
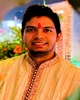
- Open Access
- Authors : Ashutosh Kumar , Swati Sachdev , Ali Mehdi , Adarsh Sharma, Abhishek Anand, Brijesh Chaurasiya
- Paper ID : IJERTV10IS020160
- Volume & Issue : Volume 10, Issue 02 (February 2021)
- Published (First Online): 25-02-2021
- ISSN (Online) : 2278-0181
- Publisher Name : IJERT
- License:
This work is licensed under a Creative Commons Attribution 4.0 International License
A Comparative Study of Electromagnetic Braking System
1
Ashutosh Kumar
B.Tech Scholar(ME) BBDNITM-054
2
Swati Sachdev
Assistant Professor (ME) BBDNITM-054
3
Ali Mehdi
B.Tech Scholar (ME) BBDNITM-054
4
Adarsh Sharma
B.Tech Scholar (ME) BBDNITM-054
5
Abhishek Anand
B.Tech Scholar (ME) BBDNITM-054
6
Brijesh Chaurasiya
-
ech Scholar (ME) BBDNITM-054
Abstract – This paper describes a new and efficient energy utilization on braking System for stoping the vehicles and presents a new methodology for evaluation of the reliability of the hybrid- magnetic Retardation system using Electromagnetism approach and Lenz Law. A new idea to use the existing EM based braking force of the vehicles and offers a stable, inflation proof, economical, reliable and new & renewable energy based braking of which there is proven and available technologies. Appropriately designed and implemented EM based braking system can save power wasted during the braking of the normal vehicle and it can provide a system which meets the need of Electric world energy of anticipated forseeable future for many years of the 21st century. Combined electric power and magnetic system is a non-depleting, non-polluting and non- depending energy source that can provide reliable and economical efficacy as a most promising new and renewable energy source of the 21st century. The heat potential of waste Energy from Retardation flowing through Disk system has been determined to produce a flow duration curve (FDC) by ordering the recorded heat flows from maximum to minimum flow. The generating capacity of the system depends on the force rate of the Magnetic Disk connected to existing braking system of the vehicle. The probability of difference in maximum and minimum force rate between winter and summer is small and this will not affect the heat output produced by heat disk of the vehicle. Several factors as design pressure, the roughness of the pipes interior surface, method of joining, weight and ease of installation, accessibility to the market, design life and maintenance, weather conditions, availability of material, related cost and likelihood of structural damage have been considered for a particular penstock of the EM braking system. The selection criteria of the Disk has been explained according to design flow, type of vehicle and desired running speed of the vehicle. A hybrid system such as micro regeneration power and photo voltaic system has been proposed to provide reliable electric energy to Banaras Hindu University, Varanasi (India).
-
INTRODUCTION
Brake A.
A vehicle brake is used to slow down a vehicle by converting its kinetic energy into heat. Most commonly brakes use friction between two surfaces pressed together to convert the kinetic energy of the moving object into heat, though other methods of energy conversion may be employed. For example regenerative braking converts much of the energy to electrical energy, which may be stored for later use. Other methods
convert kinetic energy into potential energy in such stored forms as pressurized air or pressurized oil. Eddy current brakes use magnetic fields to convert kinetic energy into electric current in the brake disc, fin, or rail, which is converted into heat. Still other braking methods even transform kinetic energy into different forms, for example by transferring the energy to a rotating flywheel.
Types of Brake
-
Friction Brake
-
Electromagnetic Brake
Friction Brake B.
-
A friction brake is a type of automotive brake that slows or stops a vehicle by converting kinetic energy into heat energy, via friction. The heat energy is then dissipated into the atmosphere. In most systems, the brake acts on the vehicle's wheel hubs, but some vehicles use brakes which act on the axles or transmission.
Friction brakes may be –
1) Drum Type. 2) Disc Type.
Drum Brake C.
A drum brake is a vehicle brake in which the friction is caused by a set of brake shoes that press against the inner surface of a rotating drum. The drum is connected to the rotating roadwheel hub
Disc Brake D.
