
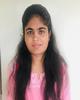
- Open Access
- Authors : Meenakshi Patel , Simson Raju
- Paper ID : IJERTV9IS100128
- Volume & Issue : Volume 09, Issue 10 (October 2020)
- Published (First Online): 16-10-2020
- ISSN (Online) : 2278-0181
- Publisher Name : IJERT
- License:
This work is licensed under a Creative Commons Attribution 4.0 International License
A State of Review on Hydraulic Fracturing Fluid Properties using Nanoparticles Application in An Unconventional Reservoir
Meenakshi Patel*
Department of Petroleum Engineering University of petroleum and energy studies Dehradun, India
Simson Raju
Department of Petroleum Engineering University of petroleum and energy studies Dehradun, India
Abstract Hydrofracturing or hydrofracking of rock formations is a technique that is used to recover oil and gas from unconventional reservoirs. Hydrofracturing is a method if injecting high pressurized fluids into a wellbore to generate cracks or fissures in the reservoir formations. The fluids that are used for hydro-fracturing should have some properties such as stiffness, heat resistance, viscosity, etc. To get these properties we use certain addictive's. Some hydro-fracturing fluids do not meet the properties that are required for fracturing there come to the introduction of nanoparticles. Nanoparticles due to its distinctive characteristics it can sustain tremendous rheological properties at high pressure and temperature in down-hole conditions. The methods such as nano-emulsion, nano- dispersion techniques are used depending upon the properties required. This review paper briefs the comparison of fracturing fluids which are used traditionally to the nanotechnology used in hydrofracturing.
Keywords Hydraulic Fracturing, Fracking, Nanoparticles, Unconventional Reservoir, Fracturing Fluids, Nanotechnology
-
INTRODUCTION
Global primary consumption slowed down at a rate of 1.3% last year (2019), the growth rate of all fuels slowed down than their 10 years average. Natural gas gave a major contribution of nearly 40% for this increase. In energy demand, China, India, and Indonesia account the two-thirds of the global rise but the USA and Germany's demands declined. Globally, the production of oil fell by 60,000 BPD and consumption grew by an average of 0.9 million barrels/day (BPD), i.e. 1.5% China (680,000 b/d) is the largest contributors to growth. Global natural gas production increased by 132 BCM, (3.4%) almost two-third increase from the US (85 BCM), which is recorded as the largest yearly growth in history seen by any country with 34 BCM in Russia, 23 BCM in Australia, and 19 BCM Iran next to the USA. Consumption of Natural gas (NG) rose by 78 billion cubic meters (BCM), nearly 2%, below the rates of growth (5.3%) in 2019 (fig.1) [13]. The production of oil in India accounts for 826 thousand barrels per day and oil consumption increased up to 5271 thousands of barrels per day. The natural gas production in India accounts for 26.9 BCM and consumption accounts for 59.7 BCM in 2019.
The energy demand is increasing linearly and the production scenario of proved reserves (conventional reserves) is diminishing for the last decades there comes the need for the
exploitation of natural gas from unconventional reserves. Unconventional reservoirs include – Gas hydrate, Shale gas, Coal-bed methane (CBM), and tight gas sands. Recovery of hydrocarbons from these unconventional reservoirs have many technical and economic challenges. Ultra low permeability and low porosity are the main reason for this challenges. Generally, hydraulic fracturing stimulation will be required to produce hydrocarbon from any formations with the permeability less than 1 mD [42].
Fig.1 Crude oil (BPD) and Natural gas (BCM) scenario of total world Source-BP Statistical Review of World Energy, 2020 69th edition
-
HYDRAULIC FRACTURING Unconventional reservoirs are greatly heterogeneous, complex, and have very low permeability. Furthermore, the robust chemical and physical interactions among pore surfaces and fluids lead to the unsuitability of conventional methods [17]. Therefore extended studies of petro physical properties of these reservoirs and new techniques are needed. Petro physical studies include the study of lithology, permeability, fluid saturation, porosity, and fluid characterization of the reservoir.
Horizontal drilling with hydrofracturing is the current technique used for effective production from the unconventional reservoir. Hydrofracturing also called fracking is a stimulation method that improves the productivity of well by increasing/enhancing permeability which enables the movement of oil and gas to the wellbore. Rocks that have permeability less than 1md are generally brilliant contenders for stimulation using hydraulic fracking. Hydrofracturing is the technique of injecting fluid at high pressure into the well up to the extent which will fracture or breakdown the rock formation. The first hydro-fracking was done in 1947 by Pan American Petroleum Corp on a gas well operated in the Hugoton field, Kansas [52].The fracturing fluid used was NAPALM (a mixture of cross-linked with naphthenic acid and gasoline gel with palm oil) which was expensive and hazardous. Due to its hazardous nature introduction of safer fluids is developed in which water is kept as base fluid. The constitutes for hydraulic fracturing include mainly water which is the base fluid with proppants such as clay, sand, ceramics, etc. And cross-linked fluids such as a polymer, gelling agents, stabilizer, breaker, etc.
Hydro-fracking is done with a pressure which is higher than the pressure of fracture in the formation, which is explained using the below (1)-
Sum= in-situ stresses + rocks tensile strength (1)
As soon as a fracture is formed it can proliferate at a pressure which is called the fracture propagation pressure
Fracture propagation pressure = Net pressure drop + in-situ stress +near well-bore pressure (2)
Net pressure drop- pressure drops down the fracture as the result of viscous flow in the fractures + only pressure rise caused by tip effects (3)
Near wellbore pressure is the pressure drop of the viscous fluid which is flowing through the perforations and resultant pressure drop from tortuosity between the wellbore and the propagating fracture.
The technique of Hydrofracturing became a trending "game- changer" in countries for unconventional juncture is full filling the demand of the energy sector but while designing an effective and efficient fracturing treatment various challenges came across after the process is accomplished due to the large number of properties which affects the treatment like reservoir properties(depth, pressure, and temperature) and rock properties(porosity, permeability, tensile strength, and composition) which play a role for considering the fracturing fluid-type, volume, pumping rate, etc. The process involved high-pressure pumping of hydro-fracturing fluid (water-95%, sand, and chemicals) which fracture the rock formation for freely flowing hydrocarbon. Once the process is completed hydrocarbon flows to the surface with flow back fracturing fluid. But at the surface, only 5-60 % of the water and hydro- fracturing fluid used flows back, and the rest become a threat for under surface with chemicals within it which contaminate the water table and affect the turbidity, odor, and color and become a major environmental issue. During this process many toxic chemicals and methane (major greenhouse effect)
gas evolved which have the potential higher than carbon dioxide to trap the heat and results in air pollution.
-
CONTROLLING FACTORS
-
Physical /chemical and Mechanical/geo-mechanical
It is necessary to study about properties (formation/ rock/reservoir) because it is assumed that rock medium to be continuous but they have various types of discontinuities such as tensile strength, joints, faults, formation,shear-strain relation, thickness, and unconformity, etc. And these properties can stop the hydraulic fracturing fluids at contact or control the extending of the fracture [17]. The equation can be given as Compaction-stress maximum stress/minimum stress.
The strength of the material is first analyzed for crack initiation. These analyses obtained the load level of the structure and also provide the location within the structure where the hydraulic fracturing fluid can reach its tensile strength. And this information provides information where the first crack can be made. Strength is obtained from the stress-strain relation of the rock materials which contribute to the work-energy required to initiate a crack depends on the types of rock (brittle or softening material).
