
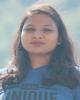
- Open Access
- Authors : Priyanka Mahadeo Teli , Dr. Suhas. P. Deshmukh
- Paper ID : IJERTV10IS120158
- Volume & Issue : Volume 10, Issue 12 (December 2021)
- Published (First Online): 04-01-2022
- ISSN (Online) : 2278-0181
- Publisher Name : IJERT
- License:
This work is licensed under a Creative Commons Attribution 4.0 International License
A Study on Suspension Testing Development
Ms. Priyanka Mahadeo Teli
PG Scholar,
Department of Mechanical Engineering, Government College of Engineering, Karad, Maharashtra, India
Dr. Suhas. P. Deshmukh
Associate Professor, Department of Mechanical Engineering,
Government College of Engineering, Karad, Maharashtra, India
Abstract A suspension or shock is actually a mechanical tool made to scale back or wet surprise impulse, & deplete kinetic strength. The shock's duty could be to soak up or deplete electricity. Inside the car, it cuts down on the end result of journeying over rough floor, resulting in progressed nice ride, at the same time as increasing in comfort because of extensively decreased amplitude of disturbances. Passive absorbers are drawing for normal load conditions. This provides the best vibration performance of the standard load condition. However, if the increased weight is less than normal, it affects the strength & ability to hold the road. In order to achieve consistent lubrication performance from shock, it is important to change the durability & deterioration of its properties. In this article, a suspension test is introduced, consisting of two helical springs & a fluid damper. The density of the flux damper is adjusted to four different levels to achieve the flexible durability of the model type. The load from the vehicle will push the damper lower below its normal loaded height. Within this project a surprise absorber was created in conjunction with a 3D model produced using Catia v5.
KeywordsSuspension design, experimentation, frequency etc
-
INTRODUCTION
Passive fluid shock provides an easy & effective solution for comfort & handling of the vehicle. These convert vibration energy into heat by passing viscous fluid through restricted orifice & are widely utilized in car suspensions. Furthermore, the fluid dampers are often tuned by changing the fluid flow area to vary the vibration isolation performance. A shock damps the movement of both the sprung & unspring masses of the car. The springs mass are that of the body & chassis of the car, & everything holding up by the springs. The unspring mass consists of the entire module not supported by the springs. This includes the suspension system & every one module attached to it; the brake caliper, brake disc, wheel, tire & some of the suspension arms.
Although there's a little amount of damping within the tire (approximately 2%) the suspension damper must do the bulk of the damping for this whole system. Meaning damping the sprung mass, unspring mass & therefore the tire! While springs & sway bars produce force supported their displacement or deflection, dampers produce force supported how briskly you progress them, or their velocity. Therefore, the quantity of damping produced is proportional to velocity. This suggests the damper works sort of a dynamic spring; it produces force only it's moving. The first purpose of the damper on the car is to damp the sprung & unspring masses at their resonant frequencies. For the sprung mass, this includes the pitch, heave & roll resonant frequencies. A secondary function is to regulate the speed of weight transfer throughout
transients like braking, corner entry & acceleration. Within the best case, dampers. If everything else within the suspension drawing & component selection is correct, they simply damp the vibrations at resonant frequencies, control the speed of weight transfer & enhance vehicle comfort & performance. Within the worst case it dampens, they're asked to catch up on structural deficiencies, control heave, pitch or roll imbalances, & catch up on drawing deficiencies like lack of suspension journey.
-
BASIC CONSIDERATION FOR SUSPENSION
SYSTEM
-
Suspension Basics
The suspension of vehicles must satisfy variety of requirements which depend upon different operating conditions of the vehicle. These processes gives a dual purpose contributing to the vehicle's handling & braking permanently active safety & driving pleasure, & keeping vehicle occupants comfortable & fairly well isolated from road noise, bumps, & vibrations. The suspension also protects the vehicle itself & mounted systems from damage & wear. We will look into suspension calculation theory to have better look into drawing a better suspension system.
-
Basic Consideration
-
Vertical loading
In vertical loading road wheel comes across the bump on the road it's subjected to normal forces (tensile or compressive) depending on the load irregularity which are engrossed by the elastic compression, shear, bending, twisting properties of spring. To minimize the pitching effect of the car, the front system should have less spring action than the back suspension.