The disc brake is a device for slowing or stopping the rotation of a road wheel. A brake disc (or rotor in U.S. English), usually made of cast iron or ceramic, is connected to the wheel or the axle. To stop the wheel, friction material in the form of brake pads (mounted in a device called a brake caliper) is forced mechanically, hydraulically, pneumatically or electromagnetically against both sides of the disc. Friction causes the disc and attached wheel to slow or stop.
Electromagnetic Brake: E.
-
Electromagnetic brakes slow an object through electromagnetic induction, which creates resistance and in turn either heat or electricity. Friction brakes apply pressure
on two separate objects to slow the vehicle in a controlled manner.
-
In locomotives, a mechanical linkage transmits torque to an electromagnetic braking component.
-
Trams and trains use electromagnetic track brakes where the braking element is pressed by magnetic force to the rail. They are distinguished from mechanical track brakes, where the braking element is mechanically pressed on the rail.
-
Electric motors in industrial and robotic applications also employ electromagnetic brakes.
-
Recent design innovations have led to the application of electromagnetic brakes to aircraft applications. In this application, a combination motor/generator is used first as a motor to spin the tires up to speed prior to touchdown, thus reducing wear on the tires, and then as a generator to provide regenerative braking.
2 LITERATURE REVIEW
Stephen Z. Oldakowski, Bedford, Ohio A magnetic brake provides braking or locking capability and is remotely controlled by electric power. The magnetic brake comprises a rotatable shaft and a brake disc mounted on the shaft. A non- rotating core housing assembly located around the shaft includes a permanent magnet and a bipolar solenoid. A magnetic armature adjacent to the core housing assembly is capable of movement toward the core housing assembly and toward and into engagement with a brake disc to prevent rotation of the shaft. A spring urges the armature away from the core housing assembly and into engagement with the brake disc. The brake does not use any electric power to maintain the brake in the set mode with the rotating shaft fully locked or in the released mode with the rotating shaft fully released. The permanent magnet is of sufficient strength to hold the armature against urging of the spring until an opposite polarity is supplied by the solenoid.
Karl Erny, Holzhausem An elevator drive has a brake device with compression springs to actuate brake levers, and brake linings on a brake drum creating a braking force. A sensor is provided to detect the movement of a brake magnet armature tappet. A bracket is attached to the brake magnet tappet on one end and a distance piece carrying the sensor housing is arranged on the other end. A restoring lug is attached to the existing mechanical indicator. A monitor evaluates the sensor signal and turns off the elevator drive in the event of dangerous operational states via a safety circuit. The system allows the state of the brake device to be monitored. The more the brake linings wear off due to abrasion, the smaller the distance between the armature and the brake magnet housing. If the armature is in contact with the brake magnet housing, the braking ability of te brake linings is completely void.
Hung-Chi Wu, 958-2, Ghung Shan Rd., Tao-Yuan, Taiwan This invention relates to an adjustable magnetic brake and in particular to one including an aluminum fan, a magnetic conducting ring enclosing the aluminum fan, a permanent magnet disposed within the aluminum fan, a fixing seat for keeping the permanent magnet in position, a sliding seat mounted in the fixing seat and provided with a bearing, a housing, bolts provided on one side of the fixing seat and extending out of the housing, a mounting plate connected with the bolts and a wire connected with the mounting plate such
that when the wire is pulled outwards, the permanent magnet will be moved outwards.
Jae-Woong Lee, Seoul, Rep. of Korea Disclosed is a magnetic brake system for a vehicle. comprising: a plurality of brake disk solenoids for generating the magnetic force; a plurality of brake pad solenoids for generating the magnetic force; a braking sensor for detecting whether a brake pedal is applied; a wheel speed sensor for detecting wheel speed; a magnetic polarity sensor for detecting magnetic polarity of the brake disk solenoids; and a control unit for controlling the brake pad solenoids using signals from the braking sensor. The wheel speed sensor and the magnetic polarity sensor. Albert E. Miller, Dayton, Ohio This invention relates to a fishing reel and more particularly to an improved type of reel having a compensated magnetic brake means for preventing backlash or overrunning of the spool. An object of this invention is to provide a reel which is inexpensive to manufacture and which is durable and trouble-free in operation. Still another object of this invention is to provide an improved form of magnetic brake having spring means for modifying the brake action. A further object of this invention is to provide a fishing reel which is smooth in operation and which is readily adjustable to desired degrees of drag or braking effect. Further objects and advantages of the present invention reside in the construction and combination of parts and in the mode of operation as will be apparent from the following description, reference being had to the accompanying drawings wherein a preferred form of the present invention is clearly shown.