-
Pressure
The pressure needed for hydraulic fracturing can be as high as 15,000 psi and the injection rate can be as much as 100 barrels per minutes.
-
Fracture
A fracture can be natural or induced. Natural cause due to any crack in the rock and induced while coring. Fractures are categorized based on their morphology. Unequivocal natural fractures, very probable natural fractures, probable natural fractures, and induced fractures. Fractures can be measurable and not measurable, micro and macro-fractures, and open and close fractures. Depends on the axis of folding fractures they can be longitudinal (along the folding axis), transversal (perpendicular to the folding axis), and diagonal (in-relation with the folding axis).
-
-
TYPES OF HYDRAULIC FRACTURING FLUID
-
Water
95% of the fracturing fluid comprises water, 4.5% sand, and the remaining 0.5% other chemical additives. Water is the primary principal carrier fluid in hydraulic fracturing because several quantities of water are used for fracturing a multistage horizontal shale gas reservoir. Major sources of water come from lakes, rivers, etc. Which are surface waters. Because the important factor is the quality of water if contaminations present in the water it will reduce the efficiency of the additives during the treatment. After perforation, the fractures are needed to be held for free-flowing of the hydrocarbon and this is taking place by using proppants that hold the fracture open until the hydrocarbon release. It depends on the well- fractured conditions of how much chemical additives are needing use. Chemicals perform multiple roles, comprising controlling the development of bacteria and avoiding the well
casing corrosion. Normally, 3 to 12 additive chemicals in very low concentrations are being used, dependent on the properties of the formation to be fractured and water characteristics. Every constituent functions a specific purpose.
-
Proppants
After the perforation is done the fracturing fluid seeps into cracks and extends the fracture due to more pressure and as the pumping pressure by fracturing fluid stops the fracture tries to reclose because of the compressive force generated by the above rock strata hence to prevent this reclosing proppants are mixed with fracturing fluids. Proppants hold the fracture open even after pressure is eliminated.
Frac-sand, resin-coated sand, silica grains, synthetic grains are used as proppants.
-
The selection of proppants is based on reservoir formation and permeability of the rock.
-
At deeper depths, the high strength proppant is used to withstand the pressure
Frac sand- "Frac sand" is round grains and a natural material made up of sandstone with high purity of quartz. Frac sand sizes range from as small as 0.1 to 2 millimeters in diameter. But general sand is used in between 0.4 to 0.8 millimeters in hydraulic fracturing. Due to the erosion and weathering cycle rock unit of Jordan Sandstone, hickory sandstone, and St. Peter sandstone consists of quartz grains and become potential sources of Frac sand material.
Ceramics beads- it is made of kaolin clay or powered bauxite which is bonded into tiny beads and heated at very high temperatures. As sand cannot withstand high shutting stresses (up to 6000 psi) so proppants made from ceramic are used. Example sintered bauxite, kaolin, magnesium, silicate, etc.
Resin coated proppants (RCP) – it enhances the conductivity of Frac sand. Resin covering can stickup pieces of damaged grain in the coatings thus restricting the flow of proppant back into the wellbore. Resins- furan, polyester, vinyl esters.
-
-
Chemical
Chemicals have several purposes in hydraulic fracturing. It will control the development of bacteria, corrosion of well casing. Chemicals are also used to make sure whether the fracturing is done is efficient and effective.
Depending on the characteristics of the wells to be fractured the number of chemical additives changes. A low concentration ranges between 3 to 12 additive chemicals will be needed for typical fracture treatments, which depend on the water characteristics and the fractured shale formation. Each component serves a specific and detailed engineering purpose.
-
-
BASED ON FLUIDS:
-
Water-based fluids
These fluids contain water and proppant. These fluids carry proppant in low quantity (particle size > 400 µm) because of the low viscosity of fluids (2 to 3 cp) [32]. Due to the low quantity of proppant, these fluids don't affect the size of the fractures but the cracks are initiated. Water-based fluids are
undesirable for formations that are water-sensitive and contain a large amount of clay because it affects permeability due to a large volume of proppants remains into fractures because of low viscosity and as a result clay gets swells [8]. Due to the use of a large amount of water the disposal of wastewater has become a major problem. The quantity of hydraulic fracturing is enough large that causes a large cost.
-
Polymer-based fluids
Polymer-based fluids contain water, proppants, and gelling agents. To improve the viscosity gelling agents are added into water-based fluids because of its low viscosity such as biopolymers or synthetic polymers (guar gum, and derivatives carboxyl methyl hydroxyl propyl guar (CMHPG), hydroxyl propyl guar (CMHPG), and polyacrylamide [50]. Guar gum is used most among all gelling agents because its swelling rate is low due to its high viscosity. For high-temperature reservoir, polymer-based fluids are not suitable due to high molecular weight they start degrading and gets deposited [51]. Additional treatment requires the breakdown of the insoluble residue which reduces the proppant's conductivity by 50% and clog the pores [8][2]. Additional treatment-breakers include
-
Cross-linked polymeric fluid.
-
Metallic cross-linkers-
-
Zirconium and Titanium complexes.
-
Borate cross-linked guar fluids [4].
But the effectiveness of the breakers is limited beyond 300o F
[3] and when the pH is more then it is thermally al stable [48]. Thickening agents (like-Dendrite star polyacrylamide (DSPAM)) are also used as additional treatment sometimes depends on reservoir conditions.
-
-
-
Viscoelastic surfactants (VES) based fluids
These fluids consist of water, proppants, and surfactants. Polymer-based fluids clog the pores due to its high molecular size (mostly guar) so to improve low molecular size viscoelastic surfactants are used which is having 5000 times lesser weight than that of the guar [15]. These fluids with other inorganic salts consist of two surfactants or co- surfactants and this mixture can be anionic-cationic, ionic- zwitter-ionic, and anionic-anionic mixed systems. Due to high viscosity effective proppant carrying capacity and after fracturing it breakdowns into low viscosity and flow back without imbibition and no residue left [24][10][54][50]. Limitations of viscoelastic surfactants in field applications are-effectiveness of the viscoelastic surfactant can be shown up to the temerature 200of beyond this temperature non- viscous structures are acquired by viscoelastic micelles [24]. Recent studies show that viscoelastic surfactants can be reused [54], and adjusting the pH-value gelling formation and fracturing fluids breaking process can be controlled [50]. And also in recent, it is observed that by using anionic based surfactants thermal stability beyond the 90oc is high due to which low formation damage is shown with 97% returned permeability [34].
-
Foam-based fracturing fluids
This fluid contains foaming agents and dispersion of gas in liquids. It carries effective proppants due to high apparent viscosity. Due to high viscosity less leaking of fluids taking place into fractures by which an effective clean-up can be done during fluid flow back [22][53]. Water sensitive formations large quantity of compressed gas is used instead of water which minimizes the water usages [19]. In unconventional reservoir nitrogen-foam, carbon dioxide foam, binary (nitrogen and CO2) foam, and viscoelastic foam are used. In ultra-dry foams, water content is <10 % [40].
Types of chemical additives in HF fluids
Function
Examples
Biocide
Kills bacteria.
To prevent excessive biofilm formation bacterial control is necessary for hydraulic fracturing operations because that may lead to clogging, consequently inhibiting gas extraction produce toxic hydrogen sulfide, and induce corrosion leading to downhole equipment failure.
Glutar-aldehyde. Quaternary ammonium compounds.
