
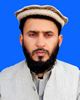
- Open Access
- Authors : Noorullah Zahid
- Paper ID : IJERTV11IS120075
- Volume & Issue : Volume 11, Issue 12 (December 2022)
- Published (First Online): 22-12-2022
- ISSN (Online) : 2278-0181
- Publisher Name : IJERT
- License:
This work is licensed under a Creative Commons Attribution 4.0 International License
A Review of Effect of Nano-Materials on Durability of Concrete
Noorullah Zahid
Dept. Civil Engineering, Shaikh Zayed University Khost Town, Afghanistan.
Abstract:- Nano-material are the ultrafine material with materials size at the nanometer level, which are used in concrete to obtain some good properties especially increasing the durability. During this study, the effect of nano-materials (such as Nano silica (SiO2), nano alumina (Al2O3), carbon nano tube, polycarboxylates, nano titania (TiO2), nano-ferric oxide (Fe2O3), nano clay, nano kaolin, carbon nanotubes) on the durability property of concrete is reviewed. Because of the nano-filler effect and the pozzolanic reaction of nano-materials, the microstructure became more homogeneous and less porous. The microstructure of concrete with nano-materials is denser and more uniform than that of conventional concrete. The channels for harmful agents through the cement composites were partially filled and blocked. Due to this action the nano- materials reduce porosity, increase the density of cement concrete, and thus show an improvement in resistance to permeability and water absorption than conventional concrete, and the frost resistance of concrete is also enhanced. The incorporation of nanomaterials in concrete enhances durability to sulfate attack. Therefore the durability of nano-concrete is increased with the relevancy of the control mixes.
Keywords: Nano-oncrete; durability; Nano-material; Nano- materials; Nanotechnology.
-
INTRODUCTION
Concrete is one of the foremost used building materials in the world because of its some better properties. But due to containing some small pores, aggressive materials infiltrate to the concrete, especially in the sever environment and reduce the durability of the concrete. So, the improving the durability property of cement concrete are very important and this is mostly corresponding to the nano-scale properties of concrete or to the nanotechnology of concrete. Recently the final word goal of concrete nanotechnology is that the studying of concrete at the nano-scale and also the studying of nano- materials accustomed give better properties to concrete. Nanomaterial refers to the ultrafine material with materials size at the nanometer level (1-100nm), which is larger than the atomic cluster (the cluster of atoms but 1nm in length) and smaller than the usual powder, within the transition zone of the cluster to the macroscopic object, a typical mesoscopic system [49]. Because of its small size, large area, and other factors, have subsequent four special effects: size effect, quantum effect, surface effect, and interface effect. These four effects mainly reflect the structural, chemical, and physical characteristics of nano-materials [71]. Nano-mineral powder mainly includes nano-silica, nano-calcium carbonate, and nano-silica powder. In ordinary hydraulic cement within the distribution of 10-100nmgel pores, the incorporation of nano- powder just fills these gaps and plays a job in improving the permeability of concrete [14]. The nano-cementing materials
increase the crack resistance, decrease within the curing time, increase in ductility, and also increase the strength. [62]. Nano-SiO2, TiO2, Al2O3, Fe2O3 was used as nano-filler in the cement matrix, the capillary pores were found to be smaller and the total porosity was also decreased [9, 20, 23, 30, 35, 36,
39, 40, 52, 59, 67, 75, 77]. With the use of the nano-materials the cement paste become dense and the dense cement paste will positively affect the durability properties of cement concrete [35].
The objective of this study is to review the durability properties of nano-concret. Due to use of nano-materials in concrete mixes the microstructure became more homogeneous and less porous. Thus concrete with nano-materials is denser and more uniform than that of conventional concrete. Nano- materials reduce water permeability, sorptivity, chloride migration, and infiltration of harmful agents and diffusivity of concrete and improves the resistance to freezing and thawing and increase the crack resistance and density. Hence, the durability performances of concrete become enhanced with nano-materials.
-
NANO CONCRETE
Nano concrete is a concrete that utilises nano materials or a concrete with nano materials added in which the size of the nano particles is less than 500 nm [37, 44, 55, 57, 58, 61, 70]. It was believed that the addition of nano particles in concrete improve the strength of conventional concrete. Nano particle works in concrete by improving the bulk properties or also known as packing model structure. Ultrafine or nano particles can perform a superb filler effect by refining the intersectional zone in cement and producing more density concrete. By acting as good filler, their manipulation or alteration in the cement matrix system occurs to provide a new nano-scale structure. Common discrepancies in concrete microstructure such as micro void, porosity and deterioration due to alkali silica reaction will be eliminated. Next, nano materials start to evolve when they become new binding agent which is smaller than cement particles. This improves the structure of hydration gel providing a neat and solid hydration structure. In addition, through the combination of filler and additional chemical reaction in hydration system, a new concrete called nano concrete with durable and enhanced performance has been developed [2, 4, 65].
