time and compressive strength were determined.
-
Normal consistency for mortar
Normal consistency water requirement of binder mixes with different steel slag to cement ratio were determined corresponding to IS 4031: part 4 (1988). Paste mixes were made with the combination of binders and water with no aggregate with different proportions of steel slag fines and OPC and were cast and tested. The various proportions of steel slag and cement used for the reparation of steel slag cement mortar were shown in Table2.
TABLE 2. PROPORTION OF STEEL SLAG AND CEMENT USED FOR THE PREPARATION OF SCM (WT. %)
Parameter
Slag (%)
IS 12089 limits
S1-1
10
90
S1-2
20
80
S1-3
30
70
-
Initial setting time for mortar
The tests for determining the initial setting time of steel slag cement binder mixes were performed using Vicats apparatus confirming to IS 5513-1976.
-
Compressive strength for mortar
Cement mortar specimens were prepared as per IS 4031 Part-6 (1988) by replacing cement with steel slag fines. All the mixes were compacted mechanically with a vibrating table. The moulds were filled with mortar in three layers and compacted to remove the air and reach the maximum density. A hydraulic testing machine of 200 kN capacity was used for testing of compressive strength. The compressive strength at the end of 3, 7 and 28 days of curing were measured. By comparing the compressive strength the ratio of Steel slag to cement that meets the required strength was then selected. In order to get a more accurate optimum specimens were
prepared by replacing cement with steel slag fines by 16, 18 and 22 percentages.
-
Influence of chemical activators on SCM
In order to evaluate the degree of activation under different chemical activators on SCM, the experimental scheme in Table 3.was used for further experiments. The chemical activators of sodium sulphate, sodium silicate, sodium carbonate and sodium hydroxide with a dosage of 6 % were used to activate SCM. Then, the Initial setting time and compressive strength at the end of 3rd, 7th and 28 days of curing were measured. The chemical activator with the best activation effect was then selected.
TABLE 3. RATIO OF ADDITION OF ACTIVATORS TO SCM (%)
Sample No.
Steel slag fines (%)
Cement (%)
Chemical Activator
S2-1
18
82
6% – Na2SO4
S2-2
18
82
6% – Na2SiO3.9H2O
S2-3
18
82
6% – NaOH
S2-4
18
82
6% – Na2CO3
-
Determination of optimum percentage of alkali activator
In order to further study the effect of dosage of the selected alkali activator on SCM, Steel slag cement mortar specimens were prepared by the addition of best alkali activator found from the above step in the percentages as shown in the Table
-
The compressive strength of SCM were measured at 3, 7 and 28 days of curing to determine the optimal amount of alkali activator.
TABLE 4. PERCENTAGE ADDITION OF SELECTED ACTIVATOR
Sample No.
Chemical Activator
S3-1
1
S3-2
2
S3-3
3
S3-4
4
S3-5
5
S3-6
6
S3-7
9
S3-8
12
-
-
RESULTS AND DISCUSSION
-
Normal consistency of steel slag cement binder mixes
The normal consistency water requirement of steel slag cement binder mixes with varying proportions of steel slag was presented in Table 5.
TABLE 5. NORMAL CONSISTENCY OF CEMENT PASTE WITH STEEL SLAG POWDER
Sample
% steel slag fines
Water requirement of normal consistency (%)
Cement Mortar
0
30
S1-1
10
29
S1-2
20
29
S1-3
30
28
The normal consistency water requirement decreased with increase in steel slag content when compared to normal cement mortar. The normal consistency water requirement decreased from 30 to 28% when the percentage of steel slag fines increased from 0 to 30% .From the above results we can conclude that the water requirement of binder mixes decreases with increase in percentage replacement of steel slag fines. This may be because fineness of cement is more when compared to steel slag fines.
-
Initial setting time of steel slag cement binder mixes
Initial setting time of different steel slag cement binder mixes were determined as per IS 456:2000 and the results obtained are as shown in Table 6.
Sample
% steel slag fines
Initial setting time in minutes
Cement Mortar
0
75
S1-1
10
85
S1-2
20
100
S1-3
30
120
Sample
% steel slag fines
Initial setting time in minutes
Cement Mortar
0
75
S1-1
10
85
S1-2
20
100
S1-3
30
120
TABLE 6. INITIAL SETTING TIME OF CEMENT PASTE WITH STEEL SLAG FINES
Initial setting time of cement paste with steel slag fines were retarded when compared to ordinary Portland cement paste. As the percentage addition of steel slag increases the initial setting time gets retarded. The initial setting time of steel slag cement mix with 30% steel slag is 120 Minutes when compared to 75 Minutes of ordinary cement paste. i.e., there is a percentage retardation of 60%. This indicates that addition of steel slag can prolong the initial setting time. This may be because the early-ages activity of steel slag fines is not as fast as that of OPC and thus resulted in slow reaction progress and retarded setting times.