-
Rolling
Center of gravity of the vehicle is significantly above the bottom. As a result while taking becomes the force acts upwards on the C.G. of auto, while the load resistance acts inwards at the wheels. This produce to a few turning the vehicle about the longitudinal axis called rolling.
-
Road holding
In road holding the degree to which vehicle maintains the contact with the road surface in various types of directional changes also as in line motion is named as road holding.
-
Unsprung weight
Unsprung weight is that the weight of the vehicle module between suspension & road surface (Rear axle assembly, steering knuckle, front axle, wheels).
-
Spring & Dampers
Most suspensions use springs to absorb impacts & dampers (or shock absorbers) to control spring motions. Semi-active suspensions include devices such as air springs & switchable shock absorbers, various self-leveling solutions, as well as systems like Hydro pneumatic, Hydromantic, & Hydra gas suspensions. Conventional springs & dampers are referred to as passive suspensions. If the suspension is externally controlled then it is a semi-active or active suspension. Mitsubishi developed the worlds first production semi-active electronically controlled suspension in passenger cars; the system was first incorporated within the 1987 Gallant model. a vehicle does not pitch when it goes over bumps within the ground, but instead moves up & down in parallel translation, it has a better springing balance.
-
Spring rate
The spring rate or stiffness is a component in setting the vehicle's ride height or its location in the suspension stroke. Vehicles which carry heavy loads will often have stiff springs to catch up on the extra weight that might otherwise collapse a vehicle to the bottom of its journey (stroke). Stiff springs are also used in performance applications when the suspension is constantly forced to the bottom of its stroke causing a discount within the useful amount of suspension journey which may also lead to harsh results. Riding in an empty truck used for carrying loads are often uncomfortable for passengers because of its high spring rate relative to the load of the vehicle. A system would even be described as having stiff springs & would also be uncomfortably bumpy. A luxury car, taxi, or passenger bus would be described as having soft & medium dampers. Vehicles with worn out or damaged springs ride lower to the bottom which reduces the general amount of compression feasible to the suspension & increases the quantity of body lean. Sports vehicles can sometimes have spring rate requirements othe than vehicle weight & load.
-
Mathematics of the spring rate
Spring rate is a ratio used to measure how resistant a spring is to being compressed or expanded throughout the spring's deflection. The magnitude of the spring force increases as deflection increases according to Hooke's Law. Briefly, this can be stated as,
F= -KX (1)
Where,
F is the force the spring exerts k is the spring rate of the spring.
X is the displacement from equilibrium length i.e.
The length at which the spring is neither compressed nor stretched. Spring rate is confined to a narrow interval by the weight of the vehicle, the load the vehicle will carry, & to a lesser extent by suspension geometry & performance desires. Spring rates typically have units of N/mm. A non-linear spring rate is one for which the relation between the spring's compression & the force exerted cannot be fitted adequately to a linear model. The spring rate of a coil spring may be calculated by a simple algebraic equation or it may be
measured in a spring testing machine. The spring constant k can be calculated as follows:
K= (d^4 G)/(8ND^3 ) (2)
Where, d is the wire diameter, G is the spring's shear modulus (e.g., about 80 GPa for steel), & N is the number of wraps & D is the diameter of the coil.
-
Damping
Damping is the control of motion or oscillation, as seen with the use of hydraulic gates & valves in a vehicle's shock absorber. This may also vary, intentionally or unintentionally. Like spring rate, the optimal damping for comfort may be less than for control. Damping controls the journey speed & resistance of the vehicles suspension. An undamped car will oscillate up & down. With proper damping levels, the car will settle back to a normal state in a minimal amount of time. Most damping in modern vehicles can be controlled by increasing or decreasing the resistance to fluid flow in the shock absorber.
-
Damping ratio
The damping ratio helps us establish which case of the damped motion we are considering. The table presented below will assist you interpret the results obtained from the damping ratio test. Note, that the damping factor can't be negative.
Table I Damping Table
There are three useful formulae used in our damping ratio calculator. We will present each of them with an explanation below.
(3)
Where,
C – Damping coefficient (in Ns/m); &
Cc – Critical damping coefficient (in Ns/m).
This is the most basic formula. If the damping coefficient is any less than the critical damping coefficient the result will be less than 1 & imply that the system is under damped, as expected.