Implementation of nano technology in concrete has started since the early millennium in line with the increasing demand for UHPC. Conventional mix formulations of UHPC with the inclusion of silica fumes provide better durability and strength. However, due to limited availability and also the high cost of silica fume makes UHPC technology declining and less demanding compared to HSC. Since then, emerging
technology in nano production has developed an alternative to silica fume. [60]. Due to the breakthrough of nano silica, many nano based particles has been developed to be used in concrete. Nano alumina [11], titanium oxide [43], carbon nano tube [47] and polycarboxylates [24] are examples of nano materials used in nano concrete.
-
EFFECT OF NANOMATERIALS ON DURABILITY OF CONCRETE
In the following will discuss the application of different nanomaterials such as nanosilica, carbon nanotubes (CNTs), ferric oxide, and nano-titanium oxide in concrete industries. It can be noted that majority of nano-based concrete products are still at the laboratory-scale level, and only a few products, such as nanosilica particles and polycarboxylate nano- products, have been commercialized and are used by the industry. Nanoparticle-incorporated concrete is also known as nanoconcrete, and more commercialization is required.
-
Nano silica
Nanosilica is a nanomaterial commonly used in the concrete application, and has characteristics such as smaller particle sizes, good dispersion, high chemical purity, large surface energy, stronger surface adsorption, and large specific surface area [78]. The nanosilica reacts with lime at the time of the cement hydrating procedure as well as subsequently generating a CSH gel, which might enhance the mechanical properties and durability of the concrete. In some of the research works, it was observed that nanosilica utilization in concrete enhanced the particle packing [16]. The cement hydration rate also was improved, which efficiently improved the strength, and lowered the dormant period and time of setting. This nanomaterial also decreased the concrete porosity and prevented the possibility of the degradaton of concrete [63]. Studies by Qing, Zenan [72], showed that concrete with addition of nano silica improved workability of concrete while the addition of superplasticizers is at a minimum dosage. The reason behind the workability improvement is the round shape of nano silica which provides a ball bearing manoeuvre in cement particles.
Size of nano silica which in nano particles acts as ultra- filler in concrete. Micro voids in concrete will be densified and refined to provide neat concrete microstructure [13, 21]. Other advantages of nano silica are the water to cement ratio can be controlled and targeted strength can be modified easily with controlled dosage. Another report by Quercia. G, Hüsken. G [19] revealed that the addition of nano silica at certain dosage just not improved strength of HSC but also acted as cement replacement material. About 20%30% of cement content can be reduced by nano silica. Thus, nano silica can be an alternative material to cement. However, the price of nano silica is high and it is available in certain countries. Some countries have to import nano silica to be used in concrete industry [33]. The incorporation of nanomaterials in concrete enhances durability to sulfate attack. The improvement of 10% nano silica replacement in the resistance to sulfate attack is better than that of 0% nano silica [68]. Ji studied the water permeability of concrete containing nano-silica and found that the microstructure of concrete containing nano-silica is more uniform and compact, leading to reduction in water permeability [30].
-
Nano alumina
The addition of nano alumina in concrete can hugely affect concrete properties as it controls the setting time of cement. The function of nano alumina in cement is to speed up the initial setting time for concrete. This will reduce segregation and flocculation. Disruption in cement will create non homogeneity in concrete mixes, and hence the performance of concrete will be affected. Nano alumina in concrete acts as dispersion agent in cement particles [7, 27, 54, 66]. Furthermore, since the size is in nano form, nano alumina also refines the voids in the hydration gel as nano filler. Since cement content in existing concrete proportion is high, dispersion of cement grains in concrete must take place concurrently with silica action in the hydration process. Without nano alumina refining of hydration product, the hydration process will be slower because the internal structure of hydration gel cannot be penetrated by silica component. By adding nano alumina, the path will be created and silica or binding materials will be easily injected into the microstructure of hydration gel and the refining process will start [25, 27, 37].