-
Compressive strength of SCM
Compressive strength(MPa)
Compressive strength(MPa)
The compressive strength of steel slag cement mortar specimens with varying proportion of steel slag were tabulated in Fig.1.
60
50
40
30
20
10
0
3
7
Curing time (Days)
28
60
50
40
30
20
10
0
3
7
Curing time (Days)
28
CM S-10% S-20% S-30%
CM S-10% S-20% S-30%
Fig. 1. Compressive strength of SCM with different steel slag cement ratios
For all the cement mortar samples, the compressive strength increased as the curing time increased. Fig.1 showed that
when the content of steel slag increases, the compressive strength of mortar specimens increases up to 20% and after that it starts decreasing continuously. The 3 day compressive strength of SCM is very less when compared to ordinary cement mortar. The 3 day compressive strength of SCM with 20% steel slag content is only 25.33 MPa while that of normal cement mortar is 32.33 MPa.ie, there is a difference of 21.65%. This difference goes on decreasing with the increasing curing period and at 28 days the compressive strength of SCM with 20% steel slag content is 51.8 MPa while that of Ordinary Cement Mortar is 53.4 MPa. Here the percentage variation is only 2.99%. Maximum compressive strength was obtained for SCM with 20% steel slag fines. At early-ages, the cementiious part of steel slag powder is far more inactive than the Portland cement and as the hydration age increases, the gap between the strengths of ordinary/normal cement mortar and mortars with steel slag becomes smaller and smaller.
Based on the results obtained, it can be observed that compressive strength of mortar cubes made by partial replacement of cement with steel slag show encouraging results at later ages. The lower early age strength can be attributed to the slower reactivity of slag due to presence of unhydrated large particles as per the available literature. This is due to due fact that the reaction of CaO present in steel slag fines is very fast and highly exothermic. The hydration products generated due to rapid reaction of CaO had weaker and fluffy types morphological crystals structure with more cracks and defects, which weakened the early strength. With the progress of time, hydration products became matured and their filling effect was also increased resulting in the more compact structure.
In order to get a more accurate optimum SCM specimens were prepared with 16%, 18% and 22% steel slag content and the corresponding compressive strength were shown in Fig.2.
Fig. 2. Compressive strength of SCM with different steel slag cement ratios
From Fig.2, it is found that the 3- day, 7- day and 28- day compressive strength of mortar specimens increased continuously, reached a peak at 18 % steel slag fines and thereafter showed a retarding trend. The 28 day compressive strength of SCM with 18% steel slag fines is found to be 54.67 MPa which is greater than that of ordinary cement mortar (OCM). So 18% steel slag content was adopted as the optimal experimental proportion for subsequent experiments. The initial setting time of cement paste with varying steel slag content is graphically represented in Fig.3.
140
120
100
80
60
40
20
0
140
120
100
80
60
40
20
0
Initial Seeting Time
(Minutes)
Initial Seeting Time
(Minutes)
Fig.3. Initial setting time of cement with different steel slag content
From Fig.3, It is clear that the initial setting time of steel slag cement binder mixes goes on increasing with the increase in percentage of steel slag fines. The initial setting time of cement paste with optimum experimental proportion of 18 % steel slag content is 98 minutes which is very much higher (30.67%) than that of OPC. So chemical activators were added in the following experiments, which would reduce the initial setting time and also increase the early strength of SCM.
-
Effect of chemical activators
In order to overcome the disadvantages of slow setting and low early strength of SCM four different alkali activators were added. Due to different types of chemical activators the chemical reaction and hardening process of hydration would be very complex, and the composition and structure of hydration products are quite different. The test results are presented below.
-
On Initial setting time of steel slag cement binder matrix
Initial Setting
Time(Minutes)
Initial Setting
Time(Minutes)
The initial setting time of cement paste with 18% steel slag fines after the addition of 6% of four different alkali activators is shown in Fig.4.
150
100
50
0
150
100
50
0
OPC
NaOH
Na2SO4 Na2SiO3
Na2CO3
OPC
NaOH
Na2SO4 Na2SiO3
Na2CO3
Fig.4. Effect of activators on the setting time of steel slag cement paste.
The initial setting time of cement paste with 18% steel slag fines and 6% Na2SO4 was obtained as 55 minutes and that with 6% Na2SiO3 was obtained as 65 minutes. i.e., addition of
Na2SO4 and Na2SiO3 can retard the initial setting time from 98 minutes to 55 and 65 minutes respectively. As we know that prolonged setting time is one of the major drawback of steel slag incorporated binder matrix, addition of Na2SO4 and Na2SiO3 will help to overcome this drawback. While NaOH and Na2CO3 doesnt have much effect on the initial setting time.