(4)
Where,
m – Suspended mass (in kg); &
k – Spring constant, as seen in Hooke's law (in N/m).
This damping ratio formula is similar to the first one, but we used the fact that
Cc = 2(mk). (5)
Where,
0 – Natural angular frequency. This is the magnitude of the angular velocity of the system when it undergoes the simple harmonic motion (in rad/s).
In this case, we rearranged the formulae further, using 0 =
(k/m).
Notice that if the values of the other quantities are established, you also know how to find the damping coefficient. This method is much simpler & more approachable than the ones we mentioned in the first section.
As you may have noticed in the first formula, the critical damping coefficient & the damping coefficient units are the same. It means that the damping ratio is dimensionless.
Two-degree-of-freedom quarter car model for analysis of a passive suspension is shown in Figure. Sprung mass (m1) represents chassis & vehicle body, whereas un-sprung mass (m2) includes suspension & tire. Quarter car models have been used for numerical simulations to evaluate vibration isolation performance of the presented system.
Figure 1 Quarter car model.
Sprung mass acceleration is the criteria used to quantify vehicle comfort performance.1 Lower sprung mass acceleration gives better comfort & vice versa. Steady-state response of the sprung mass acceleration for harmonic displacement of the un-sprung mass is given as follows
(6)
Damping factor () is given as follows
(7)
Where C is the damping coefficient, m1 is the sprung mass, wn is the natural angular velocity, w is the angular velocity of un-sprung mass excitation, ks is the suspension sprung stiffness, r is the frequency ratio (w/wn) & ypk is the peak displacement of the un-sprung mass.
Equation (1) is rewritten to obtain to include the mass & the sprung mass acceleration (steady-state response under harmonic excitations of amplitude ypk) & can also be written as follows.
(8)
Where f is the un-sprung mass excitation frequency. Equation
(3) implies that the acceleration will depend on the sprung mass in addition to the excitation frequency. Simulation has been performed with the quarter car model to evaluate the effect of change in the sprung mass on comfort. Input parameters used in the simulations are given in Table II.
Table II Simulation input Parameters.
Acceleration response for different values of sprung mass is plotted in Figure. It can be observed from Figure that the passive suspension gives better comfort for maximum sprung mass. However, as the sprung mass reduces, higher acceleration deteriorates vehicle comfort.
Figure 2 Sprung mass acceleration for different values of sprung mass.
-
-
EXPERIMENTATION
Vehicle suspension testing machines are generally configured as two or four rollers in a rigid frame. The wheels of the vehicle under test are placed between the rollers .For normal operation to test the suspension on a vehicle, the vehicles wheels are spun under the power of the tester.
The speed of the test vehicle is applied. A dynamometer then measures whether the retardation force present from the speeding effect of the test vehicles wheels is adequate.
Drawing of testing jig is performed on catia v5 & manufactured with workshop tools. To make it easy & affordable to manufacture mounting & cam was made in 3d printers. Complete view of the cad model is shown in the following picture.
-
Specifications
-
Driving Motor Torque: 896 N/cm
-
Motor Voltage: 12V
-
Motor Rating: 80 Watt
-
Motor Type: Planetary Gearbox Motor
-
Max RPM: 18
-
Damper Length: 200 mm
-
Damper Stroke: 50 mm
-
Damper type: Coil over + Air shock
-
Rail Material – Aluminum
-
Cam material: Nylon 66
Figure 3 Experimental setup
-
-
Testing conditions
The following section outlines a portion of the test programed. The test cases detailed in this report are shown in Table.
Table III Testing Conditions.
Condition
Full Load
1. No shock absorbers
yes
2. New shock absorbers
yes
For the three condition states of
-
No shock absorber.
-
A fully-functional shock absorber (i.e. within specification) for the suspension being measured.
At a load approximating full load (500N) on the damper, the test vehicle damper was spun up using the cam roller of the test rig. For the data presented in this report, the hydraulic valves of the test rig were set so that the final speed of the roller reached 50 revolutions per minute. This meant that, with two flats per revolution, the frequency of the forcing function from the flats of the roller was 12 Hz. This was at or above the highest axle-hop frequency measured for this trailer & suspension. Other speeds were used & data recorded for these. The results of that analysis will be reprted in future papers & at other for.
Figure 4 Time series of the wheel forces for new shock absorbers.
