
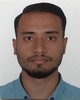
- Open Access
- Authors : Smart Shrestha , Babu Ram Bhandari , Sagar Chhetri
- Paper ID : IJERTV11IS090065
- Volume & Issue : Volume 11, Issue 09 (September 2022)
- Published (First Online): 20-09-2022
- ISSN (Online) : 2278-0181
- Publisher Name : IJERT
- License:
This work is licensed under a Creative Commons Attribution 4.0 International License
A Study on Physical Properties of Pervious Concrete
Smart Shresthaa, Babu Ram Bhandarib, Sagar Chhetric
a,b,c Infrastructure Engineering and Management Program, Department of Civil and Geomatics Engineering, Pashchimanchal Campus,
Institute of Engineering, Tribhuvan University, Nepal
Abstract:- Unlike conventional concrete, Pervious Concrete (PC) possess an open graded structure due to the fact that it contains no or very less amount of fine aggregates. This open structure of PC helps in water infiltration. Increasing concretization in urban areas has resulted in formation of impermeable surface everywhere. All the storm water is forced into the drain whose size is insufficient to accommodate them. This has resulted in urban flooding. Also due to absence of infiltration, ground water level is diminishing.
This study is intended to study the properties of PC and its application in reducing these problems. With the application of PC in light loading areas such as sidewalks, parking, playgrounds and parks, a significant amount of water can be infiltrated, which will help in reducing storm water run-off, thus preventing urban flooding and increase ground water recharge. With infiltration, underlying subsoil moisture can be maintained which in return can reduce the heat island effect in urban areas. The test results obtained from this study were in accordance with the properties as stated by ACI 522R (2010) and therefore PC can be prepared with cement ad coarse aggregates available locally in Pokhara to use in light loading areas like parking lots, sidewalks, bicycle lanes, and playgrounds.
Keywords: Pervious Concrete, no fines concrete, zero slump, permeability
1. INTRODUCTION
Concrete can be defined as a hardened stone like material composed of homogeneous mixture of cement, fine aggregate, and coarse aggregate in presence of water, which are extensively used as building material in modern days. Pervious Concrete (PC) is a special type of concrete tailored using very less or no fine aggregates. ACI 522R (2010) defines PC as a near zero slump, open-graded material consisting of Portland Cement, Course Aggregate, little or no Fine Aggregate, admixtures and water. Unlike conventional concrete, pores are introduced in PC by removal of fine aggregates from concrete creating voids between the coarse aggregates, which would be otherwise occupied by fine aggregates. This results in pores formation with its size ranging from 2 to 8 mm, allowing water to pass through easily, with void content ranging from 15 to 35% and compressive strength ranging from 2.8 to 28 MPa. The permeability ranges from 0.14 to 1.22 cm/s depending upon the aggregate shape, size, grading and density of the mixture. This hydraulic property of PC has its advantage over conventional concrete for using it as a pavement material. Compared to conventional concrete pavements, Pervious Concrete Pavements (PCP) has its advantages mainly from hydroplaning perspective. It helps in controlling storm water pollution at source as well as runoff. It helps I reducing hydroplaning o road and highway surfaces. The interaction noise between tire and pavement as well as glare on road surface especially when wet during night time is reduced significantly. It helps in increasing parking facilities by eliminating the need for water retention areas whereas it reduces the size of storm sewers. PCP helps in allowing air and water to reach tree roots, even with pavement within the tree drip line. However, there are some challenges and disadvantages of PCP with its use limited to light loading areas. Pervious Concrete is sensitive to water content and has extended curing time. Therefore, it requires specialized construction practice requiring special attention when applying PC inn areas with high groundwater as well as with application in soil types susceptible to frost and expansion. The lack of standardized test is another challenge in its application. Its application in pavement has been specified as surface course, permeable base, edge drains and shoulders. The application of PC and its thickness depends primarily upon two factors. First being its hydraulic property (porosity and permeability) and mechanical property (strength and stiffness).
The strength and properties of concrete is determined by the proportion of its ingredients. When water is added to the ingredients, it reacts with cement initiating the hydration reaction which helps to form a hard matrix responsible for binding the materials into a stone like tough material. Since, in PC, fine aggregates are used in no or less amount, voids are present in the concrete which could have been filled by fine aggregates. This results in the decrease of compressive strength of concrete. Low strength of concrete restricts its use as structural material. However, the strength of concrete can be increased using admixtures. Chen et al. (2011) have produced high strength PC with strength ranging from 32 to 46 MPa by addition of silica fumes, super plasticizers and polymer modifications. The concrete possesses better fatigue property compared to conventional PC suggesting improved resistance to cracking and crack propagation.
The voids present in the PC due to the absence of fine aggregates helps in decreasing the overall weight of the concrete whereas it increases the insulating properties of the concrete due to air present inside the voids. These interconnected voids also act as path for water to percolate into the underlying soil, thus reducing the surface runoff water. The various properties of PC are primarily dependent on its porosity, which in turn depends on cementitious content, water cement ratio,
compaction level and aggregation gradation quality. Quantity of cement is an important factor for development of compressive strength and void structure. Cementitious paste in excess results in filled void structure and hence reduced porosity. Whereas insufficient cement paste results in reduced paste coating and reduced compressive strength (ACI 522R, 2010).