-
On Compressive strength of SCM
Compressive strength(MPa)
Compressive strength(MPa)
The compressive strength of mortar samples activated under 6% of different alkali activators is tabulated as shown in Fig.5.
60
50
40
30
20
10
0
3 DAY 7 DAY 28 DAY
CM SCM Na2SO4 Na2SiO3 NaOH Na2CO3
60
50
40
30
20
10
0
3 DAY 7 DAY 28 DAY
CM SCM Na2SO4 Na2SiO3 NaOH Na2CO3
Fig.5 Compressive strength of SCM activated under different chemical activators
The compressive strength of SCM activated with 6% Na2SO4 as an external chemical activator reached 34.33 MPa after 3 days, which is the highest of the four samples. This value is even greater than the 3 day compressive strength of ordinary cement mortar, which is 32.33 MPa .This is because Na2SO4 was often used as the main components of concrete early- strength agent, which plays an important role in improving the structure and performance of cement concrete. In addition, the compressive strength of samples with Na2SiO3 as an additional chemical activator after curing for 3 days reached a value of 30.33MPa (Fig. 4.5). NaOH and Na2CO3 are less effective on improving the early age compressive strength of concrete. The later age strength of concrete activated with these two activators is also lower.
When Na2SO4 was used as the activator, the compressive strength of the SCM reached the highest and confirmed to the strength requirements of the SCM. At the same time, Na2SO4 is low in cost and high in operability, with good actual activation effects. It is a neutral salt that has low corrosion. For comprehensive consideration, Na2SO4 was selected as the chemical activator.
-
-
Effect of % addition of alkali activator
-
Effect on compressive strength
Na2SO4 were added in the SCM in the proportions described in Table 4 and the compressive strength at the ends of 3, 7 and 28 days curing period were found out. The results are shown in Fig.6.
60
50
40
30
20
10
0
% of alkali activator
3 DAY 7 DAY 28 DAY
60
50
40
30
20
10
0
% of alkali activator
3 DAY 7 DAY 28 DAY
Fig. 6. Effect of % addition of Na2SO4 on compressive strength
From Fig.6, We can see that as the percentage addition of Na2SO4 increases from 1 to 12 %, the early age strength, i.e., 3 day and 7 day strength goes on increasing. The 3 day strength of SCM without the addition of alkali activator was 26.33 MPa. While increasing the percentage addition of Na2SO4 from 1 to 12 %, the 3 day strength of SCM reached a value from 31.33MPa to 39.33 MPa respectively. i.e. When the percentage addition was 12 %, there in an increment in 3 day strength by 49.37 %. Similar is the case with 7 day strength. The 7 day strength of SCM reached a value of 46.2 MPa when
% addition of Na2SO4 was 12%, while that of plain SCM was
36.12 MPa. Thus the percentage increase in 7 day strength was 27.9%.At later ages of curing (after 7 days), the addition of chemical agents did not showed a beneficial effect on the compressive strengths of the SCM.ie., the 28 day strength of chemically activated SCM reached a maximum value of 55.33 when the percentage addition was 6 %, and thereafter further increase in alkali activator content resulted in a reduction in 28 day compressive strength.
From Fig.6 it is clear that addition of 6 % Na2SO4 resulted in the highest compressive strength at all curing periods. But from economic point of view 4 % addition is satisfactory, when compared to normal cement mortar.
-
Effect on Initial Setting Time
Na2SO4 were added in different percentages in the steel slag cement binder matrix with 18% steel slag fins and 82 % cement and the initial setting time were evaluated. The test results obtained are shown in tabular form and graphically presented in Fig.7.
Fig.7. Effect of % addition of Na2SO4 on Initial setting time
120
100
80
60
40
20
0
% NA2SO4
120
100
80
60
40
20
0
% NA2SO4
Compressive strength(MPa)
Compressive strength(MPa)
CM SCM 1%
2%
3%
4%
5%
6%
9%
12%
CM SCM 1%
2%
3%
4%
5%
6%
9%
12%
INITIAL SETTING TIME
IN MINUTES
INITIAL SETTING TIME
IN MINUTES
CM SCM 1%
2%
3%
4%
5%
6%
9%
12%
CM SCM 1%
2%
3%
4%
5%
6%
9%
12%
-
-
CONCLUSION
-
SCM specimens were prepared by partially replacing cement with steel slag fines and various were studied such as consistency, Initial setting time and compressive strength. The following conclusions were drawn.
Addition of steel slag fines resulted in reduction in the normal consistency water requirement, this may be because the fineness of cement maybe more when compared to steel slag fines.
-
Addition of steel slag fines also resulted in prolonged setting time and comparatively low early age strength.
-
The 28 day strength of steel slag cement mortar is comparable to that of Ordinary Portland Cement mortar.