-
WORKING
-
Working Principle
-
If a piece of copper wire was wound, around the nail and then connected to a battery, it would create an electro magnet. The magnetic field that is generated in the wire, from the current, is known as the right hand thumb rule.
-
Whenever the current carrying conductor cuts the magnetic field, the e.m.f (Electromagnetic force) is induced.
-
The electromagnetic braking system is based on the creation of eddy currents within a metal disc rotating between two electromagnets which set up a force opposing the rotation of the disc.
-
If the electromagnet is not energized, the rotation of the disc is free and accelerates uniformly under the action of the weight to which its shaft is connected. When the electromagnet is energized, the rotation of the disc is retarded and the energy absorbed appears as heating of the disc.
Fig 1.1
3.3 Wheel: The wheel is a circular component that rotates on an axle bearing where it is one of the key component of the braking system with a radius of 90cm.
Fig 1.2
-
-
Working Of The Model and Component Used
The model works with the principle of electromagnetic field where the wheel is made to run at a speed with the help of a motor or manually, when the wheel is at a certain speed or rpm the power provided to it is released and the wheel is on the free movement it is then the brakes are applied where the two electromagnets are mounted close the disc and an air gap is maintained between the disc and the electromagnet of 0.5mm. The electromagnets gets engaged only when there is a supply of DC power to it, but before that the model is been automated with a regulator, relay and a RF channel controller. Where the regulator generates a fixed output voltage from the supply and to regulate one or more voltages, whereas the relays are the switches that opens and closes the circuit by electrically or electromechanically and they control the circuit by opening and closing contacts in another circuit. The RF channel is the device used to switching on and off of the application by means of a remote controller where by transmitting the signal to the relay and the operation is performed accordingly.
The automated set up is connected to the power supply where then the circuit is connected to the electromagnets so that the automation can be done easily. When the wheel is rotating at a certain revolutions for a period of time the wheel is made to retard or stop with the help of the electromagnets by the help of the electromagnetic field, where the setup is operated by controlling the RF channel remote control where the rotating wheel can be stopped by controlling the RF controller where the controller transmits the signal to the relay where the relay is then activates the circuit and then it directly activates the electromagnets where the electromagnets tends to stop the wheel by applying the force to the disk and hence the wheel is made to stop in fraction of seconds and the controller is disengaged where then the automated setup disengages the electromagnets and then the wheel and the disk connected to it is left free. Thus the amount of retardation in the wheel is made to slow down or stop in an efficient way
The electromagnetic braking system is one kind of a technological revolution where the prototype model of it shows a closer look to its design where the model consists of
-
Wheel
-
Disk
-
Electromagnets
-
Frame
-
Automated circuit
-
Battery
-
Disk: One of the main key component in the braking system is the disk where it is attached to the wheel and transfers the retardation force to the wheel as well. The disk is the component where it receives retardation force and produces opposing torque force which is having a diameter of 26cm.
-
Electromagnet: Since the name itself says Electromagnetic braking system and the main component required is the electromagnet, whereas the e.m.f. rule states that the metal is completely winded and it is been enclosed so that it can be ready to use anytime. When the current is passed the coils inside are excited and the magnetic field is produced from the electromagnet. The electromagnets works in the base of induction. Where the process induction causes electrical field to produce magnetic field thus the electromagnet uses the source of power from the electrical field into the magnetic field. The strength of the magnetic field from the magnet is a static property of the electromagnet. Hence the electromagnets works by a source of power which a magnet naturally produces.
-
Automated circuit: The automated circuit board is one important component in the system where it connects the mechanical components electrically to perform the action. Where the circuit consists of
-
-
Regulator
-
Relay
-
RF channel
-
7805 Regulator: Regulator is a device that controls and regulates the voltage and the power supplied to the circuit value. 7805 regulator is a member of 78xx series of fixed linear voltage regulators which is used to maintain such fluctuations and it is a popular voltage regulator integrated circuit.