PC is gaining popularity in recent days due to its ability to allow water to pass through it to the underlying soil. It is mostly popular and suitable in low-traffic urban areas where most of the land are covered with very little exposed soil surface which has resulted in an increase in surface runoff whereas reduction in groundwater recharge almost to zero. This has called off PC as a solution to this problem. Pervious pavements are considered as Best Management Practices (BMPs) by the Environment Protection Agency (EPA). PC has been adopted as a mitigating policy by communities to the problems related to storm water runoff. As the air temperature over PC parking lots is generally cooler than asphalts, they have also been selected as an integral solution to the problem of hot pavements in the cool communities program. They also reduce snow and ice buildup and are considered a non-pollutant to the environment. The practical range of design thickness for PCP is from 125 to 300mm for plain parking lots (ACI 522R, 2010). The application of PC ranges from reducing the amount of runoff water, recharge ground water table, to tree grates, sound walls, retaining walls, air and water purifier etc. Other advantages of Porous Concrete include improving skid resistance, preserving natural ecosystem, reducing noise hydroplaning and minimizing the heat island effect in large cities (Takhelmayum & S.N, 2012).
There has always been a trend of migration from rural areas to urban areas. Therefore, the urban population is ever increasing. With increase in population, the number of new houses is increasing.Thus, there is huge change in land use/land cover than it was few decades ago. Most of the soil which were exposed to atmosphere are now covered by impervious layer in the form of pavements, parking lots, houses, roads. This has created problems especially in monsoon season as major cities of Nepal like Kathmandu, Bhaktapur, Pokhara, Biratnagar suffer from urban flooding. The main reason is change in land use practice covering open land with impervious layer and due to this, in rainfall season, all the storm water runoff accumulates into the drain rendering its capacity insufficient resulting in flooding.
Shrestha (2019) stated that the total 50 kilometers long storm water drain were designed and constructed in Pokhara about two decades ago with design considerations that were based on the then available references and much has been changed since that time. With the change in land use practice and increase in impervious surface, the volume of accumulated storm- water runoff has increased. Thus the present data will give different drain cross section. Khadka & Basnet (2019) confirmed the above statement as they found out in their study that the existing drainage system of lakeside (Barahi Chowk) of Pokhara to be inadequate for the runoff generated during the peak rainfall.
Increasing the cross section of the drainage without decreasing impervious cover is a short-term solution and in the long run, those too will be insufficient. In such condition, another alternative can be the use of PC. Replacement of impervious conventional concrete cover and paving tiles in areas like pedestrian walkways, parking lots, playgrounds, cycle lanes and parks can help in decreasing the storm-water runoff by percolating the rainwater to the underlying soil. This helps in reducing the urban flooding problem and pollution of water resources as well as increase in recharge of ground water table that can help in preventing water scarcity during dry season.
-
Objective of the study
The main objective of this study is to study the physical properties of Pervious Concrete. Its specific objective is:
-
To study the hydraulic and mechanical properties of Pervious Concrete.
-
-
Scope of the study
With rapid urbanization, land use practice is changing. In city areas, most of the open land are covered by buildings and pavements which are mostly impermeable in nature, thus increasing the rate of storm water runoff and decreasing the rate of water infiltration in to the ground water table. The designed drain capacity is increasingly becoming insufficient to carry the storm water, thus urban areas are facing flooding problems (Tennis et al., 2004). Use of PC in construction can help in reducing problems relating to urban flooding and heat island effect. It will also help in improving the quality of ground water by filtering of organic and inorganic materials during infiltration. Although the use of PC dates back decades in US and Europe, it has not been used commercially in Nepal. This research intends to introduce the concept of PC and how it can help in reducing the flooding problem in urban areas and help in contributing ground water table recharge.
-
Limitation of the study
The limitations of this research are:
-
For the hydraulic property of the PC, only porosity and permeability were measured.
-
For the mechanical property, compressive strength and density were measured. Its flexural strength and its durability properties such as its resistance to freeze and thaw, sulfate resistance and abrasion resistance were not measured.
-
The shrinkage on the concrete was not taken into consideration and the volume of cylindrical mould was taken as the total volume of the sample specimen.
-
Research Review
-
LITERATURE REVIEW
Moretti et al. (2019) stated that the practice of waterproof material in pavement has led in increasing the flow of water into sewage system creating problems relating to flooding, reduced ground water table recharge and surface temperature increase due to heat island effect. As such, permeable pavement provides best alternative. However, they suffer from clogging and therefore require schedule cleaning. With the application of Permeable Concrete Pavement (PCP), storm water runoff can be managed. Removal of organic and inorganic materials during infiltration process improves the quality of ground water. PCP also improves skid-related falls, reduction of traffic noises as well as urban heat island effect. Nonetheless PCP are exposed to risk of clogging and freeze and thaw damage. (Xie et al., 2019) Zhu et al. (2019) in their study found out that for a two-way six lane road in Nanjing, China, PCP could reduce surface runoff by more than 50% as compared to reduction by more than 10% by drainage system. PCP has influence on reduction of flood peaks as well as hysteresis of flood peaks. The whole permeable pavement system, including permeable subgrade had better result in reducing runoff coefficient and flood peak flow with sand being the ideal material for subgrade. Merighi et al. (2006) in their study discussed about the use of PC as layer over continuous concrete base and found out that it is effective in reducing tyre spray and hydroplaning. Their study verified the potential of PC to serve as wearing course on Airport runways with proper consideration of aggregate grading and enough cement content to maintain porosity, bond to aggregate, compressive and flexural strength behavior as well as water permeation capacity or drainage property. Various attempts have been done to make PC more sustainable. By replacing aggregate by Oil Palm Kernel Shell (OPKS) (from 25 to 75% by mass), sustainable PC can be achieved with compressive strength ranging from 6 to 12 MPa and permeability varying from 4 to 16 mm/s which is acceptable for use in light traffic roads and parking lots. (Khankhaje et al., 2016)
-
-
Constituents of PC
In general, concrete consists of cement as binding material, with coarse aggregate as main constituent responsible for the strength and volume of the concrete and fine aggregate acting as a filler material of occupy the spaces between the aggregate to render it dense. Admixtures are also used in concrete production to increase is workability as well as other hydraulic and mechanical properties. Pervious Concrete differs from conventional concrete as the use of fine aggregate is limited creating a continuous interconnected void in concrete responsible for better hydraulic conductivity. Its constituents are:
Cement: Cement is a binding material. Cement when mixed with water forms a paste, which is coated on the surface of aggregate. This cement paste when hardened gives bond strength to the aggregates. It is an essential component of concrete. ACI 522R (2010) and IS: 12727 (1989) have mentioned that Ordinary Portland cement can be used to prepare PC.