Cl02-chlorine dioxide Naclo(sodium hypo- chloride),
Dimethyl oxazolidine
Breaker
Reduce fluid viscosity of the various polymers used or by reducing the molecular weight facilitates the flow back of residual polymer which allows for clean-up of the proppant pack. During the treatment, these materials would be inactive and then after some time suddenly 'spring to action' when pumping stops, promptly breaking fluid back to a low viscosity preparing the fracture and formation for flow.
Oxidizer-ammonium persulfate
Sodium persulfate Calcium, and magnesium peroxides.
Acids- HCL, acetic acid. Enzymes-protein molecules- hemicellulose, cellulose, amylase, and pectinase.
Buffer
Controls the pH level of the base fluids by which the hydration, dispersion, and crosslinking of the fracturing fluid polymers can be engineered. To maximize the effectiveness of other additives such as cross-linkers.
K2CO3 NA2CO3 CH3COOH
Fumaric acid
Clay stabilizer
Prevents clay swelling by preventing the water from interacting with the reservoir mineralogy and also prevent the migration of the formation clays which could block pore spaces thereby reducing permeability.
KCl, NH4Cl,
Tetra-methyl ammonium chloride.
Friction reducer
Reduce friction.
These materials are added into water to manufacture called "slickwater". Add at the concentrate of 0.25 to 2 gal/1000 gal.
Anionic copolymer, Polycyclic acid (PAAC), Polyacrylamide(PAAM), Partially hydrolyzed, Polyacrylamide (PHPA).
Types of chemical additives in HF fluids
Function
Examples
Biocide
Kills bacteria.
To prevent excessive biofilm formation bacterial control is necessary for hydraulic fracturing operations because that may lead to clogging, consequently inhibiting gas extraction produce toxic hydrogen sulfide, and induce corrosion leading to downhole equipment failure.
Glutar-aldehyde. Quaternary ammonium compounds.
Cl02-chlorine dioxide Naclo(sodium hypo- chloride),
Dimethyl oxazolidine
Breaker
Reduce fluid viscosity of the various polymers used or by reducing the molecular weight facilitates the flow back of residual polymer which allows for clean-up of the proppant pack. During the treatment, these materials would be inactive and then after some time suddenly 'spring to action' when pumping stops, promptly breaking fluid back to a low viscosity preparing the fracture and formation for flow.
Oxidizer-ammonium persulfate
Sodium persulfate Calcium, and magnesium peroxides.
Acids- HCL, acetic acid. Enzymes-protein molecules- hemicellulose, cellulose, amylase, and pectinase.
Buffer
Controls the pH level of the base fluids by which the hydration, dispersion, and crosslinking of the fracturing fluid polymers can be engineered. To maximize the effectiveness of other additives such as cross-linkers.
K2CO3 NA2CO3 CH3COOH
Fumaric acid
Clay stabilizer
Prevents clay swelling by preventing the water from interacting with the reservoir mineralogy and also prevent the migration of the formation clays which could block pore spaces thereby reducing permeability.
KCl, NH4Cl,
Tetra-methyl ammonium chloride.
Friction reducer
Reduce friction.
These materials are added into water to manufacture called "slickwater". Add at the concentrate of 0.25 to 2 gal/1000 gal.
Anionic copolymer, Polycyclic acid (PAAC), Polyacrylamide(PAAM), Partially hydrolyzed, Polyacrylamide (PHPA).
Table 1- Types of chemical additives with functions and examples [42].
Iron controller
Keeps iron in solution Prevents precipitation of sulfates and carbonates (calcium carbonate and sulfate, barium sulphate) which could plug off the formation.
Acetic and citric acid, Ammonium chloride, Ethylene glycol,
Poly-acrylate,
Surfactant
Lowers surface tension-to improve the fluid recovery and compatibility between the formation matrix (formation fluids) and the fracturing fluid.
Fluorocarbon, Nonionic methanol, Isopropanol, Ethoxylated alcohol.
Gel stabilizer
Reduce thermal degradation
MEOH,
Sodium thio-sulphate.
Gelling agents
Increase the viscosity of the fracturing fluids.
As a result, fluid will carry more proppants into the fractures.
To improve proppant transport these gelling agents reduce the fluid loss, and then the friction pressure allows crosslinking.
Guar gum, Petroleum distillates, Hydroxyl ethyl, cellulose(HEC), Viscoelastic, Surfactant (VES).
Proppants
Proppants hold the fractures and allow fluids to flow more freely to the wellbore.
Sand (sintered bauxite, ceramic beads, zirconium oxide, etc.)
Corrosion inhibitor
Reduces rusting on steel tubing, tools, well casings, and tanks( used only in fracturing fluids that contain acids)
Methanol,
Ammonium bi-sulphate (for oxygen scavengers).
Solvent
Additives (soluble in oil, water, and acid-base treatment fluids) are used to control the wettability of contact surfaces or to prevent/break emulsions
Several aromatic hydrocarbons.
Cross- linkers
To increase the molecular weight of the polymer used cross-linkers are used which is achieved by crosslinking the polymer backbone into a 3D structure. This results in increasing base viscosity of the linear gel from less than 50 cps into the 100's or 1000's of cps range.
Titanium and zirconium Borate(which is in the form of boxic acid) Soluble salts of Calcium, Magnesium, and organic borate complex.
-
-
MAJO CHALLENGES WHILE TREATMENTS
-
Due to the low permeability of the rock fracturing fluid loss takes place it means less volume of fracturing fluid is fracturing the formation while treatment and define the efficiency of the entire process. A team of researcher geologist William brace of M.I.T in 1960 discovered a phenomenon of DILATANCY-when a rock reaches its breaking point a minute crack is formed why which fracturing fluid leak-off from the main fracture.
-
A water-sensitive reservoir causes an imbibition effect results in the swelling of clay particles in the reservoir which later dislodge the crack and fluid loss takes place. Swelling causes a reduction of the permeability of the formations
-
If the reservoir fluid is gas then the fracturing fluid takes place in capillaries and is bound by a capillary force which turns into a fluid loss, reduces permeability and increases the clean-up time and if the reservoir pressure is less may cause permanent damage to the formation.
-
Rock matrix also affects the treatment if the formation is hard it pulverized the proppant and which results in the decrease of flow capacity and if the formation is soft proppants lodge into the pores and may clog the pores.
-
Several researchers and groups have come out with a solution by developing nanoparticle methodology which can improve the hydraulic fracturing technique or conductivity or efficiency. Due to its tremendous features like small size, high shear rate, large surface to volume ratio, etc.
-
Larger tonnes of water are required for fracturing.
-
Limited fracture-width due to the size of proppants in fluids.
-
Reduced %-flow back-water recovery and affects the environment.
-
-
-
NANOTECHNOLOGY IN HYDROFRACTURING
Nanotechnology is an advancement in science which is a manipulation of matter for the fabrication of nanoscale properties with a size of 1-100nm. Due to the small size and excellent properties, it has been widely used. Nanotechnology applications in oil and gas increased new possibilities for researches with excellent results.