-
-
Fig: 1.3
-
Relay: Relays are the switches that open and close the circuit by electrically or electromechanically, they control the circuit by engaging and disengaging and even the contacts between another circuit. The Relay Contact is closed and the AC Mains circuit gets a closed path and the Bulb glows. Thus a Relay is DC operated but controls AC. The electro- mechanical relay is an output device (actator) which comes in a different shapes, sizes and designs, and they have many uses and applications in electronic circuits. But when the electrical relays can be used for low power electronic or computer type circuits to switch relatively high currents or voltages both
ON or OFF some form of relay switch circuit is required to control it.
-
RF channel controller: The RF channel is a device which is used to switching ON and OFF of the system. Where the RF controller is a small electronic device used to transmit and receive radio signals between two devices. RF controllers are usually subject to regulatory uses just like the controlling the actuation.
-
Frame: The frame is the structural system which supports components of the physical construction such as the axel, wheel, clamps connecting the electromagnet and the automated circuit board holder. Vertical steel columns and horizontal beams, constructed in a rectangular grid that even balances the vibrations which is occurred by the movement of the wheel and even the ability to handle the stopping force of the wheel by the electromagnets.
-
Battery: Battery is a device that converts chemical energy directly to electrical energy where it is used to power up the whole system especially to the circuits. It consists of a number of voltaic cells; each voltaic cell consists of two half cells connected in series by a conductive electrolyte containing anions and cations.
-
METHODOLOGY
To fabricate the model it all begins with a systematic plan where the fabrication is of a seven steps of solving process. The steps are as follows:
-
ANALYSING THE RESEARCH PAPERS:
Collect all the relevant data about the problems and the research programs which are happening around and the outcomes of them and evaluate them by comparing with the other research programs where to sort out the demerits of the conventional types of braking systems in a more effective.
-
SELECTION OF THE ELECTROMAGNETIC BRAKES TO OVERCOME THE PROBLEMS:
Selection of the electromagnetic braking system is to minimize the problems which normally occur in the conventional type of braking system where to overcome some problems like efficiency, maintaining parameters, safety. Hence to overcome these problems the electromagnetic braking system is been selected for the further process.
-
ANALYSIS OF THE ELECTROMAGNETIC BRAKING SYSTEM:
To study and analyze about the system where by focusing on to the working principle and the fabrication materials and design required for the model to be done and even a study towards the functioning of the braking system according to the design planned.
-
PREPERATION OF DESIGN:
In this step it is more concentrated on to the design part where looking on to several alternatives of designs according to the installation specifications as planned in the previous steps.
-
FABRICATION:
In this step the process consist of working on to the chosen design and approach into the reality. The model is then fabricated as per the specifications given and check if all the mechanisms work perfectly.
-
TESTING:
The model is tested to check if it meets all the objectives and the model is again made to test weather there has to be done any improvement or any modifications to it. After the test is done completely the model is then made to implement.
RESULT AND DISCUSSION
-
Area of the Electromagnet = 12.4 m
-
Current & Voltage supplied (I/V) = 7amp/230volts.
-
Length of electromagnet (L) =90 mm.
Let the plate & wheel assembly maximum weight is to be consider approx. 2kg. which is 19.62N so that will be
F is the force in Newton.
B is the magnetic field in teslas.
A is the area of the pole faces in square meters. is the permeability of free space.
In case of free space (air)
=4.10-7 H.m-1 19.62 = B2 (12.4)
2×4.x10
B=0.00199wb/m2
-
TOTAL MAGNETIC FLUX IN CORE: Ø = B ×A
Ø = 0.00199×12.4 Ø
= 0.0246 wb.
-
THE MAGNETIZING FORCE: H = B/µ = 0.00199/4×10^-7
= 1583.59 AT/m.
For air gap of 0.5 mm magnetic force is given by between magnet & plate.