Coarse Aggregates: Coarse aggregates are the major constituent of concrete. They are used in large proportion compared to other constituent materials and are responsible for the strength of the concrete. The properties of coarse aggregate govern most of the properties of concrete. Aggregate shape, size, source, surface condition, water absorption, specific gravity and presence of organic and deleterious materials are responsible for deciding the quality of concrete prepared. Test on aggregates should be carried out to find its properties for using it in concrete preparation. A narrow grading is an important characteristic. Larger aggregate provides a rougher surface. Recent use of PC has focused on parking lots, low traffic pavements and pedestrian walkways. For these applications, the smallest sized aggregate feasible is used for aesthetic reasons. Coarse aggregate size 9.5mm top size has been used extensively for parking lots and pedestrian applications (Tennis et al., 2004). Single sized or narrow graded aggregates are suitable for preparing PC. Both IS 456 (2000) and IS: 12727 (1989) suggests the use of 20mm aggregate in general and for thin sections, 10mm aggregate size can be used, but it requires more quantity of cement. ACI 522R (2010) suggests single sized course aggregate or grading between 19 mm and 9.5 mm. The presence of elongated and flaky aggregates also affects the properties of PC. Use of flaky and elongated aggregates results in formation of less voids as these type aggregates tend to stack on one another while mixing disrupting the interconnected voids.
Water: In concrete preparation, water is responsible for producing wet mixture of cement sand and aggregate and increase the workability of concrete as well as hydration of hardened concrete to gain strength. It should be free from any acidic or basic impurities. Generally, water that is suitable for drinking is suitable for preparation of concrete. The use of potable water is satisfactory for making concrete mixes (ACI 522R, 2010; IS 456, 2000).
-
Preparation of Pervious Concrete mix
Water Cement ratio (w/c): For preparation of concrete, water cement ratio governs the workability of mixture. Excess amount of water will make the paste lean, which results in drainage and clogging of pore system. Insufficient amount of water will make thick paste, resulting in insufficient coating of aggregate thus reducing the strength of the concrete. Unlike conventional concrete, the use of fine aggregate is limited in PC. Due to this, the water requirement for preparation of
mixture decreases as water is mixed with cement only to form paste as opposed to cement and sand in conventional concrete preparation. Chindaprasirt et al. (2008) stated that though the fundamental properties of PC have been studied, the optimum condition to produce good porous concrete with potentially highest strength and durability has not been established. To obtain continuous voids and enough strength, most important condition is to keep the continuity of cement paste with coarse aggregate embedded such that continuous void is maintained which is achievable with the use of cement paste with relatively low water content and sufficiently high workability. ACI 522R (2010) recommends w/c to be kept between 0.27 to 0.34 and IS: 12727 (1989) recommends w/c to be between 0.4 to 0.5.
Cement Aggregate ratio (C/A): Cement Aggregate ratio is responsible for the density of the concrete which in turn is responsible for the strength of concrete. In pervious concrete, the ratio of cement and aggregate affects the porosity of PC. Using of Cement smaller ratio results in less cement to mix with large amount of aggregate. In such conditions, enough strength may not be achieved as cement paste is insufficient to coat the aggregate and provide necessary bond strength. Whereas keeping the cement aggregate ratio larger results in decrease in aggregate quantity with more cement available to mix with it. In such condition, cement paste is able to fully coat the aggregate and give enough bond strength but the surplus cement paste may settle between the aggregate voids resulting in decrease in porosity as well as disrupting in formation of interconnected voids. This results in decreased permeability which makes it not suitable for application. Aggregate ratio of 1:4 to 1:4.5 by weight is suggested by ACI 522R (2010), whereas C/A of 1:8 to 1:12 by volume is suggested by IS: 12727 (1989).