Nanoparticles due to its distinctive characteristics at high temperature and pressure it can sustain excellent rheological properties at downhole conditions. Consists unique characteristics like Nano size ranges from 1 nm to 100 nm and having a high ratio for the surface area to the volume which enhances the stability of fracturing fluid at downhole with the high shear rate at a higher value of temperature and pressure [55][23]. To improve the conductivity of hydraulic fracturing and to enhance the rheological characteristics of hydraulic fracturing fluid-like polymer-based, viscoelastic based and foam-based fluids, nano-materials are used as nano cross-linkers and as bi-polymer nano-composites. Recently using Nanoparticles are- carbon nanotubes (CNT), polycrystalline diamond nano-composites, aluminum oxides, nano-silica, copper oxide, and low-cost nanoparticles such as
-
silicon dioxide (SiO2), calcium carbonate (CaCO3), and fly ash. Nanoparticles at the downhole improve the structural strength and viscosity of viscoelastic surfactant and water or polymer or foam-based fluids respectively.
Fig.2 Schematic representation of nanoparticles infiltrating pores spaces in rock formation [43].
Nanoparticles can be used for several technical functions in hydrofracturing:
-
Proppants
-
Clay stabilizer and Formation control additive
-
Additive for Fluid loss control in viscoelastic surfactant fluids(VES) and cross-linker
-
Breaker systems
-
Biocides
-
Surfactant system
-
Most of the nanomaterials used or proposed for applications in hydrofracturing are inorganic-mainly metals and metal oxides. The technical functions of nanoparticles vary with chemical composition, size, and other petrophysical properties.
The use of nanomaterial improves hydrocarbon production by enhancing the additives performance, fluid performance, or proppant ability in unconventional rock formations (e.g. higher production rates). The observed results with the use of nanoparticles are cost-effective and eco-friendly in comparison to the traditional methods.
Addictive
Advantages of nanotechnology application compared to traditional fluids
Proppants for tight formations
Ultra-light proppants
Increased well life.
-
Increased area for flow and fracture network, reduced fluid loss, improved percolation, and increased well productivity.
-
Less settling and reduced density.
-
Improved penetration in the rock formation.
-
Smaller volumes required for fracture job.
-
Stiffness, stable, and greater heat resistance distortion properties.
-
Additives and porous proppants can be carried to release directly into a fracture in response to environmental conditions.
-
Hollow proppants- the manufacturing process can be
Addictive
Advantages of nanotechnology application compared to traditional fluids
Proppants for tight formations
Ultra-light proppants
Increased well life.
-
Increased area for flow and fracture network, reduced fluid loss, improved percolation, and increased well productivity.
-
Less settling and reduced density.
-
Improved penetration in the rock formation.
-
Smaller volumes required for fracture job.
-
Stiffness, stable, and greater heat resistance distortion properties.
-
Additives and porous proppants can be carried to release directly into a fracture in response to environmental conditions.
-
Hollow proppants- the manufacturing process can be
Table2. Application of nanotechnology in addictives and the advantages over traditional HF fluids [47].
controlled at a molecular scale to create proppants particles that are precisely tailored for any rock formation
Strengthen proppants
Fluid loss/cross-linker in VES
Cross-linker /polymeric
Breaker system
Formation fines control
Biocide
Surfactant system
Fracturing/CO2 based fluids
-
Fiber-coated proppants advance the mechanical properties such as compressive strength and suspension capability.
-
Hydraulic cement- the presence of nano bentonite provides better mechanical properties and a significant reduction in permeability ( 29% to nearly 80%) as compared with heavy bentonite
-
Increased/enhanced fluid viscosity at a greater temperature.
-
Reduced amount of surfactant used in fracturing fluid and at low temperature, the easier breaking of gel in a fluid is found
-
Environmental friendly.
-
Enhanced viscosity.
-
Increased time for the crosslinking process
-
Stable and extended life compared to liquid breakers in VES (viscoelastic surfactants) fluids.
-
Controlled release of internal breakers (nano-encapsulation)
-
Prevents fine movement close to the wellbore causing wellbore and formation damage.
-
Increased settling time, properties such as not settling in mud pit and suspension.
-
Compared to conventional surfactants-proppants permeability is higher
-
Improved ability in lowering the interfacial tension and inreased rock wettability.
-
Improved asphaltene and paraffin removal.
-
Less treatment fluid need for remediation which is environment friendly.
-
Environmentally suitable and chemically safe (biodegradable, plant-derived, nontoxic, and nonhazardous).
-
Decreased Pressure to initiate cleaning up.
-
Increased fracture in the rock formation.
-
-
DETAILED RESULTS OF NANOMATERIAL BY TECHNICAL FUNCTION
-
Proppants
Proppant particles placed in fracture form a pack or layer must have excellent mechanical properties. The mechanical properties include stiffness (deformation resistance), stability, and compressive strength united with durability to prevent the formation of fines particles. Another important property is that heat resistance (to withstand high compressive load and high temperature).
It has been found that Nanoparticles can increase the characteristics of the mentioned mechanical properties [35]. It also has to be noted that the development of mechanical properties activates variations in other properties such as by reducing the density drastically progresses the toughness and
strength [47], but as whole nanoparticles are selected based on the application.
-
Ultra-light proppants (ULP)
Two dissimilar kinds of nanotechnology applications are proposed for the production of ULP. A different kind of nanocomposite material for Ultra-light proppants production have been claimed. The European research organization JRC found from detailed literature that an innovative class of thermoset polymer nanocomposites contains a light thermoset polymer matrix with nanoparticles from an inorganic substance. Specific models of materials that can be considered as nanofillers (addictive in solid form) and have particles in the size from 1to500 nm are given: carbon black, nanofibers, and carbon nanotubes. The research claims that these proppants, both nanofiller constituents, and polymer, have a lesser density compared to the density of normal ceramic and sand-based proppants. This permits proppants passage without settling into the rock formation compared to the normal proppants used before. The result observed is that it shows more fracture length effectiveness, particularly while using fracturing fluids such as Visco-elastic surfactant fluids which have low viscosity. Other important properties include better resistance to high-temperature distortion, stability, and stiffness in the subsurface (fig 3). Concentrations and lesser volumes of nanoparticle proppants are required to create needed fracture conductivity and width. United with a better effective length of fracture, the capability to keep the proppant as a single layer would help to attain greater hydrocarbon production for a longer period. A test was performed [11] , on proppant particles of 1.19-1.41 mm size made of 5.635% ethyl vinyl benzene, 84.365% styrene, 0.5% by weight of Monarch 280 (carbon black 310 nm) and10% di-vinyl benzene as nanofiller in contrast to a reference proppant particles of the same size without nanofiller. The outcome explained the benefits of using the nanoparticles in terms of improved recovery for the conductivity of liquid under a compressive stress of 4000 psi at a temperature of
190 °F. The test was conducted for 260 hours and the conductivity of proppant with nanoparticles was found to be 50% better than the sample which is used as a reference.
The next production of ULP using nanotechnology applications is the porous materials properties. Solid materials which have pores of dimension up to 10*3 nm are Porous materials. A major reduction of weight happens when there is an existence of cavities which decreases the density of the material. An experiment [46], involves carbon nanofibers (CNF) made on the surface of a core (proppants). Carbon fibers give a low density and a surface with high porosity that decreases the total density of the proppants particles. Additionally, the writers claims that carbon nanofibers coated on proppants might have the potential to get mixed in the fractures over the surface fibers and thus remaining back in the fractures till the removal of fracking fluid.
Fig 3. Shows the proppants and nano-proppants distributed in fractures and micro-fractures [12].
-
Proppants for tight formations
Tight shale has lower permeability and brittle nature therefore linear gels, slickwater and water fracs (low viscous fluids) are typically applied [45]. These fluids make fractures with a longer length and minor width which benefits in the interconnection between natural fractures and network formed within rock.