-
Carbon nano tube (CNT)
Carbon nanotubes (CNTs) are also commonly used for concrete application, and the tensile strength of CNT is almost 100 times higher than that of steel with a similar diameter. CNTs also have a higher thermal conductivity, similar to that of diamond crystal [8]. Carbon nanotubes are added to concrete as a nanofiller because they possess a higher surface area and unusual mechanical characteristics. Mohsen et al. [50] examined the influence of carbon nanotube utilization on the microstructure, permeability, strain capacity, and flexural strength of concrete. The test results confirmed this nanomaterial increased the concrete beam ductility by approximately 150%. A qualitative microstructural analysis showed the CNT filaments uniform dispersion inside the concrete hydration products in entire batches. The study confirmed that a large void content was occurring due to the increased surfactant content present in the solution after the sonication process. Gürkan et al. [74] demonstrated that relative to carbon nanotubes, carbon fiber utilization remarkably enhanced the load-carrying capability and ductility, leading to bending mode of failure even with inadequate shear reinforcement. Nanotubes are members of the fullerene structural family. Their name is derived from their long, hollow structure with the walls formed by one- atom-thick sheets of carbon, called graphene. These sheets are rolled at specific and discrete angles, and the combination of the rolling angle and radius decides the nanotube properties [47]. The chemical bonding of nanotubes is composed similar to those of graphite. These bonds, which are stronger than the bonds found in alkanes and diamond, provide nanotubes with their unique strength.
The advantage of using CNT in concrete is its flexibility. From this, the design of concrete can be altered into either unique or rigid design. Flexibility provided by CNT also increases the strength of concrete. As compared to other nano materials, CNT is the best nano material in terms of improving flexibility and enhancing strength of concrete [47]. Most of all, volume and size of CNT are smaller as compared to other nano materials. The main reaction of CNT in
concrete is to improve the tension and compression abilities [73].
Steel reinforcement section can be replaced by CNT which permits extra loads to be handled. By replacing steel in concrete, it was believed that more lightweight and less reinforcement sections can be created. In addition, time and the cost of construction can be reduced. However, lack of CNT sources and being extremely pricy reduces the interest of having CNT in concrete.
-
Polycarboxylates
Normally, polycarboxylate is applied in concrete as high range water reducer. The addition of polycarboxylate will help to control the workability of concrete at low water to cement ratio. The properties of polycarboxylate in concrete depend on the dosage of polycarboxylate. Too high dosage will result in false set or no hydration occurrence in concrete [64]. Apart from that, inclusion of polycarboxylate at required dosage will produce Self Compacting Concrete (SCC). SCC increases the workability of concrete and produces a flow concrete which gives great impact during the placing of concrete at low and high intensity area. Another advantage of having polycarboxylate in concrete is its ability to be used in marine structure. Since polycarboxylate has the ability to remove air bubble in improving density of concrete, pores or voids in concrete will be reduced to provide a compact structure. In addition, refining of concrete microstructure will prevent or reduce the rate of permeability when dealing with marine condition. From that, the attacks of sea water such as sulphate and chloride content can be controlled or reduced. Besides, the use of polycarboxylate is considered as a greener technique compared to silica fume and any additives in refining microstructure of concrete. Sobolev (2005) reported that utilisation of polycarboxylate in concrete enhances workability and performance compared to that of silica fume. Furthermore, almost 70% of depending material in concrete such as silica fume, superplasticizers and fibers can be reduced [4, 10]. Finally, the study showed that polycarboxylate in concrete enhances the strength performance as compared to those of plain concrete. Crainic (2002) reported that polycarboxylate inclusion at around 2.5% of cement weight rapidly increases strength of concrete at early age. It was reported that at day one, the strength of concrete can go from 40 to 80 MPa. At 28 days, strength can be achieved at around 70100 MPa easily at lower dosage of polycarboxylate. This proves that polycarboxylate can be an alternative admixture to enhance the strength of concrete. Typically, polycarboxylates will be applied in concrete as a high-range water reducer, and this incorporation helps to control the workability of the concrete at a lower water-to cement-ratio [51]. Due to its easy handling characteristics with minimum guideline or technique required, makes polycarboxylate one of the most popular nano materials to be adopted in concrete.
-
Titanium oxide
Addition of TiO2 in concrete and concrete has proven a great effect on self-cleaning ability and contribute to the aplication of green material in construction [56]. Self- cleaning effect of TiO2 has been utilised in buildings, paving material and the finish product can be seen on the construction of Jubilee Church in Rome Italy [18]. Another
benefit of TiO2 is accelerating strength of concrete at early age. Furthermore, performance of concrete also improves and abrasion resistance in concrete increases [17]. Basically, those effects are provided by TiO2 in concrete due to TiO2 has ability to act as glass layer or pigment outside the concrete particles and also in the microstructure of concrete. Those layers react to the hydration gel during mixing and act as protective layer that gives self-cleaning ability to the concrete surface. The self-cleaning effect provided by TiO2 surrounds the outer surface concrete and coats concrete surface which is hard and permeable. For enhancement in performance, TiO2 in concrete forms a fiber reinforced system which can be seen mimicking the glass fiber effect. Refining and tailoring the hydration gel by acting as fiber contribute to the strength enhancement and more durable concrete [26]. The larger effective surface of TiO2 nanoparticles helps to absorb a large quantity of water, leading to a reduction in the concretes workability [31].