-
Properties of PC
The physical properties of PC that governs its acceptability in application can be broadly divided into two groups. They are hydraulic property and mechanical property. Porosity and permeability fall under hydraulic property as these values are responsible for hydraulic conductivity of PC. Strength and durability are the mechanical property of PC. Pervious Concrete should have enough strength to sustain the applied load and should possess hydraulic conductivity to allow water to pass through it to the underlying soil. PC produced with similar process as conventional concrete possesses satisfactory properties. It was found out that the compressive strength was decreased by 50 to 70%, split tensile strength by 45 to 50% and density by 30% as compared to conventional concrete whereas percentage of void ratio was increased to 4%. (Rajasekhar & Spandana, 2016) Due to the absence of filler material sand, the voids in the concrete is increased which decreased the density of the concrete. This resulted in lower strength, whereas due to the presence of voids, the permeability of the PC was increased. Alam et al. (2013) in their study found out that for PC with very high porosity, the compressive strength demand is very high but that kind of situation is unlikely in current practice. Tensile strength demand is higher for edge loading and compressive stress demand is highest for corner loading. The total porosity of PC is responsible for the strength of the concrete but it cannot be measured easily. It can be estimated through effective porosity. There is a good correlation between effective and total porosity estimation method is suitable in condition where apparatus to measure total porosity is unavailable. Newly developed model using Griffiths Fracture Theory, which is a semi-empirical model can be applied to predict compressive strength of porous concrete on the basis of porosity of the material. (Lian et al., 2011)
The permeability of PC is an important and necessary property. PC are designed to have voids which results in better permeability value. Permeability test is necessary to determine its hydraulic conductivity of PC for its application. Qin et al. (2015) conducted permeability test on PC sample using constant head method (CHM) and falling head method (FHM) and found out the permeability to be increasing linearly with the reciprocal water pressure. Permeability measure by constant head method was found out to be lower than that by falling head method and the selection of starting and finishing water heads from falling head method affected the calculated permeability. They suggested that the water permeability of permeable concrete should be reported with the applied pressure and the associated testing method.
The strength of PC is governed by the cement and coarse aggregate ratio. Addition of fine aggregates can increase the strength but it results in decrease in other properties. Addition of admixtures and inert materials along with cement and aggregate for preparation PC can help achieve higher strength inn PC. Different studies have been carried out to produce PC with favorable properties. Some of the studies conducted to produce PC with different w/c and C/A without any addition of admixtures and inert materials and its properties are listed in the table below.
Table 0.1 Results from similar research studies
Literature
w/c
C/A
Porosity (%)
Permeability (cm/s)
Comp. Strength (Mpa)
ACI 522R (2010)
0.27 to 0.34
1:4 to
1:4.5
15 to 35
0.14 to 1.22
2.8 to 28
Tennis et al. (2004)
0.27 to 0.34
1:4 to
1:4.5
15 to 25
0.2 to 0.54
3.5 to 28
Kevern et al. (2011)
0.29
1:4
32.5
–
12.3
Huang et al. (2010)
0.35
1:4.5
27 to 30
1.7 to 1.9
5 to 7
Chindaprasirt et al. (2008)
0.28 to 0.34
1:2.14 to
1:3.36
15 to 25
–
13 to 22
Jain & Chouhan (2011)
0.3 to 0.45
1:4
–
0.13 to 2.52
2.79 to 12.18
Chandrashekar et al. 2018)
–
1:48
34.2
0.29
21.5
Rajasekhar & Spandana (2016)
0.35
1:4
–
–
22
Manan et al. (2018)
0.65
1:263
–
0.92
11.29
Ali & Kareem (2014)
0.27 to 0.36
1:3.7
12 to 22
0.2 to 1.1
12 to 17
Sharanya (2019)
0.3
1:4
–
0.44 to 0.90
11.3 to 25.4
Deepika & Fathima (2020)
0.36
1:4
–
1.5
16.1
Rami & Joshi (2015)
0.33
1:4
–
4.13
7.64
-
RESEARCH METHODOLOGY
-
Materials
For the preparation of PC in this study, material used were Ordinary Portland Cement (OPC), natural coarse aggregate and water. The materials were collected following the guidelines and previous researches as discussed in literature review.
Cement: – The cement used in this test was OPC 43 Grade Sagarmatha Cement.
Coarse Aggregate: – Washed natural river bed coarse aggregate without presence of any organic materials were collected from Hemja. Two different group of coarse aggregate were used. They are:
-
-
-
Aggregate passing through 16mm and retained in 9mm sieve.
-
Aggregate passing through 9mm and retained in 5mm sieve.
The physical properties of coarse aggregate were tested. Sieve analysis to determine coefficient of uniformity (Cu) and coefficient of curvature (Cc), flakiness index and elongation index measurement test were carried out following IS:2386- Part I, 1963 Specific gravity and water absorption test were conducted following the procedures from IS 2386- Part III, 1963.
Water: – Potable water available in Hemja was used in this study.
-
Preparation of PC
The ratio of cement and coarse aggregate affects the strength of the concrete. For this study, the ratio of cement and coarse aggregate was fixed following the nominal mix ratio used in general practice for preparation of M20 and M15 concrete. In general practice, cement sand and coarse aggregates are mixed in ratio of 1:1.5:3 for M20 nominal mix and in the ratio of 1:2:4 for M15 nominal mix. As the use of sand is limited in PC, and in this study, the use of sand was restricted, and in concrete, aggregate is responsible for the total volume of the concrete and sand acts as filler material, the proportion of sand from nominal mix ratio was removed reducing the ratio of cement and aggregate to 1:3 for M20 and 1:4 for M15. The target mean compressive strength was set as 15 MPa for 1:4 mix and 20 MPa for 1:3 mix. With two different aggregate sizes and to different mix ratio, six mixes were prepared in total. The mixes and their aggregate size and proportions are shown in table. For preparing sample A and B, aggregate of size 5-9mm were mixed in the ratio of 1:3 and 1:4 respectively. Similarly, for sample C and D, aggregate size 9-16mm were mixed in the ratio 1:3 and 1:4 respectively. For sample E and F, aggregate size 5-9 mm and 9-16 mm were used in equal proportion and mixed with the cement in the ratio of 1:3 and 1:4 respectively. With these six mixes, a total of 18 samples were prepared with 3 samples for each mix category.
Table 0.1 Sample Classification
Sample
Aggregate size
C/A Ratio (by wt.)