It has been found in the literature [12], that the use of nano proppants than normally used proppants which can extend the fracture dimension of the network by introducing much lengthier micro-fractures combined with natural fractures. This increases the enhanced well productivity compared to traditional proppants.
-
-
Cross-linker and fluid loss addictives in VES
Viscoelastic Surfactants -based fluids have two main disadvantages:
-
Fluids based on VES are incapable of information of filter cake, which causes a huge quantity of fluid loss into the rock (porous) matrix and also to the damaged formation.
-
Thermal stability is low for these fluids which have restricted the usage example: for well stimulation in tight gas reservoirs [30].
It has been explained in the research paper [47] that nanoparticles have the ability to improve and stabilize viscosity while mixed with VES fluids and this process is called PSEUDO CROSS LINKING . It is the phenomenon of the creation of a three-dimensional network in micellar solution, the nanoparticle act as a physical cross-linker by the creation of micelle-nanoparticle junctions. Like this way addiction of nanoparticles in VES fluids increases and maintains the viscosity at higher temperatures thereby reducing the fluid loss in the rock formation. [51] states Guar gum gel viscoelastic property is increased when it is cross- linked with nano silica cross linker due to increase of intermolecular forces and the stability of nano cross linker structure enhances by the nano cross linker (fig.4).
Fig.4 Crosslinking mechanism between nano cross linker and guar gum [20].
-
-
Breaker
A breaker is used to break the long-chain molecules into shorter molecules to reduce the viscosity of fracturing fluid. Presently two types of breakers are commonly used:
-
Internal breakers- which is added directly to fracturing fluids
-
External breakers- which is being added directly to the flow back
For proper fracturing of the hydrocarbon-bearing rock formation, the delayed release of internal breakers is an important factor. Encapsulation techniques (fig.) are used to activate internal breakers but due to the larger size of the capsules, which are usually designed to break open when the fracture recloses at the end of the injection which results in incomplete degradation of the filter cake. Usually, at the downhole conditions, the breakers are activated at a controlled rate over time (1-24 hours).
Nanotechnology can increase the performance of normally used breakers by using the technique of nano-encapsulation and deliver clarifications to the challenging problems of internal breakers for VES fluids [7]. The breaker may be prepared by a semiconductor nanomaterial of a thickness between 1-1000nm [31]. The nanomaterials used are inorganic (a combination of silicon carbide cuprous oxide, cupric oxide, silicon, germanium nitride, germanium, germanium nitride, etc.) And organic nature (pentacene, anthracene, polypyrrole, or polyaniline). The author claims that the observed result shows the breaker nanoparticle had a long life and was stable in comparison to traditional liquid breakers in VES fluids. The authors added that the change may occur in the breaking of the aqueous fluid upon addig the breaker nanoparticles and it is assumed to happen with the help of metal catalysts. The breaking may occur as an effect of-
-
A rearrangement of the bond on the VES fluid.
-
An addition to VES (, elimination (decomposition, degradation) of VES.
-
Chemical redox reaction.
-
-
Biocides
Biocides are toxic which can cause effects on the surrounding ecosystem when it is leaked from wellbores to aquifers. The concentration of biocide used is in large quantity which makes it expensive. Usually biocides breakdown quickly so it must be replaced causing increased cost. There comes the need or application of nanoparticle biocide.
An Application of nanoparticle biocide in fracturing fluids
[49] states the use of core-shell nanoparticles with a material (nonmetallic) and a coating of Ag and Ag2O. The metallic nanoparticle composition covers metallic silver nanoparticles that are lastingly or semi-permanently merged to water that use the multiple modes of biocide act to terminate bacteria. The structure and small size of the nanoparticle help it to remain suspended and not settle or settling time is higher in the mud pit. It is demanded that biocide with the nanoparticle composition (silver nanoparticle) maintain the concentration and efficiency than traditional biocides. -
Surfactant
The main objective with surfactants in frac-fluids is to decrease IFT among the fracture surface (rock) and fluid i.e., to decrease the water surface tension and which in turn reduce the flow of fluids to the porous formation, and starts its retrieval after flow back fluid. Hence surfactants guarantee the conductivity of proppants recovery before starting producing hydrocarbons.
Nanotechnology applications as a surfactant are based on nanoemulsion, nanoaddictives for emulsions, and nano- dispersions.
The patented product G-CLEAN WELL WAKE UP! By Green Earth Technologies is an oil well stimulus solution with preparations specially plotted for breaking the paraffin or asphaltenes and eliminate the build-up from the well [28]. This describes the application executed in G-CLEAN WELL WAKE UP!, the writers were keen out an nanoemulsion involving of a micellar solution of fatty acids, such as a polysorbate emulsifier , coconut oil fatty acids, one or more ionic surfactants [6]. The described droplet size was in the range of 5-50 nm. The corporation also described that the nanoemulsion hugely increases asphaltene and paraffin removal efficiency over old-fashioned micro emulsions and it is chemically unreactive formations and is environmentally friendly [28]. The company also described that nanoemulsion releases and eliminates asphaltene, paraffin deposits by allowing a mechanism of structural disjoining pressure from a thin-film of nanoparticles, which expands among the rock formation and the build-up deposits. Micelles in the colloidal form initially dissolve, then capture after then eradicate the hydrocarbon deposited permitting the well to continue production. The enhanced deposits removal effectiveness of the nanoemulsion explains that very little treatment/handling fluid is essential throughout well-remediation as matched to old-fashioned techniques owing to the ratio of high surface area to volume [29].
-
Clay stabilizer and formation fine control addictive
The migration of fines into the formation is an important problem while the production of oil and gas. Fines migration is the movement of particles such as nonclay and clay
particles-carbonates, silica, and quartz within a rock formation cause of drag forces along with other forces created in the course of hydrocarbon flow. The migration of fines into formation because the particles get suspended in the fluid produced to block or act as a barrier in the pore throat radii there by this reduces the productivity of the well. Damage made is usually traced to an area of about 3 5 feet radius.
The reason for fines migration is due to the improper choice of the proppants or unconsolidated rock formation. The introduction of nanoparticles coating on proppants for reducing the fine into the formation are discussed (stefania, 2016) The authors explained the use of nanocrystals (inorganic) to make proppants beads for clay stabilization and fines fixation even though the paper didnt explain the method to prepare composition used. The literature shows that the introduction of nanoparticles decreased the fines migration compared to traditional addictives and extended well productivity was observed.
Table 3- Currently used addictives with the company name and product name [47].