-
Optimum replacement level of steel slag fines is found to be 18% by weight of cement.
-
Among the four different alkali activators Na2SO4 showed the best activation effect.
-
The maximum strength was obtained when the percentage addition of Na2SO4 was 6%, however considering market cost and sustainability 4% was selected as the optimum amount of addition for concrete preparation.
-
SCM with 4% Na2SO4 showed comparable results to that of ordinary Portland cement mortar.
REFERENCES
-
Hou, J., Liu, Q., Liu, J., and Wu, Q.(2018). Material Properties of Steel Slag-Cement Binding Materials Prepared by Precarbonated Steel Slag.
Journal of Materials in Civil Engineering , ASCE, ISSN 0899-1561
-
Jiang, Y., Ahmad, M.R.,Chen, C. (2019). Properties of magnesium phosphate cement containing steel slag powder Construction and Building Materials ,ELSEVIER ,Vol.195.pp.140147 .
-
Palod, R., Deo, S. V., and Ramtekkar, G. D. (2018). Parametric Study of Steel Slag Powder as Cementitious Material on Cement Mortars Urbanization Challenges in Emerging Economies,ASCE.
-
Qiang, W., Mengxiao, S.,and Jun, Y.(2016). Influence of classified steel slag with particle sizes smaller than 20 m on the properties of cement and concrete Construction and Building Materials , ELSEVIER, Vol.123,pp.601- 610.
-
Yi Jiang , Y., Ling , T.C ., Shi , C., and Pan , S.U.(2018). Characteristics of steel slags and their use in cement and concrete – A review. Journal of Resources, Conservation & Recycling , ELSEVIER
,Vol. 136 , pp.187197.
-
Rosales, J., Cabrera, M., and Agrela, F.(2017). Effect of stainless steel slag waste as a replacement for cement in mortars- Mechanical and statistical study Construction and Building Materials , ELSEVIER, Vol.142,pp.444458.
-
Caijun, S.,(2004). Steel SlagIts Production, Processing, Characteristics, and Cementitious Properties Journal of Materials in Civil Engineering, ASCE ,Vol. 16, ISSN 0899-1561.
-
Rajeh, Z., Al-Zaid., Faisal, H., Al-Sugair and Abdulaziz, I.(1997) Investigation of potential uses of electric-arc furnace dust (EAFD) in concrete Cement and Concrete Research, Vol. 27. pp. 267-278.
-
Rashad, M A.(2020) Effect of steel fibers on geopolymer properties The best synopsis for civil engineer Construction and Building Materials , ELSEVIER, Vol. 246.
-
Rooholamini, H., Sedghi, R.,Ghobadipour, B., and Adresi, M.(2019) Effect of electric arc furnace steel slag on the mechanical and fracture properties of roller-compacted concrete Construction and Building Materials, Vol. 211.pp. 8898.
-
Roslana, N H., Ismailc, M., Khalid, N H., and Muhammaded, B. (2020) Properties of concrete containing electric arc furnace steel slag and steel sludge Journal of building engineering, Vol.28.
-
Stone, D ., Das, S ., Convey, D., and Neithalath, N.(2014) Pore- and micro-structural characterization of a novel structural binder based on iron carbonation Materials Characterization , Vol.98.pp. 168179.
-
Tran, T T., Pham, T M., and Hao, H.(2019) Experimental and analytical investigation on flexural behaviour of ambient cured geopolymer concrete beams reinforced with steel fibers Engineering Structures , Vol.200.
-
Usman, M., Farooq, S H., Umair, M., and Hanif, A.(2020) Axial compressive behavior of confined steel fiber reinforced high strength concrete Construction and Building Materials, Vol.230.
-
Zhang, N., Wu, L., Liu, X., and Zhang, Y.(2019) Structural characteristics and cementitious behavior of basic oxygen furnace slag mud and electric arc furnace slag Construction and Building Materials,.Vol.219.pp.1118.
-
Ahmad, M.R., Jiang, Y., and Chen, C. (2019). Properties of magnesium phosphate cement containing steel slag powder Construction and Building Materials,Vol.195.pp.140147.
-
Barnett, S.J., Rubio, M.D., Perez, B., and Parron, M.E. (2019). Mechanical-strength characteristics of concrete made with stainless steel industry wastes as binders Construction and Building Materials , Vol.204.pp. 675683.
-
Ghouleh, Z., Celikin, M., Roderick, I. L., and Shao, Y.(2018) Microstructure of Carbonation-Activated Steel Slag Binder Journal of Materials in Civil Engineering, ASCE, ISSN 0899-1561.
-
Gomesa, R F., Diasb, D P., and Silvac, F A. (2020) Determination of the fracture parameters of steel fiber reinforced geopolymer concrete Theoretical and Applied Fracture Mechanics.