A
5-9mm
1:3
B
5-9mm
1:4
C
9-16mm
1:3
D
9-16mm
1:4
E
5-9mm and 9-16mm mixed
1:3
F
5-9mm and 9-16mm mixed
1:4
The clean aggregate sample and cement were first weighted as per their required ratio and were dry mixed. Water was weighted and a small amount of water was added to the mix. The concrete was hand-mixed adding water slowly. A ball of concrete was formed to check the consistency of the concrete. Water cement ratio was fixed as 0.3. first the slump test was conducted on the fresh concrete. The mixed concrete was then placed into the cylindrical mould in 3 layers, tamping each layer 25 times with the tamping rod. The moulds were labelled with sample name and it was left to dry for 24 hours. Samples were taken out form the mould next day and name tags were attached to them for identification and were kept under water at room temperature for curing. Porosity and Permeability test were carried out after 7 days and compressive strength test was carried out after 28 days.
-
Testing of sample specimen
After 7 days, the samples were tested to calculate its dry density, porosity and permeability.
-
Porosity Test
The porosity of the sample was calculated using water displacement method. In water displacement method, weight of water displaced by the sample solid is calculated, which is equals to the volume of the sample solid. At first, an empty clean bucket was taken and its weight was measured as W1. The bucket was then filled with water to its top and its weight was
measured as W4. After that, the sample was taken out from curing pond and kept in bucket and water was filled to top. The weight was measured as W3. The sample was then left outside for 24 hours. After 24 hours, the air-dried sample was kept in the bucket and again the weight was measured as W2. The weight of displaced water was calculated using following equation:
Weight of Displaced Water = ((W4 W1) (W3 W2)) Eq. 3.0.1
The volume of displaced water is equals to the volume of sample solid, which is subtracted from the total volume of the sample to obtain the volume of voids. Porosity is calculated as the ratio of volume of voids to the total volume of sample, and expressed in percentage.
-
Permeability Test
The permeability of the sample was calculated using falling head method. In this method, the sample is subjected an initial water head and time taken to reach final water is recorded. The apparatus was prepared as shown in the figure below.
Figure 0.1 Falling Head Permeameter
The sample was prepared by wrapping it in thin shrink wrap plastic sheet and covered by rubber tightly to prevent any leakage from the side of the sample. A graduated tube was placed above the sample. The height of the exit pipe was fixed above the top level of the sample.
First the water was filled from exit pipe. This helps in removing the air trapped inside the sample. After that, the exit hole was covered and water was completely filled inside the graduated cylinder. The water was allowed to settle for a while and cover placed at exit hole was removed. The time taken (t) for water level to fall from initial height (p) to final height (p) was calculated by reviewing the video recorded during the testing process. The permeability of sample was calculated using following equation:
Permeability (k) = 2.303(aL/At)log (p/p) cm/sec Eq. 3.2
Where, A= Cross-sectional area of sample, a = cross-sectional area of graduated stand pipe.
-
Compressive Strength Test
-
The compressive strength of the samples were carried out following the procedures mentioned in IS 516 (1959). As there was no use of fine aggregates, the top and bottom surface of the sample cylinders were rough, so it was capped using cement as per the code. Since the PC is weaker tha conventional concrete, lower loading rate of 100kg/sq cm/min was applied.
-
RESULTS AND DISCUSSIONS
-
Aggregates Properties
The test results of the aggregates are summarized on the table below.
Table 0.1 Physical Properties of Aggregates
Physical Properties
Aggregate Size
9-16mm
5-9mm
Coefficient of Uniformity (Cu)
1.67
1.59
Coefficient of Curvature (Cc)
1.07
0.96
Flakiness Index (%)
8.13
6.91
Elongation Index (%)
9.95
9.57
Water absorption (%)
0.67
0.24
Apparent Specific Gravity
2.715
2.712
The Coefficient of Uniformity (Cu) and Coefficient of Curvature (Cc) value for both aggregate sizes are near to one indicating the aggregates as single sized or narrow graded aggregates. The flakiness and elongation index for aggregate size 9-16mm were found out to be 8.13% and 9.95% respectively. The flakiness and elongation index for 5-9mm size aggregate
were found out to be 6.91% and 9.57% respectively. Water absorption for aggregate size 9-16mm and 5-9mm were 0.67% and 0.24% respectively. Apparent Specific Gravity were 2.715 and 2.712 for aggregate size 9-16mm and 5-9mm respectively.
-
Density
The average dry density of the samples is listed on the table below. It can be seen that samples A, C and E have more density compared to samples B, D and E with same aggregate size used. This is because former group of samples were mixed with cement aggregate ratio of 1:3 compared to 1:4 for later. Because of this, more cement was available to mix with aggregate resulting in denser concrete compared to samples B, D and F with cement aggregate ratio of 1:4. Samples E and F have maximum density in their respective mix category because of the use of both size of aggregate. This has resulted in a densely packed structure with smaller aggregate occupying the spaces between the larger aggregate thus increasing dry density of PC.
2.175
2.3
Density (g/cm3)
2.116
2.1
2.059
2.078
2.2
2.022
2.1
2
1.9
A (5-9mm)
B (5-9mm)
C (9-16mm)
D (9-16mm)
E (mix)
F (mix)
1.8
Figure 0.1 Average Density of Samples
-
Porosity
The graph plotted for the average porosity of different samples as calculated is shown below.