Function with nanomaterial type used |
Product name with company name |
Proppants- Nanocomposites- Polymer with inorganic nanofiller(eg. Carbon black, CNT, alumina, nanoclay) |
Frack-black Frackblackhp Frackblackht (Sun drilling company) |
Nanocomposites-composition not available |
Liteprop108(Baker Hughes incorporated) |
Mixture inorganic shell(eg: fly ash) and core shells-hollow ceramic core |
Ox-frac Ox-ball Ox-thor Ox-steel (Oxane materials) |
Cross-linkers, VES/fluid loss- Nanoparticles-composition not declared (most probably metal-oxide nanoparticle) |
Diamond-fraq (Baker Hughes incorporated) |
Nanoemulsions- composition not declared |
Nanosurf696 (Oil chem technologies) |
Surfactant system- Nanoemulsion- Most possibly made with mixture of water,terpene(solvent) and alcohol ethylates(surfactants) |
Complex nanofluid MA845, Stimgpht, Stimoil®ENX ,EC,FBAM,FBA plusenviro, Stimoil®E50,FD,AHS, MA- 844W, MA845, GPHT (Fiotek industries) |
Nano-dispersion |
NPD solutions (FTS international0 |
Nano-emulsion Most probably made of metal oxides such as sio2 |
G-clean well wakeup (Green earth technologies) |
Formation fines control |
Con-FINE fines control agent (Baker Hughes incorporated) |
Nano particles |
Addictives |
Important function |
Polymer/surfa ctant |
||
Titanium nano- spheres(6- 14nm) |
HPG( hydroxyl propyl guar) |
Titanium complexes are used as fracturing fluid its nanoparticles are active species which crosslink with HPG [32]. |
Sio2 nanoparticles(2 0nm) |
Guar gum, HPG |
Improve viscosity and thermal stability, when the HPG gel cross-linked with nanoborate cross linker. Having a low concentrate of polymer the carrying capacity of proppant increases. At pH. 10 the optimum performance increases [48] |
Sio2 nanoparticles (30nm nano- silica) |
Acrylamide based synthetic copolymer gelling agent |
Concentration of polymer reduced by 25-50% which shows an effective proppants carrying ability and high thermal stability. The presence of nano crosslinker also provides a high viscosity which permits efficacious clean-up. But viscosity shows less increment in increasing nanoparticle size [36]. |
Boronic acid(15 nm-nano-latex) |
Guar gum/DTAB |
Gel viscosity increased when even at low concentration guar gum cross-linked with Nano latex (only 2ppm boron concentration is needed) [35]. |
VES-surfactant |
||
Sio2 nanoparticles (30nm) |
CTAB, nano3 |
Solution viscosity, relaxation time, and the elastic response of material increased when the nanoparticles added to wormlike micelle [41]. |
Zno and mgo nanoparticles(3 0 nm) |
Amid-amine oxide surfactant |
Enhanced shear rate and viscosity of nearly 100 cp is reached when at 275of VES micellar are added in cabr2 and cacl2 [24]. |
Sio2 nanoparticles (7-40 nm) |
CTAB, nasal |
Properties of NEWMS such as viscoelastic and Viscosity increased when nano silica added [20]. |
Insert crystal nanoparticles |
Cause of the pseudo crosslink of the nanoparticles with VES micelles viscosity of VES fluid at 250of is shown 200cp [26]. |
|
Foam fracturing fluid |
||
Sio2 nanoparticles(1 40 nm) |
AOS |
Adding of nanoparticles in AOS mobility of the injected gas reduced with improving stability [22] |
PEC nanoparticles (106.26 nm) |
– |
The Incidence of PEC nanoparticles, the durability of the fracturing fluid increases. The reduction of fluid loss and stability of CO2 foam |
Nano particles |
Addictives |
Important function |
Polymer/surfa ctant |
||
Titanium nano- spheres(6- 14nm) |
HPG( hydroxyl propyl guar) |
Titanium complexes are used as fracturing fluid its nanoparticles are active species which crosslink with HPG [32]. |
Sio2 nanoparticles(2 0nm) |
Guar gum, HPG |
Improve viscosity and thermal stability, when the HPG gel cross-linked with nanoborate cross linker. Having a low concentrate of polymer the carrying capacity of proppant increases. At pH. 10 the optimum performance increases [48] |
Sio2 nanoparticles (30nm nano- silica) |
Acrylamide based synthetic copolymer gelling agent |
Concentration of polymer reduced by 25-50% which shows an effective proppants carrying ability and high thermal stability. The presence of nano crosslinker also provides a high viscosity which permits efficacious clean-up. But viscosity shows less increment in increasing nanoparticle size [36]. |
Boronic acid(15 nm-nano-latex) |
Guar gum/DTAB |
Gel viscosity increased when even at low concentration guar gum cross-linked with Nano latex (only 2ppm boron concentration is needed) [35]. |
VES-surfactant |
||
Sio2 nanoparticles (30nm) |
CTAB, nano3 |
Solution viscosity, relaxation time, and the elastic response of material increased when the nanoparticles added to wormlike micelle [41]. |
Zno and mgo nanoparticles(3 0 nm) |
Amido-amine oxide surfactant |
Enhanced shear rate and viscosity of nearly 100 cp is reached when at 275of VES micellar are added in cabr2 and cacl2 [24]. |
Sio2 nanoparticles (7-40 nm) |
CTAB, nasal |
Properties of NEWMS such as viscoelastic and Viscosity increased when nano silica added [20]. |
Insert crystal nanoparticles |
Cause of the pseudo crosslink of the nanoparticles with VES micelles viscosity of VES fluid at 250of is shown 200cp [26]. |
|
Foam fracturing fluid |
||
Sio2 nanoparticles(1 40 nm) |
AOS |
Adding of nanoparticles in AOS mobility of the injected gas reduced with improving stability [22] |
PEC nanoparticles (106.26 nm) |
– |
The Incidence of PEC nanoparticles, the durability of the fracturing fluid increases. The reduction of fluid loss and stability of CO2 foam |
Table 4:- Important nano-particles enhancing the hydraulic fracturing fluid [47].
becomes high [27]. |
||
Nano-sensors |
||
Nano- magnetite( oleic acid-stabilized) (15 nm) |
In shale gas, Nano-magnetite will be ideal agents in the future and high quantity necessary [39]. |
|
Carbon coated magnetic nanoparticles |
The magnetization of the reservoir due to intensification of the volumetric magnetite susceptibility effectively increases [5]. |
|
Super- paramagnetic nano-sensors |
Helps in the detection of the location and proppants in hydraulic fracture with an increase in magnetic susceptibility [1]. |
CONCLUSION
-
Hydraulic fracturing is now one of the important techniques for the unconventional reservoir. Many countries are facing problem with the oil & gas conventional reservoir, in this hydraulic fracturing technique come up as a booming technique to fill the gap between demand and supply.
-
This paper is reviewed about how nanoparticles enhance the fracking. Nanoparticles when used as hydraulic fracturing fluids their properties change and come up with better applications. With the applications, this paper also gives the details of nanoparticle manufacturing companies with the product name for any research sample.
-
Nanomaterials enhance the additive performance of additives (like- cross-linkers, breaker, viscoelastic surfactant (VES), biocide, etc.), fluid performance, and ability of different proppants to hold the fractures.
-
When nanoparticles are used as proppants it will increase the mechanical properties of the fluids to withstand high compressive strength and high- temperature like-stiffness, compressive strength, stability, etc. A detailed study found about ultralight proppants (nanocomposites) forms from an inorganic substance gives better passage for the hydrocarbon to flow without settling. When CNF is coated on the surface of proppants it gives low density and high surface porosity which decreases the overall density of proppant particle.
-
When nanoparticles are used with Viscoelastic surfactant (VES) it forms a 3-dimensional cross-link structure which results in stabilize the viscosity and improved ability to withstand at a higher temperature which reduces the fluid loss.
-
By using nano-encapsulation, the performance of breakers can be increased. That means the breaker will be having to give long life and more stability compared to traditional liquid breakers.
-
Silver nanoparticle coating on biocide improves the settling properties it will increase the settling time in the mud pit, prevent bacteria deposits, and maintain
concentration and efficiency than the traditional biocides.