However, issues on safety and health were among the problems arised in TiO2. Although there is no report on the pollution but particles of TiO2 which are dusty and small create the environmental effect to factory workers during packing and production. It was believed that titanium creates inflammatory effect and dangerously causing cancer to factory workers [17]. Therefore, care during handling must be taken seriously which includes mixing process of TiO2.
-
Ferric Oxide
The optimum incorporation of ferric oxide (Fe2O3) nanoparticles in concrete specimens might increase the compressive strength. Kani et al. [34] studied the properties of cement composites and mortars in the presence of ferric oxide nanoparticles as the modifier. The cement composite was synthesized by the sol-gel technique with the complex ligand tetraethylammonium orthosilicate. Ferric oxide nanoparticles were incorporated at 2.0, 4.0, and 6.0 wt % concentrations in the cement composite; whereas for mortars, 2.0, 3.0, and 4.0 wt % of ferric oxide nanoparticle concentrations were employed. The test results confirmed a variation in the molecular structure and phase composition of the cement composites, resulting in stronger bonds in the silicate network, with an extremely ordered arrangement of nanomaterials in them. The mechanical properties of mortar samples increased with inclusion of ferric oxide nanoparticles, and a 3.0 wt%dosage was recognized as the optimal concentration.
A study by Heikal et al. [22] examined the influence of ferric oxide nanoparticles on the properties and durability resistance to chloride and sulfate anion attacks. Ferric oxide nanoparticles were manufactured from the heating of Fe(CH3COO)2OH at 450 _C and 300 _C at a 2 h soaking time. The manufactured ferric oxide nanoparticles demonstrated the buildup of fine ferrihydrite and hematite crystals with an almost 1020 nm grain size.
Ferric oxide nanoparticles increased the durability of composite pastes containing ferric oxide nanoparticles toward chloride and sulfate anion attacks. Mixes with 0.51.0% ferric oxide nanoparticles confirmed low values of total chloride and total sulfate contents. This was due to a finer and denser matrix with low porosity, which blocked the empty pores to the diffusion of chloride and sulfate anions, and
therefore demonstrated increased values of bulk density and compressive strength. Thus, overall, it was noted that the addition of ferric oxide nanoparticles to the concrete could improve its mechanical properties, such as its compressive strength. Further, the hardened concretes water absorption could also be improved with the inclusion of iron powder. Moreover, it was observed that the ferric oxide nanoparticles could increase the durability resistance of concrete against chloride, as well as sulfate anion attacks.
In a previous study [69] showed a significant improve- ment in the mechanical properties and durability performance using the nano-particles as an admixture. The study showed that 3 wt% of nano-Fe3O4 in the cementitious materials was the optimal amount to improve both its mechanical and microstructural properties. It concluded that, the replacement of cement by iron powder improved the compressive strength and porosity but decreased the slump flow [38].
-
Nano kaolin
Nano kaolin is a by-product of kaolin. Kaolin or its chemical name, kaolinite is a clay mineral, part of the industrial minerals, with the chemical composition Al2 Si2 O5 (OH)4. It is a layered silicate mineral, with one tetrahedral sheet linked through oxygen atoms to one octahedral sheet of alumina octahedral [6, 76]. Rocks that are rich in kaolinite are known as kaolin or china clay [5].
Kaolinite contains white mineral that is also known as dioctahedral phyllosilicate clay. It is formed from clay which is produced by chemical weathering of aluminium silicate minerals such as feld- spar [1, 76]. The chemical formula for kaolinite as used in mineralogy is Al2 Si2 O5 (OH)4. However, in ceramic applications, the formula is typically written in terms of oxides, which after being treated by heat treatment change into Al2O3_2SiO2_2H2O. Furthermore, kaolin after treatment or endothermic dehydration will change from crystal to amorphous stage [53]. The transformation will change it into new formation of clay called metakaolin. Metakaolin consists of amorphous silica and alumina, and the structure is in long order or hexagonal layers [5, 12]. Metakaolin has been known as very reactive pozzolan and performs similar reaction to silica fume. Strength enhancement and improved durability by refining microstructure, allowing reliable water penetration and making cost effective are the stronger points in metakaolin as compared to silica fume [15, 28, 29, 42].
Nano kaolin is formed using either top to down or bottom to up approach. Those processes will influence the final formation of nano kaolin. Generally, the basic but major formation of nano kaolin involves layering or stacking flakes. At a glance, the particle of kaolin is similar to nano kaolin. Morphological properties of kaolin after the transformation in size from micro to nano is its particles provide larger surface area. In concrete, nano kaolin must undergo treatment in order to form a more reactive or stable component; nano metakaolin. Nano metakaolin is still newly used as supplementary in concrete, but the enhancement in concrete properties is expected, due to the positive impact of metakaolin in UHPC and other types of concrete. In a report by Morsy et al. [46], nano metakaolin addition in concrete has improved the strength of mortar where almost 8%10% increment of compressive strength can be achieved. The most
interesting finding is, tensile and flexural enhancement of mortar containing nano metakaolin is around10%15% as compared to plain OPC [45, 46].