.23
12.53
12
10
16.00
10.64
.09
14.00
Porosity (%)
12.00
7.99
10.00
5.76
8.00
6.00
4.00
2.00
A ( 5 – 9 mm)
B ( 5 – 9 mm)
C ( 9 – 16 mm)
D ( 9 – 16 mm)
E ( mix)
F ( mix)
0.00
Figure 0.2 Average Porosity of Samples
The porosity of samples A, C and E are lesser compared to samples B, D and F for same aggregate size. On comparing samples, A and C, which were mixed with cement aggregate ratio of 1:3, sample C has better porosity. This is due to the larger aggregate size use in sample C. Similar results can be seen between sample B and D with porosity value of sample D slightly larger than sample B. But for samples E and F, the porosity values are lesser because of the use of mixed aggregate size. The overall porosity of all samples has a smaller value with a maximum value of only 12.53%. The use of flaky and elongated aggregate may be the reason for this as these types of aggregates forms a well packed concrete resulting in less porous structure. Better porosity ca be achieved by using less flaky and elongated aggregates.
2.2
E
2.15
Density (g/cm3)
2.1 A C F
2.05 D
B
2
1.95
1.9
5 6 7 8 9 10 11 12 13
Porosity (%)
Figure 0.3 Comparison between Density and Porosity of samples
The graph between the density and porosity of samples shows that the increase in porosity has resulted in decrease in density. Samples E, A, F, and B have their porosity value in increasing order with their density in decreasing order. These samples have larger difference in porosity and density with change in cement to aggregate ratio from 1:3 to 1:4. For samples C and D, with application of larger aggregate size of 9-16mm, their porosity and density values are higher and the difference in their porosity and density values are smaller with change in cement to aggregate ratio from 1:3 to 1:4. The role of cement paste in deciding the porosity and density of PC is critical for small sized aggregates.
-
Permeability
0.55
0.17
0.70
Permeability (cm/s)
0.49
0.60
0.41
0.50
0.26
0.26
0.40
0.30
0.20
0.10
A ( 5 – 9 mm)
B ( 5 – 9 mm)
C ( 9 – 16 mm)
D ( 9 – 16 mm)
E ( mix)
F ( mix)
0.00
Figure 0.4 Average Permeability of Samples
The above graph shows the permeability values for different samples. Samples A, B, C and D prepared using narrow graded aggregate shows better permeability properties compared to samples E and F. This is because of the formation of interconnected voids, which is possible in concrete prepared using narrow graded aggregates. For same aggregate size, the permeability value has increased with change in cement to aggregate ratio from 1:3 to 1:4. The quantity of excess cement after coating of aggregate is decreased when more amount of aggregate is used in samples B, D and F, compared to samples A, C and E. this has resulted in increased permeability on the former group of samples.
Similarly, from the comparison graph between porosity and permeability, as shown below, we can that porosity and permeability are directly related as an increment in the value of one result in an increment in another. For samples A and B, with aggregate sizes 5-9 mm, the difference in porosity and permeability is large compared to other samples with a similar change in cement to aggregate ratio from 1:3 to 1:4. Samples E and F have lesser values for porosity and permeability because of the use of the different size of coarse aggregates.
14
Porosity (%)
D
12 B
C
10 F
8 A
6 E
4
0.1 0.2 0.3 0.4 0.5 0.6
Permeability (cm/s)
Figure 0.5 Comparison between Porosity and Permeability of Samples
-
Compressive Strength
Comp. Strength (MPa)
20.46
18.71
11.
12
25.00
62
15.72
.11
15.80
20.00
15.00
10.00
5.00
A ( 5 – 9 mm)
B ( 5 – 9 mm)
C ( 9 – 16 mm)
D ( 9 – 16 mm)
E ( mix)
F ( mix)
0.00
Figure 0.6 Average Compressive Strength of Samples
The above figure shows the compressive strength of different PC samples. Samples A and E prepared using cement to aggregate ratio of 1:3 i.e. M20 mix ratio have higher compressive strength with values nearer to 20 MPa whereas sample C
with similar ratio has only compressive strength of 15.72 Mpa. This is because samples A and E were prepared using small sized aggregate of 5-9 mm, with sample A consisting of 5-9 mm aggregate and sample E with mixture of 5-9 mm and 9-16 mm aggregate. Due to the use of small size aggregate in sample A, they are densely packed with enough cement paste for bond resulting in larger value of compressive strength. Similarly, for sample E, use of both size of aggregate has resulted in a uniform structure with small sized aggregates occupying the voids created by large sized aggregates forming a dense structure resulting in larger compressive strength value. Samples C and D have lesser strength value as they were prepared using large sized aggregate 9-16 mm, which formed larger voids resulting in weaker concrete.
13
D
12 B
11 C
Porosity (%)
10 F
9
8 A
7
6 E
5
4
10 12 14 16 18 20 22
Compressive Strength (MPa)
Figure 0.7 Comparison between Porosity and Compressive strength of Samples
From above comparison chart, we can see that the range of change in porosity and compressive strength from sample B with cement to aggregate ratio 1:4 to sample A with ratio 1:3 for same aggregate size of 5-9 mm is larger compared to other samples. The graph shows the inverse relationship between the porosity and compressive strength larger porosity value with lesser compressive strength and vice versa. The change in porosity and compressive strength from sample C to D is subtle. The line between sample E and F for its porosity and Compressive strength follows a steeper slope.
25 0.60
20 0.50
0.40
15
0.30
10
0.20
5 0.10
A (5-9mm)
B (5-9mm)
C (9-16mm)
D (9-16mm)
E (mix)
F (mix)
0 0.00
Porosity (%) Comp. Strength (Mpa) Permeability (cm/s)
Figure 0.8 Comparison of Porosity, Permeability and Compressive strength
From above comparison graph for porosity, permeability and compressive strength, we can see that the slope for the porosity and permeability line are similar in nature, whereas the slope for compressive strength line is inverse in nature. Sample B has the highest value for permeability and higher porosity with lower value for compressive strength. Sample E has highest value for compressive strength with lowest value for porosity and permeability. The difference in properties for sample A to B and E to F are steeper in nature whereas the difference for sample C to D is of milder nature.