-
Nanotechnology applications as surfactants are based on nano-emulsion, nano-additives for emulsions, and nanodispersions. It is chemically unreactive to formations and environmentally friendly. It gives the result by breaking the paraffin and asphaltene which eliminates the build-up on the wall.
-
The use of nanocrystals (inorganic) to make proppants beads for clay stabilization and fines decreased the fines migration into the formation compared to traditional additives and extended well productivity.
REFERENCES
[1]. Aderibigde A.A, Cheng K, Heidari Z, Killough J.E, Fuss T, Stephens W; Detection of propping agents in fractures using magnetic susceptibility measurements enhanced by magnetic nanoparticles https://doi.org/10.2118/170818-MS , 2014. [2]. Al. Muntasheri G.A, Liang F, Hull K.L; Nanoparticles-enhanced hydraulic fracturing fluids https://doi.org/10.2118/185161-PA,2017.
[3]. Alharbi, A., Liang, F., Al-Muntasheri, G.A., Li, L.,. Nanomaterials-enhanced highpressure tolerance of borate- crosslinked guar gels. In: SPE-188817-MS, Abu Dhabi International Petroleum Exhibition & Conference, 13-16 November 2017. Abu Dhabi, UAE,. https://doi.org/10.2118/188817-MS. 2017 [4]. Al-Muntasheri, G.A.,. A critical review of hydrauli fracturing fluids over the last decade. In: SPE-169552-MS SPE Western North American and Rocky Mountain Joint Meeting, 17-18 April,Denver, Colorado, . https://doi.org/10.2118/169552-MS., 2014b [5]. An C, Yan B, Alfi M, Mi L, Killough J.E, Heidari Z; Estimating
spatial distribution of natural fractures by changing NMR T2 relaxation with magnetic nanoparticles; https://doi.org/10.1016/j.petrol.2017.07.030 Journal of Petroleum Science and Engineering:2017.
[6]. Andrecula P. Biodegradable non-reactive oil-well stimulation fluid and method of use, US 8778850 B2, https://patents.google.com/patent/US8778850B2/en.2014 [7]. Barati R, Johnson SJ, McCool S, Green DW, Willhite GP, Liang JT. Fracturing fluid cleanup by controlled release of enzymes from polyelectrolyte complex nanoparticles, https://doi.org/10.1002/app.33343 . 2011. [8]. Barati R, Liang J.t. A review of fracturing fluid systems used for hydraulic fracturing of oil and gas wells, journal of applied polymer science, https://doi.org/10.1002/app.40735 , 2014 [9]. Baruah A., Pathak A.K., Ojha K., Study on rheology and thermal stability of mixed (nonionicanionic) surfactant based fracturing fluids. https://doi.org/10.1002/aic.15175 AIche journal, 2016a [10]. Baruah A., shekhawat D.S., Pathak A.K., Ojha K., Experimental investigation of rheological properties in zwitterionic-anionic mixed-surfactant based fracturing fluids. https://doi.org/10.1016/j.petrol.2016.05.001 Journal of Petroleum Science and Engineering, 2016b. [11]. Bicerano J, Thermoset nanocomposite particles, processing for their production, and their use in oil and natural gas drilling applications, https://patents.google.com/patent/US8278373B2/en.2015
[12]. Bose CC, Fairchild B, Jones T, Gul A, Barati RG. Application of nanoproppants for fracture conductivity improvement by reducing fluid loss and packing of micro-fracture, https://doi.org/10.1016/j.jngse.2015.05.019 .Journal of Natural Gas Science and Engineering.2015. [13]. BP Statistical Review of World Energy, 2020 69th edition https://www.bp.com/content/dam/bp/business- sites/en/global/corporate/pdfs/energy-economics/statistical- review/bp-stats-review-2020-full-report.pdf [14]. Charles fairhurst; Fractures and fracturing: hydraulic fracturing in jointed rock. https://www.intechopen.com/books/effective-and- sustainable-hydraulic-fracturing/fractures-and-fracturing- hydraulic-fracturing-in-jointed-rock [15]. Chauhan G., Ojha K., Baruah A., EFFECTS OF NANOPARTICLES AND SURFACTANT CHARGE GROUPS ON THE PROPERTIES OF VES GEL.https://doi.org/10.1590/0104-6632.20170341s20150094 ,
Brazilian journal of chemical engineering, 2017a
[16]. Chauhan G.,Verma A., Hazarika A., Ojha k., Rheological, structural and morphological studies of Gum Tragacanth and its inorganic SiO2 nanocomposite for fracturing fluid application , https://doi.org/10.1016/j.jtice.2017.08.039 journal of the Taiwan institute of chemical engineers, 2017b [17]. Chauhan Geetanjali, Das Akashdeep, Agarwal Subham and Ojha Keka, Hydraulic Fracturing for Oil and Gas and its Environmental Impacts. http://www.isca.in/rjrs/archive/v4/iISC-2014/1.ISCA- ISC-2014-Oral-8EVS-24.pdf. Research Journal of Recent Sciences. 2015. [18]. Chen F., Yang Y., He J., Bu T., He X., He K., Xiang C., Yu Z.,Wu H., The gelation of hydroxypropyl guar gum by nanoZrO2 https://doi.org/10.1002/pat.4168 polymer advanced technologies, 2018a
[19]. Chen H., Elhag A.S., Chen Y., Noguera J.A., Alsumaiti A.M., Hirasaki G.J., Nguyen Q.P., Biswal S.L., Yang S., Johnston K.P., Oil effect on CO2 foam stabilized by a switchable amine surfactant at high temperature and high salinity https://doi.org/10.1016/j.fuel.2018.04.020 . Fuel, 2018b [20]. Dai C, Zhang Y, Gao M, Li Y, Lv W, Wang X, Wu Y, Zhao M; The study of novel nanoparticles-enhanced wormlike micellar system. https://pubs.acs.org/doi/10.1021/acs.biomac.6b01545 Nanoscales Res. Lett. 12,431:2017. [21]. Dai C, Zhang Y, Gao M, Li Y, Sun Y, Zhao M; The first study of surface modified silica nanoparticles in pressure-decreasing application; https://pubs.rsc.org/en/content/articlelanding/2015/RA/C5RA098 83A#!divAbstract RSC Adv 5, 61838-61845: 2015. [22]. Emrani A.S, Ibrahim A.F, Nasr-El-Din H.A; Mobility control using nanoparticle-stabilized CO2 foam as a hydraulic fracturing fluid; https://doi.org/10.2118/185863-MS Journal of Petroleum Science and Engineering:2017. [23]. Guerfi, A., Sevigny, S., Lagace, M., Hovington, P., Kinoshita, K., Zaghib, K., 2003. Nanoparticle Li4Ti5O12 spinel as electrode for electrochemical generators https://doi.org/10.1016/S0378- 7753(03)00131-9 e. J. Power Sources 119, 8894, 2003 [24]. Gurluk M.R, Nasr-El-Din H.A, Crews J.B; Enhancing the performance of viscoeleastic surfactant fluids using nanoparticles; https://doi.org/10.2118/164900-MS SPE-164900: 2013. [25]. Haung T, Crews J.B, Agarwal G; Nanoparticles pseudo-cross- linked micellar fluid: optimal solution for fluid-loss control with internal breaking; Journal of Petroleum Science and Engineering; https://doi.org/10.2118/128067-MS 2010. [26]. Haung T, Crews J.B; Nanotechnology application in viscoeleastic surfactant stimulation fluids: Journal of Petroleum Science and Engineering; https://doi.org/10.2118/115384-MS 2008. [27]. Hosseini H, Tsau J, Peitier E, Barati R; lowering fresh water usage in hydraulic fracturing by stabilizing scCO2 foam with polyelectrolyte complex nanoparticles prepared in high salinity produced water,https://doi.org/10.2118/189555MS.Howard,G.C.,Fast,C.,1957.Op timumFluidCharacteristicsforFractureExtension.DrillingandProdu ctionPractice :2018.