-
Nano clay
Nano clay is nanoparticles of layered mineral silicates. Depending on the chemical composition and nanoparticle morphology, nanoclays are organised into several classes such as montmorillonite, bentonite, kaolinite, hectorite, and halloysite. Nanoclay is one of the most affordable materials that have shown promising results in polymers. Nanoclay is made of montmorillonite mineral deposits known to have platelet structure with average dimension of 1 nm thick and 70150 nm wide. The unique structure of montmorillonite clay is it possesses several qualities that make it an excellent base for manipulation through nanotechnology. These qualities include stability, an interlayer space, high hydration and swelling capacity and a high chemical reactivity [21, 32, 48].
Clays can be considered as inexpensive materials. Having nano materials from clay based can be adaptable ith adequate cost. Despite the occurrence of clay in most parts of the world, guideline and techniques to imply and form clay to nano materials is still unrevealed. Research on the advantages and disadvantages of nano clay as construction materials need to be explored. Nano clay has been widely used in polymeric system. However, the evidence on improvement and enhancement in material stiffness, thermal stability, as barrier coating, solvents and other improvement especially in electronic and new form of materials are needed. Normally in construction, nano clay is applied as an additive to enhance concrete properties. Morsy et al. [46] reported that, enhancement in compressive and tensile strength for mortar cement having nano clay as additive was recorded. Thermal behavior of concrete also improved after nano clay was added as cement additive in paste [3, 41].
-
-
CONCLUSION
In this study, the effect of nano-materials on durability of concrete is discussed, and the following conclusions were drawn:
-
Nanomaterials are used as nano-filler in the cement concrete matrix, the capillary pores were found to be smaller and the total porosity was also decreased and the cement paste become dense and the dense cement paste positively affect the durability properties of cement concrete.
-
Nano silica (SiO2) is the most commonly used nanomaterials in a cement matrix, but there are others nano-materials which are also used in concrete mixtures such as nano alumina (Al2O3), carbon nano tube, polycarboxylates, nano titania (TiO2), nano- ferric oxide (Fe2O3), nano clay, nano kaolin, carbon nanotubes.
-
The nano-materials improve the strength of concrete. There is a strong correlation between concretes splitting tensile strength and compressive strength. The splitting tensile strength tends to increase along with the increase of concretes compressive strength.
-
Because of the nano-filler effect and the pozzolanic reaction of nano-materials, the microstructure of
concrete became more homogeneous and less porous. Thus, the addition of each nano-material to concrete improves its durability at an extent.
-
The microstructure of concrete with nano-material is denser and more uniform than that of conventional concrete. The channels for harmful agents through the cement composites were partially filled and blocked. Due to this action the nano-materials reduce porosity, increase the density of cement concrete, and thus show an improvement in resistance to permeability and water absorption than conventional concrete, and the frost resistance of concrete is also enhanced.
-
The incorporation of nanomaterials in concrete enhances durability to sulfate attack.
-
Nano-materials increase the resistance to sulfate attack, reducing the permeability of concrete mixtures against chloride ions; improve the resistance against freezing and thawing; reduce the loss of compressive strength. Consequently, they are capable of improving the durability of concrete.
-
The various types of nano-materials impose different effects on the shrinkage property and carbonation depth of concrete mixture; the microstructure of different types of concrete is significantly enhanced upon the addition of nano-materials.