Table 0.2 Test results of the samples
Sample
w/c
C/A
Porosity (%)
Permeability (cm/s)
Comp. Strength (MPa)
A (5-9mm)
0.3
1:3
8.31
0.25
18.71
B (5-9mm)
0.3
1:4
12.23
0.54
11.62
C (9-16mm)
0.3
1:3
10.64
0.41
15.72
D (9-16mm)
0.3
1:4
12.63
0.52
12.11
E (mix)
0.3
1:3
6.08
0.15
20.46
F (mix)
0.3
1:4
10.36
0.29
15.14
The above table shows the summary of properties of PC. For two different size of narrow graded aggregated, with mix ratio of cement and aggregate in 1:3 and 1:4, six groups of sample mixes were prepared keeping water cement ratio as 0.3. Porosity in the range of 6.08% to 12.63% were achieved with its permeability value from 0.15 cm/s to 0.54 cm/s. the compressive strength of PC achieved ranges from 11.62 MPa to 20.46 MPa with most of the samples having compressive strength above 15 MPa. Aggregate size 5-9 mm had a greater range in change of properties. Its porosity varied from 8.31% to 12.23% with permeability varying from 0.25 cm/s to 0.54 cm/s. The change in compressive strength was observed ranging from 11.62 MPa to 18.71 MPa. Aggregate size 9-16 mm showed a small change in their properties when mix ratio was changed from 1:3 to 1:4. Samples mixed prepared by mixing both the aggregate sizes had a better strength property over with their value between 15.14 MPa for 1:4 mix ratio and 20.46 MPa for 1:3 mix ratio. But they showed significantly less hydraulic property with porosity ranging only between 0.15 cm/s to 0.29 cm/s.
-
-
CONCLUSIONS AND RECOMMENDATIONS
The study was carried out to prepare Pervious Concrete and study its properties. The size and grading of aggregates and mix properties were finalized after conducting literature review and following different codes and guidelines. Pervious Concrete was prepared by mixing Ordinary Portland Cement with natural riverbed aggregate of size 5-9 mm and 9-16 mm in proportion of 1:3 ad 1:4 by weight, keeping the water cement ratio at 0.3. The PC prepared was tested for its physical properties in two categories as hydraulic property and mechanical property. For hydraulic property, porosity and permeability were measured and density and compressive strength were measured for mechanical property. The results obtained were in accordance to the criteria given by ACI 522R (2010). Compressive strength above 10 MPa was achieved for all samples with maximum value of 20.46 MPa which is suitable for application in light loading areas. Conclusions drawn from the study may be listed as:
-
The size of aggregate and its grading affected both hydraulic and mechanical property of PC with small sized narrow graded aggregate showing better result.
-
Porosity of all samples were relatively lesser compared to results obtained in different literatures. This may be due to the fact that aggregates with flakiness and elongation index of 6.9% to 9.95% were used and also the concrete was poured in the mould in three layers tamping each layer 25 times by tamping rod rendering the concrete dense. However, further study is necessary to validate this claim.
-
PC prepared with larger sized aggregate inn narrow grading resulted in better hydraulic property for both mix proportions. However, they were accompanied with reduced strength.
-
PC prepared with aggregate of both sizes had higher compressive strength in both mix proportions but they had lesser hydraulic property.
-
The results obtained indicate that the prepared PC can be used in light-loading areas like parking lots, sidewalks, bicycle lanes, drains, greenhouses, and playgrounds.
To conclude, PC can be prepared using locally available materials with desirable properties. The application of PC primarily depends on its hydraulic performance. However, it is not sufficient condition as PC should possess enough strength for its application in different loading conditions. Nonetheless, for extensive use of PC, more studies are necessary. Some recommendations are:
-
The effect of freezing and thawing in cold climate.
-
Stresses on PC in hot areas.
-
Effect of vibration in PC due to dynamic loading.
-
Durability of the top surface of PC due to heavy loading.
-
The effect of flakiness and elongation index of aggregates on hydraulic performance of PC.
-
Study on clogging of PC on long term use.
REFERENCES
[1] ACI 522R. (2010). Report on Pervious Concrete. In ACI Commitee 522 (Issue March). https://www.concrete.org/Portals/0/Files/PDF/Previews/522R- 10web.pdf [2] Alam, A., Haselbach, L., & Cofer, W. F. (2013). Three-Dimensional Finite Element Modeling of Pervious Concrete Pavement: Vertical Porosity Distribution Approach. International Journal of Research in Engineering and Technology, 02(12), 767777. https://doi.org/10.15623/ijret.2013.0212129 [3] Ali, M. K., & Kareem, Q. M. sh. (2014). Experimental Study onn Mechaical and Hydrological Properties of Pervious Concrete with Different Water Cement Ratio. Construction and Building Materials, 50(12), 524529. https://doi.org/10.1016/j.conbuildmat.2013.09.022 [4] Chandrashekar, V. C., Tejashwini, P. S., Madhu, K., Deepa, T., & Poorinma, K. (2018). Effect on the Engineering Properties of Pervious Concrete by Partial Replacement of Cement with GGBS. GRD Journals-Global Research and Development Journal for Engineering, 3(3), 17. www.grdjournals.com [5] Chen, Y., Wang, K., Wang, X., & Zhou, W. (2011). Strength, fracture and fatigue of pervious concrete. Chemosphere, 82(October), 15831588. [6] Chindaprasirt, P., Hatanaka, S., Chareerat, T., Mishima, N., & Yuasa, Y. (2008). Cement paste characteristics and porous concrete properties.Construction and Building Materials, 22(5), 894901. https://doi.org/10.1016/j.conbuildmat.2006.12.007
[7] Deepika, K. P., & Fathima, Z. (2020). Utilization of Porous Concrete in Ground Water Recharge. July, 48044806. [8] Huang, B., Wu, H., Shu, X., & Burdette, E. G. (2010). Laboratory evaluation of permeability and strength of polymer-modified pervious concrete.Construction and Building Materials, 24(5), 818823. https://doi.org/10.1016/j.conbuildmat.2009.10.025 [9] IS: 12727. (1989). Code of practice for no-fines cast in situ cement concrete.