AT = H×L = 1583.59×90×10^-3 = 142.52 AT
To find the power of electromagnet which is manually constructed
Assuming N = number of turns in the electromagnetic = 800 F= (NxI) 2 µa / (2xg)
g = air gap between electromagnet & plate F= (8×1) 2 4×10 -7 x0.00199 /(2×0.5) 2
F= 16.045N for each electromagnet
TABLE .1 LIST OF ELECTROMAGNETS ACCORDING TO THEIR SIZE AND POWER
NUMBER SIZE(mm) RATED POWER(W) ADHESIVE FORCE(N)
-
-
RESULT:
Hence the deacceleration of the electromagnetic braking system by using manual method takes place according to the braking time.
4340105
25
25
100
7
600
6. APPLICATIONS
4340110
35
40
100
9
850
4340120
35
40
150
11
1650
application of locomotives where the set up was a drum brake
4342125
35
40
200
13
2300
which is totally different from the present designs and works
4343135
35
40
300
19
4000
on the same principle and it is well used in the present high
4344145
50
60
400
28
8400
speed electric trains.
4345155
35
40
500
40
6000
4346165
35
40
600
46
6600
4347175
35
40
700
54
7700
in automobiles it is even used in the industrial fields where to
retard or slow down the moving parts which is not efficiently
-
Electromagnetic brakes were before used in the
-
The electromagnetic braking system is not only used
If the model is driven by the motor then the calculation will be as follows
Assuming,
Single phase AC motor. Power = 12v/5A=60 watt Speed= 0-8600 rpm (variable).
Motor
Torque P = 2 N T/ 60
T = 60 x 60/ 2 x 8600 T = 0.066 N-m
PERFORMANCE TESTING
rpm r= radius of wheel V= r
= 0.9×2n/60
=0.9×2×2000/60 V= 188.4 m/s
According to newtons law of motion V= u+at
a= (v- u)/t
where the initial velocity of thw wheel u=188.4 m/s and final velocity v=0
therefore a= (0-188.4)/1 = -188.4 m/s^2 a= (0-188.4)/3 = -62.8 m/s^2
4.4. PERFORMANCE TESTING OF THE MODEL WHEN POWERED BY A MANUAL
For constant speed at taking 200 rpm r= radius of
wheel V= r
= 0.9×2n/60
=0.9×2×200/60
V= 18.8 m/s
According to newtons law of motion V= u + at
a= (v-u)/t
where the initial velocity of thw wheel u=188.4 m/s and final velocity v=0
therefore a= (0-18.8)/1 = -18.8 m/s^2 a=(0-18.8)/3 = -6.2 m/s^2
performed by the other conventional methods.
-
Now a days these types of braking systems are used in the field of motorsports where it is more responsive and effective and it is been used in cars like Mclaren P1, La Ferrari
-
Where he electromagnetic brakes are even used as clutches in other fields where they have a high holding power to the other components which will be easier to transfer the work.
-
The electromagnetic braking system is even used in the industrial robotic applications where the requirement of pausing the actions.
-
-
-
This type of braking system is even used in the recreational purposes where an example of the climbing devices where the rope gets locked at a particular height with the help of the electromagnetic braking inside.
-
CONCLUSIONS
-
-
Electromagnetic braking system is found to be more reliable as compared to other braking systems. In oil braking system or air braking system even a small leakage may lead to complete failure of brakes. While in electromagnetic braking system as four disc plates, coils and firing circuits are attached individually on each wheel, even any coil fails the brake does not completely fails remaining three coil works properly. And this system needs very little of maintenance. In addition, it is found that electromagnetic brakes make up approximately 80% of all of the power applied brake applications. Electromagnetic brakes have been used as supplementary retardation equipment in addition to the regular friction brakes on heavy vehicles. The frictions brakes can be used less frequently and therefore practically never reach high temperatures. The brake linings would last considerably longer before requiring maintenance and the potentially brake fade problem could be avoided. This enhanced braking system not only helps in effective braking but also helps in avoiding the accidents and reducing the frequency of accidents to a minimum. Furthermore the electromagnetic brakes prevent the danger that can arise from the prolonged use of brake beyond their capability to dissipate heat.
