
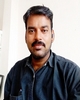
- Open Access
- Authors : Dr. B. Sudarshan , U. Pradeep Kumar , R. Mahesh
- Paper ID : IJERTV10IS070085
- Volume & Issue : Volume 10, Issue 07 (July 2021)
- Published (First Online): 14-07-2021
- ISSN (Online) : 2278-0181
- Publisher Name : IJERT
- License:
This work is licensed under a Creative Commons Attribution 4.0 International License
A Review: an Optimization of the Fused Deposition Modeling (FDM) Process Parameters in Rapid Prototyping Technology (RPT)
1 Dr. B. Sudarshan 2U. Pradeep Kumar 3 R. Mahesh
1. Associate professor, Department of Mechanical engineering,
2 & 3. Assistant Professor, Department of mechanical engineering
K.S.R.M. College of engineering (Autonomous), Kadapa, Andhra padesh-516003
Abstract:- Rapid prototyping (RP) is a type of technology that can create physical models from computer-aided design (CAD) data automatically. Fused deposition modeling is a rapid prototyping technique that involves laying a track of semi-molten plastic filament on a platform in a layer-by-layer fashion from bottom to top. The mechanical properties of parts fabricated using fused deposition modeling (FD) are highly dependent on various process variables such as layer thickness (A), air gap (B), raster width (C), contour width (D), and raster orientation (E) on the mechanical properties such as tensile, flexural, impact strength, and hardness. To collect the test runs for this investigation, a thorough Taguchi experiment was used. To investigate the influence of the variable FDM process parameter settings, a number of analytical approaches such as Analysis of Variance (ANOVA) were applied. As a result, optimizing FDM process parameters is required in order to increase component quality. The goal of this research is to look at the reviews of several optimization approaches for optimizing process parameters in the FDM process.
Keywords: Optimization, Taguchi Approach Fused Deposition Modeling (FDM), and Analysis of Variance (AN0VA).
-
INTRODUCTION:
Reduced product development cycle time is a major concern in industries that want to stay competitive in the marketplace, hence the focus has turned away from traditional product development methodologies and toward quick manufacturing processes such as rapid prototyping (RP). The RP method can create parts with any difficult geometry in the shortest amount of time possible without incurring additional costs owing to the lack of tooling. Fused deposition modeling is an RP technique that involves layer-by-layer deposition of extrusion material to construct real items directly from a CAD model. However, the quality of FDM-produced parts is greatly dependent on the process parameters employed. As a result, FDM parameters must be optimized. The optimization of process parameters aids in the discovery of proper parameter adjustments that improve prototype quality. Because it may simplify experimental plans and reduce the number of experimental runs, the Taguchi approach is the most extensively utilized for experiment design.
-
FORMULATION OF THE PROBLEM
To please the buyer, the product's quality and price are the most critical factors. However, as previously stated, the
quality of FDM-produced parts is greatly dependent on numerous process parameters. As a result, it is important to carry out FDM parameter optimization. The quality of working parts will be improved. There are a plethora of optimization, design of experiments, and prediction approaches available. It's tough to say which is superior without a quick review. This paper aids in determining which strategy is ideal for a certain application, and we will choose the best method to accomplish our aim.
-
LITERATURE REVIEW
Several investigations on FDM build part depositing parameters are presented in this publication. For a range of parametric structures (solid, shell, orthogonal, hexagonal, pyramid), build orientations, and internal densities, material usage, build time, and loading characteristics are captured (loose, compact). Based on this information, a model is created that can I estimate mechanical properties and (ii) compute build time and materials based on different internal structural configurations for the component's application. It is necessary to create a model that creates an optimal solution (minimal material, minimum build time, etc.).[L. Villalpando et al., 2014] There may be times when the two most common FDM production processes (solid and shell) aren't appropriate. Internal structures that provide a balance of material utilisation and strength can open up new possibilities. However, this adds to the production strategy's complexity, and comprehensive physical testing to evaluate mechanical behaviors is time-consuming and costly. Virtual experimentation addresses these issues, and it is demonstrated in this study that the FEA simulation accurately simulates the real experiments done on compressive materials.
S. Dinesh Kumar et al.(2014), The findings of the experimental study on the cause of the key FDM process variable parameters, namely layer thickness (A), air gap (B), raster width (C), contour width (D), and raster orientation (E), are explained in this paper (E). In this study, pieces were constructed using the innovative ABS- M30i biomedical material. Taguchi's design of trials with two levels for each element was used in the experiments.
In this study, five FDM parameters were investigated at two variable settings for building test parts: (A) layer thickness, (B) air gap, (C) raster width, (D) contour width,
and (E) raster orientation, which resulted in a reduction in building time and improved surface finish.
Sandeep Raut et al. (2014), the purpose of this research article was to look at the impact of built-up orientation on the mechanical qualities and total cost of FDM parts. Experiments were conducted using a STRATASYS FDM rapid prototyping machine and CATALYST software, utilizing ABS as the primary material. Tensile and flexural specimens were made according to ASTM standards, with three geometrical axes and distinct built-up orientations. The impact of constructed orientation on the mechanical qualities and total cost of FDM parts was explored in this study.