[10] IS:2386- Part I. (1963). Method of test for aggregate for concrete. Part I – Particle size and shape. Indian Standards, (Reaffirmed 2002). [11] IS 2386- Part III. (1963). Method of Test for aggregate for concrete. Part III- Specific gravity, density, voids, absorption and bulking. Bureau of Indian Standards, New Delhi, (Reaffirmed 2002). [12] IS 456. (2000). Plain Concrete and Reinforced. Bureau of Indian Standards,New Dehli, 1114. [13] IS 516. (1959). Method of Tests for Strength of Concrete. Bureau of Indian Standards, 130. [14] Jain, A. K., & Chouhan, J. S. (2011). Effect of Shape of Aggregate on Compressive Strength annd Permeability Properties of Pervious Cocrete. IJAERS, I(I), 120126. [15] Kevern, J. T., Schaefer, V. R., & Wang, K. (2011). Mixture proportion development and performance evaluation of pervious concrete for overlay applications. ACI Materials Journal, 108(4), 439448. https://doi.org/10.14359/51683117 [16] Khadka, S., & Basnet, K. (2019). Storm Water Management of Barahi Chowk Area , Lakeside , Pokhara , Nepal using SWMM. KEC Conference, 2(1), 320325. [17] Khankhaje, E., Salim, M. R., Mirza, J., Hussin, M. W., & Rafieizonooz, M. (2016). Properties of sustainable lightweight pervious concrete containing oil palm kernel shell as coarse aggregate. Construction and Building Materials, 126, 10541065. https://doi.org/10.1016/j.conbuildmat.2016.09.010 [18] Lian, C., Zhuge, Y., & Beecham, S. (2011). The relationship between porosity and strength for porous concrete. Construction and Building Materials, 25(11), 42944298. https://doi.org/10.1016/j.conbuildmat.2011.05.005 [19] Manan, A., Ahmad, M., Ahmad, F., Basit, A., & Ayaz Khan, M. N. (2018). Experimental Investigation of Compressive Strength and Infiltration Rate of Pervious Concrete by Fully Reduction of Sand. Civil Engineering Journal, 4(4), 724. https://doi.org/10.28991/cej-0309127 [20] Merighi, J. V., Fortes, R. M., & Bandeira, A. (2006). Study of the concept of porous concrete for use on airport runways. 25th Annual Southern African Transport Conference, SATC 2006 – 2010: Will Transport Infrastructure and Systems Be Ready, 2006(July 2005), 4453. [21] Moretti, L., Di Mascio, P., & Fusco, C. (2019). Porous Concrete for Pedestrian Pavements. Water (Switzerland), 11(10). https://doi.org/10.3390/w11102105 [22] Qin, Y., Yang, H., Deng, Z., & He, J. (2015). Water permeability of pervious concrete is dependent on the applied pressure and testing methods. Advances in Materials Science and Engineering, 2015, 17. https://doi.org/10.1155/2015/404136 [23] Rajasekhar, K., & Spandana, K. (2016). Strength Properties of Pervious Concrete Compared with Conventional Concrete. IOSR Journal of Mechanical and Civil Engineering (IOSR-JMCE) e-ISSN, 13(4), 97103. https://doi.org/10.9790/1684-13040397103 [24] Rami, A. K., & Joshi, T. M. (2015). Pervious concrete: Effect of Sand in Permeability of Pervious Cocrete. Concrete Construction – World of Concrete, 60(1112). https://doi.org/10.1007/978-3-642-41714-6_161018 [25] Sharanya, G. (2019). Investigation on permeability characteristics of pervious concrete. International Journal of Advance Research, Ideas and Innovations in Technology, 5(3), 793797. [26] Shrestha, K. K. (2019). Perspectives of Storm Water Drainage in Pokhara. September. [27] Takhelmayum, G., & S.N, S. (2012). A Laboratory Study on the Effect of Compressive Strength of Pervious Concrete on Low Volume Road Using CSD.International Journal of Engineering and Social Science, 2(11), 113117.
[28] Tennis, P. D., Leming, M. L. ., & Akers, D. J. . (2004). Pervious concrete pavements. In International Journal of Civil Engineering and Technology (Vol.8, Issue 4). https://doi.org/10.3141/2113-02
[29] Xie, N., Akin, M., & Shi, X. (2019). Permeable concrete pavements: A review of environmental benefits and durability. Journal of Cleaner Production, 210, 16051621. https://doi.org/10.1016/j.jclepro.2018.11.134 [30] Zhu, H., Yu, M., Zhu, J., Lu, H., & Cao, R. (2019). Simulation study on effect of pereable pavement on reducing flood risk of urban runoff. International Journal of Transportation Science and Technology, 8(4), 373382. https://doi.org/10.1016/j.ijtst.2018.12.001