Figure 5 Time series of the wheel forces for no shock absorbers.
Dynamic range of signal
The peak-to-peak value (i.e. the dynamic range) of the wheel- force signal was derived for the three cases of shock absorber health.
Figure 6 Example of dynamic range (peak-to-peak value) of the wheel
forces.
The values of dynamic range1 for wheel forces with the three conditions of shock absorbent health is shown in Table. These values were derived from the dynamic data shown in graphical form.
Condition at 500N
Peak-to-peak value of
Difference compared
static wheel loading
wheel force (kg) for
with new shock
flats with 4 mm
absorber case
excitation
No shock absorbers
280
47.1
New shock absorbers
132
0
Condition at 500N
Peak-to-peak value of
Difference compared
static wheel loading
wheel force (kg) for
with new shock
flats with 4 mm
absorber case
excitation
No shock absorbers
280
47.1
New shock absorbers
132
0
Table IV Results
-
-
RESULTS
The signals from the load cells under the roller bearings were conditioned & filtered with a 25 Hz low-pass filter to remove noise. Time-series & peak-to peak values are shown in the following section
Time series of wheel force signals
Portions (& representative samples) of the time series of the wheel-force signals for the three states of shock absorber health are shown in Figure. Resonance occurred throughout the transients from starting the roller compared with the steady-state running dynamic forces. This may be seen in the starting transients for the worn & no shock absorber cases in the 0.5-1.0 s or so before the signal settled down to fairly even excursions.
ACKNOWLEDGMENT
First & foremost, I would like to thank my guide Dr. S. P. Deshmukh, Mechanical Engineering Department, for guiding me to accomplish this dissertation work. It was my privilege & pleasure to work under his able guidance. I am indeed grateful to him for providing helpful suggestion, from time to time. Due to his constant encouragement & inspiration I am able to present this dissertation.
I am very much thankful to Dr. A. T. Pise, Principal, Government college of Engineering, Karad for providing all the necessary facilities to carry out my dissertation work
I express my deep gratitude to Dr. R. K. Shrivastava, Head of Mechanical Engineering department for his valuable guidance & constant encouragement.
I am thankful to all teaching & non-teaching faculty members of Mechanical engineering department, GCE Karad, for providing help me directly or indirectly for completing this dissertation work.
Last but not the least; it would not have been possible for me to resume the prolonged work of project without support of my family members. Constant encouragement & support of my family made me possible to complete the work.
REFERENCES
-
Lalitkumar Maikulal Jugulkar , Shankar Singh , Suresh Maruti Sawant ,Analysis of suspension with variable stiffness & variable damping force for automotive applications Advances in Mechanical Engineering 2016, Vol. 8(5) 119.
-
Mahmoud Omar , M.M. El-kassaby, Walid Abdelghaffar A universal suspension test rig for electrohydraulic active & passive automotive suspension system Alex&ria Engineering Journal (2017) 56, 359370.
-
Hitesh K. Tare, C.S. Dharankar Determination of damping coefficient of automotive hydraulic damper using sinusoidal testing VOLUME-3, ISSUE-7, 2016.
-
P. KARIMI ESK&ARY, A. KHAJEPOUR, A. WONG & M. ANSARI Analysis & optimization of air suspension system with independent height & stiffness tuning International Journal of Automotive Technology, Vol. 17, No. 5, pp. 807816 (2016).
-
ukasz Konieczny, Rafa Burdzik Modern suspension systems for automotive vehicles & their test methods Article in Vibroengineering PROCEDIA October 2017.
-
Ankit Kumar Dixit*, Aradhya Saxena, Arpit Gupta, Ch&ransh P&ey, Prashant Chauhan Concept of Shock Absorber Test Rig & Approaching towards a Universal Testing Procedure Volume no.06,special issue no.[02],December 2017.
-
Alan G. Mayton Joseph P. DuCarme Christopher C. Jobes Timothy J. Matty Laboratory investigation of seat suspension performance throughout vibration testing National Institute for Occupational Safety & Health, Pittsburgh Research Laboratory.
-
A.E. Geweda a, M.A. El-Gohary b, A.M. El-Nabawy a, T. Awad Improvement of vehicle ride comfort using genetic algorithm optimization & PI controller Alex&ria Engineering Journal (2017) 56, 405-414.