REFERENCES
[1] A. Chakchouk et al., Formulation of blended cement: effect of process variables on clay pozzolanic activity, Constr. Build. Mater. 23 (3) (2009) 13651373. [2] A.B. Aref Sadeghi Nik, Nano-particles in concrete and cement mixtures, Appl. Mech. Mater. 110116 (2012) 38533855. [3] A.E. Al-Salami, H. Shoukry, M.S. Morsy, Thermo-mechanical characteristics of blended white cement pastes containing ultrafine nano clays, Int. J. Green Nanotechnol.: Biomed. 4 (4) (2012) 516527. [4] A.K.M. Bjorn Birgisson, Georgene Geary, Mohammad Khan, Konstantin Sobolev, Nanotechnology in Concrete Materials, 2012, Transportation Research Circular E-C170, ISSN 097-8515. [5] B.B. Sabir, S. Wild, J. Bai, Metakaolin and calcined clays as pozzolans for concrete: a review, Cem. Concr. Compos. 23 (6) (2001) 441454. [6] B.N. Rolfe, R.F. Miller, I.S. McQueen, Dispersion characteristics of Montmorillonite, Kaolinite and Illite clays in water of varying quality and their control with phosphate dispersants, in: Geological Survey Professional Paper 334-G cooperation Colorado State University, (USA), 1960. [7] B.-W. Jo et al., Characteristics of cement mortar with nano-SiO2 particles, Constr. Build. Mater. 21 (6) (2007) 13511355. [8] Che, J.; Cagin, T.; Goddard,W.A., III. Thermal conductivity of carbon nanotubes. Nanotechnology 2000, 11, 65. [9] Chen J, Kou SC, Poon CS. Hydration and properties of nano- TiO2 blended cement composites. Cem Concr Compos 2012;34:6429. [10] Constructor. Smart nano materials in construction industry, 2014. [11] D. Adak, M. Sarkar, S. Mandal, Effect of nano-silica on strength and durability of fly ash based geopolymer mortar, Constr. Build.Mater. 70 (2014) 453459.
[12] D. Zhang et al., Synthesis of clay minerals, Appl. Clay Sci. 50 (1) (2010) 111. [13] D.A. Jon Belkowitz, An investigation of nano silica (SiO2) in the cement hydration process, in: Concrete Sustainability Conference 2010, National Ready Mixed Concrete Association. [14] Du H, Gao H, Pang SD. Use of 2-D nano-particles to enhance the concrete resistance to chloride ingress. In: XIII International conference on durability of building materials and components, Sao Paulo, Brazil; 2014. p. 94653. [15] E. Ghafari, H. Costa, E. Júlio, Critical review on eco-efficient ultra high performance concrete enhanced with nano-materials, Constr. Build. Mater. (2015) 201208. [16] Elrahman, M.A.; Chung, S.-Y.; Sikora, P.; Rucinska, T.; Stephan,D. Influence of nanosilica on mechanical properties, sorptivity,and microstructure of lightweight concrete. Materials 2019, 12, 3078.
[17] F. Pacheco-Torgal, S. Jalali, Nanotechnology: advantages and drawbacks in the field of construction and building materials, Constr. Build. Mater. 25 (2) (2011) 582590. [18] F. Sanchez, K. Sobolev, Nanotechnology in concrete a review, Constr. Build. Mater. 24 (11) (2010) 20602071. [19] G. Quercia, G. Hüsken, H.J.H. Brouwers, Water demand of amorphous nano silica and its impact on the workability of cement paste, Cem. Concr. Res. 42 (2012) 344357. [20] Gaitero JJ, Campillo I, Guerrero A. Reduction of the calcium leaching rate of cement paste by addition of silica nanoparticles. Cem Concr Res 2008;38:11128. [21] H. Lindgreen et al., Microstructure engineering of Portland cement pastes and mortars through addition of ultrafine layer silicates, Cem. Concr. Compos. 30 (8) (2008) 686699. [22] Heikal, M.; Zaki, M.E.; Ibrahim, S.M. Characterization, hydration, durability of nano-Fe2O3-composite cements subjected to sulphates and chlorides media. Constr. Build. Mater. 2021, 269, 121310. [23] Hou PK, Kawashima S, Wang KJ, Corr DJ, Qian JS, Shah SP. Effects of colloidal nanosilica on rheological and mechanical properties of fly ashcement mortar. Cem Concr Compos 2013;35:1222. [24] I. Navarro-Blasco et al., Assessment of the interaction of polycarboxylate superplasticizers in hydrated lime pastes modified with nanosilica or metakaolin as pozzolanic reactives, Constr. Build. Mater. 73 (2014) 112. [25] I.G. Richardson, The nature of CSH in hardened cements, Cem.Concr. Res. 29 (8) (1999) 11311147.