[28]. http://www.getg.com/G-CLEAN_well_stimulation.php [29]. https://www.accesswire.com/viewarticle.aspx?id=417987 [30]. Huang T, Clark DE. Advanced fluid technologies for tight gas reservoir stimulation. Conference paper for presentation at SPE Saudi Arabia Section Technical Symposium and Exhibition https://doi.org/10.2118/160844-MS .2012. [31]. Huang T. Breaking viscoelastic surfactant gelled fluids using breaker nanoparticles, US 8778852 B2, https://patents.google.com/patent/US8778852B2/en .2014 [32]. Hurnaus T, Plank J; cross linking of guar and HPG based fracturing fluids using ZrO2 nanoparticles; https://doi.org/10.2118/173778-MS Journal of Petroleum Science and Engineering: 2015. [33]. Jiangtao Zheng, Yang ju,Hui-Hai Liu, Liange Zheng ,Moran Wang: Numerical prediction of the decline of the shale gas productions rate with considering the geomechanical effects based on the two-part Hookes model; https://doi.org/10.1016/j.fuel.2016.07.112 fuel 185( 2016) 362-369; 2016.
[34]. Khair E.M.M., Shicheng Z., Shanbo M.,Mei Z., Performance and application of new anionic D3F-AS05 viscoelastic fracturing fluid https://doi.org/10.1016/j.petrol.2011.05.011 Journal of Petroleum Science and Engineering, 2011 [35]. Lafitte v, Tustin G.J, Drochon b, Parris M.D; Nanomaterials in fracturing applications; https://doi.org/10.2118/155533-MS Journal of Petroleum Science and Engineering: 2012. [36]. Liang F, Al-Muntasheri G, Ow H cox J; reduced polymer loading high temperature fracturing fluids by use of nano-cross-linkers; https://doi.org/10.2118/177469-PA SPE J. 22, 622-631:2017. [37]. Luca Gandossi: An overview of hydraulic fracturing and other formation stimulation technologies for shale gas production: http://dx.doi.org/10.2790/99937 .JRC technical reports EUR 26347 EN; 2013. [38]. Madhan Nur Agista, Kun Guo and Zhixin Yu:A state of the art review of nanoparticles application in petroleum with a focus on Enhanced oil recovery; https://doi.org/10.3390/app8060871.2018.
[39]. Morrow L, potter D.K, Barron A.R; Detection of magnetic nanoparticles against proppant and shale reservoir rocks: https://doi.org/10.1080/17458080.2014.951412 J.Exp. Nanosci 10, 1028-1041: 2015. [40]. Nath, F., Xiao, C.,. Characterizing foam-based frac fluid using carreau rheological model to investigate the facture propagation and proppant transport in eagle ford shale formation. In: SPE- 187527-MS, SPE Eastern Regional Meeting, Lexington, 4-6 October 2017, Kentucky, USA, . https://doi.org/10.2118/187527-MS 2017
[41]. Nettesheim F, Liberation M.W,Hodgdon T K, Wagner N.J, Kaler E.W, Vethamuthu M; Influence of nanoparticles addition on the properties of wormlike micellar solutions; https://pubs.acs.org/doi/10.1021/la800271m Langmuir 24, 7718-7726: 2008.
[42]. Nurudeen yekeen, Eswaran Padmanabhan,Ahmad Kamal Idris, Prithvi singh Chauhan: nanoparticles applications for hydraulic fracturing of unconventional reservoirs: A comprehensive review of recent advances and prospects: https://doi.org/10.1016/j.petrol.2019.02.067 journal of petroleum science and engineering 178(2019) 41-73;2019. [43]. Peter James Boul,Pulickel M. Ajayan. Nanotechnology Research and Development in Upstream Oil and Gas. https://doi.org/10.1002/ente.201901216 .Energy Technology 2019 [44]. R.L. Root: Factors affecting the design of hydraulic fracturing treatments. https://www.onepetro.org/conference-paper/ARMA- 78-0008 [45]. Rickman RD, Jaripatke OA. Optimizing micro- emulsion/surfactant packages for shale and tight gas reservoirs, 2010. Conference paper for presentation at SPE Deep Gas Conference and Exhibition, Manama, Bahrain, https://doi.org/10.2118/131107-MS 24-26 January 2010 [46]. Rytter E. Porous proppants, https://patents.google.com/patent/WO2015067555A2/un , 2015 [47]. Stefania Gottardo et.al. Use of nanomaterials in fluids, proppants, and downhole tools for hydraulic fracturing of unconventional hydrocarbon reservoirs,https://core.ac.uk/download/pdf/81685116.pdf JRC EUROPEAN COMMISION 2016
[48]. Wang K,Wang Y, Ren J, Dai C; Highly efficient nano boron crosslinker for low-polymer loading fracturing fluid system. https://doi.org/10.2118/186943-MS In: SPE/IATMI Asia Pacific Oil and Gas conference and Exhibition, Jakarta, Indonesia,pp. 1- 11: 2017. [49]. Woodrow R, McCubbins JR. Nanoparticle biocide in industrial application, US 20140148367 A1, https://patents.google.com/patent/US20120015852A1/pt 2014 [50]. Wu H.,Zhou Q., Xu D.,Sun R., Zhang,. Bai B,.Kang W,; SiO2 nanoparticle-assisted low-concentration viscoelastic cationic surfactant fracturing fluid. https://doi.org/10.1016/j.molliq.2018.06.107, journal of molecular liquids, 2018a [51]. Xiang zhang, J.G. Wang, Feng gao, Yang ju, Jia liu: Impact of water and nitrogen fracturing fluids on fracturing initiation pressure and flow pattern in anisotropic shale reservoirs: https://doi.org/10.1016/j.compgeo.2016.07.011 computers and geotectonics 81(2017) 59-76 [52]. Xiao wei Weng;Modelling of complex hydraulic fractures in naturally fractured formation Journal of Unconventional Oil and Gas Resources. https://doi.org/10.1016/j.juogr.2014.07.001 .2015 [53]. Xiao, C., Balasubramanian, S.N., Clapp, L.W., . Rheology of supercritical CO 2 foam stabilized by nanoparticles. In: SPE- 179621-MS,SPE Improved Oil Recovery Conference, 11- 13April, 2016, Tulsa, Oklahoma, USA, . https://doi.org/10.1021/ acs.iecr.7b01404 2016. [54]. Yan Z., Dai C., Zhao M., Sun Y., Zhao G., Development, formation mechanism and performance evaluation of a reusable viscoelastic surfactant fracturing fluid https://doi.org/10.1016/j.jiec.2016.03.012 journal of Industrial and engineering chemistry, 2016. [55]. Zhao M., Zhang Y., Zou C., Dai C., Gao M., Li y., Lv W., Jiang J., Wu Y., Can More Nanoparticles Induce Larger Viscosities of Nanoparticle-Enhanced Wormlike Micellar System (NEWMS). https://doi.org/10.3390/ma10091096 2017a