Mechanical properties of FDM-produced items, such as tensile and bending strength, are investigated in this work. In calculating the total cost of FDM parts, the influence of the main material used, the support material required, the number of layers, and the build time are all taken into account. As a result, the work implicitly includes the minimization of major and support materials. The slicing method is also used to determine the best build orientation. For different construction orientations, the build time and number of layers necessary are calculated. Based on the findings, it can be inferred that FDM parts built up around the y-axis at a 0 angle have good tensile strength and low cost. FDM items with an x-axis 0 angle built up orientation have good flexural strength and a moderate cost. This is an excellent conclusion that will assist Rapid Prototyping users in determining the ideal construction orientation for their parts and creating optimal process planning.
Anoop Kumar Sood et al. (2010), Anoop Kumar et al. investigated the impact of key process parameters including as layer thickness, part orientation, raster angle, air gap, and raster width, as well as their interactions, on the dimensional accuracy of fused deposition modeling (FDM) ABS parts. They discovered that shrinkage, as well as the length and width directions of manufactured elements are dominant. However, in the thickness direction, there is a positive departure from the required value. Taguchi's parameter design was used to find the best parameter settings to minimize the percentage change in length, width, and thickness of a standard test specimen. They employed an artificial neural network (ANN) to make predictions.
Finally, they conclude that higher layer thickness (0.254 mm), 0 orientation, maximum raster angle (60), medium raster width, and 0.004 air gap will produce desired results for reducing % change in length. Lower values of layer thickness (0.127mm), orientation (0), raster angle (0), and raster width (0.004), on the other hand, will decrease the percentage change in thickness of the test specimen. They used the grey Taguchi approach to construct the part in such a way that all three dimensions are as close to the actual value as possible. Finally, maximising of the grey relational grade reveals that the layer thickness is 0.178 mm, the part orientation is 0 degrees, and the layer thickness is 0.178 mm. With a raster angle of 0 degrees, a road width of 0.4564 mm, and an air gap of 0.008 mm, the overall dimensions of the part will improve.
R. Anitha et al. (2001) did an experiment and discovered numerous intriguing elements of the FDM process in their findings. At a 95 percent level of significance, only the layer thickness is effective to 49.37 percent. However, after pooling, it was discovered that the layer thickness is effective to 51.57 percent at a level of significance of 99 percent. At a 99 percent level of significance, the two parameters, road width and speed, contribute 15.57 and
15.83 percent, respectively. The correlation study emphasizes the importance of layer thickness even more. This suggests that surface roughness has a strong inverse relationship. The layer thickness is most effective when it is at level, according to the S/N study. When the layer thickness is 0.3556mm, the road width is 0.537mm, and the deposition speed is 200mm, the layer thickness is most effective.
B.H. Lee et al.(2005), They optimized the effect of parameters on the creation of flexible ABS objects in an FDM machine, and produced ABS compliant prototypes as a result. To explore the process parameter in order to produce optimum elastic performance of compliant ABS prototype to gain maximum throw distance from prototype, an orthogonal array, S/N ratio, and ANOVA are used. For the study, four parameters were chosen: air gap, raster angle, raster width, and layer thickness, each at three levels. The L9 orthogonal array was chosen for the design of experiments, and after the experimental work, the optimum combination of parameters for 10, 15, and 20 degrees of displacement was determined.
-
FINAL THOUGHTS
The conclusion gained from the above reviews is that optimizing FDM parameters is required to achieve higher quality parts. For experimental design, the Taguchi method is the best option. Its tools, like as orthogonal arrays, S/N ratios, and ANOVA analysis, are useful in identifying the most important factors that influence performance characteristics.
REFERENCES
-
L. Villalpando, H. Eiliat, R. J. Urbanic, An optimization approach for components built by fused deposition modeling with parametric internal structures, Product Services Systems and Value Creation. Proceedings of the 6th CIRP Conference on Industrial, Product- Service Systems, 800-805 (2014).
-
S. Dinesh Kumar, V. Nirmal Kannan and G. Sankaranarayanan,
Parameter Optimization of ABS-M30i Parts Produced by Fused Deposition Modeling for Minimum Surface Roughness, International Journal of Current Engineering and Technology (April 2014)
-
Sandeep Raut,VijayKumar S. Jatti, Nitin K. Khedkar, T.P.Singh,
Investigation of the effect of built orientation on mechanical properties and total cost of FDM parts, 3rd International Conference on Materials Processing and Characterization (ICMPC),1625-1630 (2014)
-
Anoop Kumar Sood, R.K. Ohdar, S.S. Mahapatra, Parametric appraisal of mechanical property of fused deposition modeling processed parts, journal of Materials and Design from Elsevier, 287-295 (2010)
-
R. Anitha, S. Arunachalam, P. Radhakrishnan, Critical parameters influencing the quality of prototypes in fused modeling, journal of materials processing technology, 385-388 (2001)
-
B.H. Lee, J. Abdullah, Z.A. Khan, Optimization of rapid prototyping parameters for production of flexible ABS object, Journal of Materials Processing Technology 169, 54-61 (2005)