[26] J. Chen, C.S. Poon, Photocatalytic construction and building materials: from fundamental to application, Build. Environ. 44 (9) (2009) 18991906. [27] J. Rosenqvist, Surface Chemistry of Al and Si (Hydr)Oxides, With Emphasis on Nano-Sized Gibbsite (-Al(OH)3), Department of Chemistry, Inorganic Chemistry, Umeå University, Umeå, Sweden, 2002. [28] J.A. Kostuch, G.V. Walters, T.R. Jones, High Performance Concrete Incorporating Metakaolin A Review. Concrete 2000,<>University of Dundee, 1993, 17991811
[29] J.M. Khatib, B.B. Sabir, S. Wild, Pore size distribution of metakaolin paste, Cem. Concr. Res. 26 (10) (1996) 15451553. [30] Ji T. Preliminary study on the water permeability and microstructure of concrete incorporating Nano-Sio2. Cem Concr Res 2005;35-43. [31] Joshaghani, A.; Balapour, M.; Mashhadian, M.; Ozbakkaloglu, T. Effects of nano-TiO2, nano-Al2O3, and nano-Fe2O3 on rheology, mechanical and durability properties of self-consolidating concrete (SCC): An experimental study. Constr. Build. Mater. 2020, 245,118444. [32] K. Patel, The use of nanoclay as a constructional material, Int. J. Eng. Res. Appl. 2 (4) (2012) 13821386. [33] K.A. Ganesan, Strength and water absorption properties of ternary blended cement mortar using rice husk ash and metakaolin, Scholar. J. Eng. Res. 1 (4) (2012) 5159. [34] Kani, E.N.; Rafiean, A.H.; Alishah, A.; Astani, S.H.; Ghaffar, S.H. The effects of Nano-Fe2O3 on the mechanical, physical and microstructure of cementitious composites. Constr. Build. Mater. 2021, 266, 121137. [35] Kawashima S, Hou P, Corr DJ, Shah SP. Modification of cement- based materials with nanoparticles. Cem Concr Compos 2013;36:815. [36] Kong D, Du X, Wei S, Zhang H, Yang Y, Shah SP. Influence of nano-silica agglomeration on microstructure and properties of the hardened cementbased materials. Constr Build Mater 2012;37:70715. [37] L. Hui et al., Microstructure of cement mortar with nano- particles, Compos. Part B: Eng. 35 (2) (2004) 185189. [38] Largeau, M.A., Mutuku, R. and Thuo, J. (2018) Effect of Iron Powder (Fe2O3) on Strength,Workability, and Porosity of theBinary Blended Concrete. Open Journal of Civil Engineer-ing, 8, 411-425.
[39] Li G. Properties of high-volume fly ash concrete incorporating nano-SiO2. Cem Concr Res 2004;34:10439. [40] Li H, Xiao H, Yuan J, Ou J. Microstructure of cement mortar with nano-particles. Compos B: Eng 2004;35:1859. [41] M. Heikal et al., Behavior of composite cement pastes containing silica nano-particles at elevated temperature, Constr. Build. Mater. 70 (2014) 339350. [42] M.A. Caldarone, K.A. Gruber, R.G. Burg, High reactivity metakaolin: a new generation of mineral admixture, Concr. Int. (1994) 3740. [43] M.A. Massa et al., Synthesis of new antibacterial composite coating for titanium based on highly ordered nanoporous silica and silver nanoparticles, Mater. Sci. Eng. C 45 (2014) 146153. [44] M.O. Remzi Sahin, New materials for concrete technology: nano powders, in: 33rd Conference on Our World in Concrete & Structures: 2527 August 2008, Singapore, 2008. [45] M.S. Morsy et al., Behavior of blended cement mortars containing nano-metakaolin at elevated temperatures, Constr. Build. Mater. 35 (2012) 900905. [46] M.S. Morsy, S.A. Alsayed, M. Aqel, Effect of nano-clay on mechanical properties and microstructures of ordinary Portland cement mortar, Int. J. Civ. Environ. Eng. 10 (01) (2010). [47] M.S. Morsy, S.H. Alsayed, M. Aqel, Hybrid effect of carbon nanotube and nanoclay on physico-mechanical properties of cement mortar, Constr. Build. Mater. 25 (1) (2011) 145149. [48] M.Z.a.R.S.C. Smart, Nanomorphology of kaolinites: comparative SEM and AFM studies, Clays Clay Min. 26 (2) (1998) 153160. [49] Mei Zhang. The research status and development of nanometer materials [J]. Journal of missile and space launch technology. 2000 (3). [50] Mohsen, M.O.; Al Ansari, M.S.; Taha, R.; Al Nuaimi, N.; Taqa,A.A. Carbon nanotube effect on the ductility, flexural strength, and permeability of concrete. J. Nanomater. 2019, 2019, 111.
[51] Norhasri, M.M.; Hamidah, M.S.; Fadzil, A.M. Applications of using nano material in concrete: A review. Constr. Build. Mater. 2017, 133, 9197. [52] Oltulu M, Sahin R. Pore structure analysis of hardened cement mortars containing silica fume and different nano-powders. Constr Build Mater 2014;53:65864. [53] P. Blanchart, S. Deniel, N. Tessier-Doyen, Clay structural transformations during firing, Adv. Sci. Technol. 68 (2010) (2010)3137.
[54] P. Hosseini et al., Effect of nano-particles and aminosilane interaction on the performances of cement-based composites: an experimental study, Constr. Build. Mater. 66 (2014) 113124. [55] P. Hou et al., Effects of the pozzolanic reactivity of nanoSiO2 on cement-based materials, Cem. Concr. Compos. 55 (2015) 250258.