With all the advantages of electromagnetic brakes over friction brakes, they have been widely used on heavy vehicles where the brake fading problem exists. The same concept is being developed for application on lighter vehicles. The concept designed by us is just a prototype and needs to be developed more because of the above mentioned disadvantages. These electromagnetic brakes can be used as an auxiliary braking system along with the friction braking system to avoid overheating and brake failure. ABS usage can be neglected by simply using a micro controlled electromagnetic disk brake system .These find vast applications in heavy vehicles where high heat dissipation is required. In rail coaches it can used in combination of disc brake to bring the trains moving in high speed. When these brakes are combined it increases the life of brake and act like fully loaded brakes. These electromagnetic brakes can be used in wet conditions which eliminate the anti-skidding equipment, and cost of these brake are cheaper than the other types. Hence the braking force produced in this is less than the disc brakes if can be used as a secondary or emergency braking system in the automobiles.
REFERENCES
-
LATCHING BRAKE USING PERMANENT MAGNET by Stephen Z. Oldakowski, Bedford, Ohio United States Patent Patent Number: 5,121,018
-
ADJUSTABLE MAGNETIC BRAKE by Hung-Chi Wu, 958-2, Ghung Shan Rd., Tao-Yuan, Taiwan United States Patent Patent Number: 5,096,024
-
MAGNETIC BRAKE SYSTEM FOR A VEHICLE by Jae- Woong Lee. Seoul, Rep. of Korea United States Patent Patent Number: 5,746,294
-
BRAKE DEVICE FORAN ELEVATOR WITH MONITORING CAPABILITIES by Karl Erny, Holzhausem United States Patent Patent No.: US 7,909,145 B2
-
MAGNETIC BRAKE by Albert E. Miller, Dayton, Ohio United States Patent Office Patent No 2,482,428
-
Kesavamurthy, N., Eddy-current in solid iron due to alternating magnetic flux, The Institution of Engineers Monograph, No. 339U, pp. 207213, June, 1959,
-
Ohyma, T., Adhesion at higher speeds, its basic characteristic, its improvement and some related problem, Japanese Railway Engineering, Vol. 108, 1988.
-
Mcconnell, H.M., Eddy-current phenomena in ferromagnetic material, AIEE Transactions,Vol. 73, part I, pp. 226234, July, 1954.
-
Ren He,Xuejun Liu Brake Performance Analysis of ABS for Eddy Current and Electrohydraulic Hybrid Brake System School of Automotive & Traffic Engineering, Jiangsu University, Zhenjiang 212013, China Received 24 September 2013; Revised 29 October 2013; Accepted 30 October 2013
-
G. G. Desta, Eddy Current Brake System, 2004, US 6,698,554 B2.
-
C. Jun, A study on robust control for anti-lock braking system, Automotive Engineering,vol.1,pp.1722,1998.
-
K. Lee Jr. and K. Park, Modeling of the Eddy currents with the consideration of the induced magnetic flux, in Proceedings of the IEEE Region 10th International Conference on Electrical and Electronic Technology, pp. 762768, August 2001.
-
A.C. Smith, S. Williamson, A. Benhama, L. Counter, and J.M. Papadopoulos, Magnetic drive couplings, in Proc. IEEE 9 the International Conference on Electrical Machines and Drives. Seattle, WA, 1999, pp. 232-236.
-
R. Limpert, Brake Design and Safety. Warrendale, PA: Society of Automotive Engineers, 1999.
-
Robert Bosch GmbH, Bosch Automotive Handbook. Warrendale, PA: Society of Automotive Engineers, 2004.
-
Cedrat, (2005, March), Flux ® One step ahead. [Online]. Available: www.cedrat.com.
-
Telma. (2004, December). Nos Produits. [Online]. Available: www.telma.com
-
http://www.nmbtc.com/bearings/608-bearing/
-
https://en.wikipedia.org/wiki/
-
www.wikipedia.org
-
www.cst.com
-
www.patentgenius.com
-
www.supermagnetman.com
-
https://www.lens.org/lens/
-
http://www.bios.net/daisy/patentlens/patentlens.html
-
http://www.google.com/patents/