[56] P. Maravelaki-Kalaitzaki et al., Physico-chemical and mechanical characterization of hydraulic mortars containing nano-titania for restoration applications, Cem. Concr. Compos. 36 (2013) 3341. [57] P.B.a.K. Chong, Nanotechnology and concrete: research opportunities, in: Proceedings of ACI Session on Nanotechnology of Concrete: Recent Developments and Future Perspectives November 7, 2006, Denver, USA2006. [58] P.C. Aïtcin, Cements of yesterday and today: concrete of tomorrow, Cem. Concr. Res. 30 (9) (2000) 13491359. [59] Quercia G, Spiesz P, Husken G, Brouwers HJH. SCC modification by use of amorphous nano-silica. Cem Concr Compos 2014;45:6981. [60] R. Yu, P. Spiesz, H.J.H. Brouwers, Effect of nano-silica on the hydration and microstructure development of Ultra-High Performance Concrete (UHPC) with a low binder amount, Constr. Build. Mater. 65 (2014) 140150. [61] R.J.M. Pellenq, N. Lequeux, H. van Damme, Engineering the bonding scheme in CSH: the iono-covalent framework, Cem. Concr. Res. 38 (2) (2008) 159174. [62] Rashad, A. M. A synopsis about the effect of nano-Al 2 O 3, nano-Fe 2 O 3, nano-Fe 3 O 4, and nano clay on some properties of cementitious materialsa short guide for Civil Engineer. Materials & Design, 2013, 52,143- [63] Rollins, A.B.; Collet, P.E.P.; Andres, V. Concrete Porosity Reduction by Colloidal Silica Nano Technology, Part 2: One YearResults from Djeno Wharf. Available online: https://www.pci.org/PCI_Docs/Papers/2018/10001_Final_Paper.p df (accessed on 9 October 2021).
[64] S. Helmy, S.V. Hoa, Tensile fatigue behavior of tapered glass fiber reinforced epoxy composites containing nanoclay, Compos.Sci. Technol. 102 (2014) 1019
[65] S. Zhao, W. Sun, Nano-mechanical behavior of a green ultra-high performance concrete, Constr. Build. Mater. 63 (2014) 150160. [66] S.R. Ali Nazari, Improvement compressive strength of concrete in different curing media by Al2O3 nanoparticles, Mater. Sci. Eng. A 528 (2010) 11831191. [67] Said AM, Zeidan MS, Bassuoni MT, Tian Y. Properties of concrete incorporating nano-silica. Constr Build Mater 2012;36:83844. [68] Saloma et al. Improvement of concrete durability by nanomaterials, Science Direct, Elsevier, Procedia Engineering ( 2015 ) pp. 608 612 [69] Sikora, P., Horszczaruk, E., Cendrowski, K. and Mijowska, E. (2016) The Influence of Nano-Fe3O4 on the Microstructure and Mechanical Properties of Cementitious Composites. Nanoscale Research Letters, 11, 182. [70] V.M. Maholtra, P.K. Mehta, Pozzolanic and Cementitious Materials, Taylor & Francis, 1996. [71] Wei L., Linkai X., Xiaochu W., and Yi R., A Review of Mechanical Properties and Durability of Nano-concrete, Advances in Engineering Research, Volume 136, (7th ICADME) 2017, pp. 5-8. [72] Y. Qing et al., Influence of nano-SiO2 addition on properties of hardened cement paste as compared with silica fume, Constr. Build. Mater. 21 (3) (2007) 539545. [73] Y. Rostamiyan et al., Using response surface methodology for modeling and optimizing tensile and impact strength properties of fiber orientated quaternary hybrid nano composite, Compos. Part B: Eng. 69 (2015) 304316. [74] Yldrm, G.; Sarwary, M.H.; Al-Dahawi, A.; Öztürk, O.; Anl, Ö.;¸Sahmaran, M. Piezoresistive behavior of CF- and CNT-based reinforced concrete beams subjected to static flexural loading: Shear failure investigation. Constr. Build. Mater. 2018, 168, 266 279.
[75] Yu R, Spiesz P, Brouwers HJH. Effect of nano-silica on the hydation and microstructure development of ultra-high performance concrete (UHPC) with a low binder amount. Constr Build Mater 2014;65:14050. [76] Z. Adamis, Bentonite, Kaolin and Selected Clay Minerals, G. World Health Organization (WHO), Editor, 2005. [77] Zhang M, Li H. Pore structure and chloride permeability of concrete containing nano-particles for pavement. Constr Build Mater 2011;25:60816. [78] Zhuang, C.; Chen, Y. The effect of nano-SiO2 on concrete properties: A review. Nanotechnol. Rev. 2019, 8, 562572.