
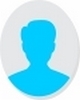
- Open Access
- Authors : Pramukh Ganapathy C , Dr. G Sarangapani , Dr. H.S Prasanna
- Paper ID : IJERTV11IS100084
- Volume & Issue : Volume 11, Issue 10 (October 2022)
- Published (First Online): 30-10-2022
- ISSN (Online) : 2278-0181
- Publisher Name : IJERT
- License:
This work is licensed under a Creative Commons Attribution 4.0 International License
Comparative Study on the Design Methods to Achieve Self-Compacting Concrete
Pramukh Ganapathy C Department of Civil Engineering Coorg Institute of Technology Kodagu, Karnataka, India -571216 |
Dr. G Sarangapani Department of Civil Engineering The National Institute of Engineering Mysuru, Karnataka, India-570008 |
Dr. H.S Prasanna Department of Civil Engineering The National Institute of Engineering Mysuru, Karnataka, India-570008 |
Abstract- Self-compacting concrete (SCC) has the property to flow and densify on its own. The mix of SCC will be generally cohesive which will prevent the bleeding and segregation issues in concrete. In general, the SCC mix demands the usage of mineral admixtures and the High Range Water Reducing admixtures to maintain its fluidity. These mineral admixtures are generally the by-products from various industries. The utilization of these mineral admixtures not only makes the SCC mix economical by reducing the but also gives an eco-friendly edge for concrete preparation as it reduces the disposal issues. M40 grade of SCC concrete is attempted to achieve through Nan Su and Modified Nan Su method in which the cement is supplemented with the incorporation of the mineral admixtures like Fly Ash, Sugarcane Ash, Kaolin Clay, and Wood As. The outcome of the work concludes that the SCC mixes produced with the modified Nan Su method provide better mechanical strength.
Keywords- Self Compacting Concrete; Compressive strength
I. INTRODUCTION
The Self Compacting Concrete (SCC) is being used widely mainly due to its advantages like reduction in time and vibration. It also provides better durability and finish. The main constituents in an SCC mix are similar to the conventional vibrated concrete which consists of cement as a binder, aggregates as filler and water for mixing. In addition to the regular constituent SCC demands the usage of additives which generally has chemical and mineral components.
The primary need of adopting SCC in construction is due to its flow ability and capabilities to fill the foam work with congested reinforcement. Henceforth, in order to prevent the blockage of concrete during passing complex reinforcement the usage of coarse aggregate content is to be reduced. The reduction in the coarse aggregate content boosts the cement requirement making the mix uneconomical and also increasing the hydration temperature. Hence to check the excess cement content in the mix the usage of other mineral admixtures as a replacement for cement helps in reducing the ill effects of increased cement content in the mix. In general, the mineral admixtures which has pozzolanic property is used in SCC mix. But, parallelly the works related to understanding the feasibility of utilizing other kinds of mineral admixtures are also being carried out.
The major drawback in adopting the SCC lies in the designing the mix of SCC as there is no such proven methodology to design SCC, whereas the SCC is generally designed by trial and error to meet the requirements of the mix specified by the European Federation of National Association for Representing Concrete (EFNARC) [1]. The EFNARC specifies the guidelines and recommends the tests to be carried out on a concrete mix to categorize it as SCC based on the ability to fill, pass, maintain fluidity and reduce segregation. Hence this present work aims in assessing the feasibility of developing the SCC mix by using two different methods of mix design and by incorporating Fly Ash, Sugarcane Ash, Kaolin Clay and Wood Ash in the mix as a replacement for the Cement.
-
Cement
The Ordinary Portland Cement (OPC) of 53 Grade Cement conforming to IS 12269:1987 [2] was used throughout this work. Its physical properties are tested as per IS 4031:1988 [3] [4][5] and are given in Table I.
-
Aggregates
River sand of specific gravity 2.63, fineness modulus 2.9 of Zone II gradation is used as fine aggregate. The crushed granite of 12 mm and down-size with specific gravity of 2.5 is used as coarse aggregate. The tests on the fine aggregate and coarse aggregate were performed as per IS: 383-1970 [6].
TABLE I. PHYSICAL PROPERTIES OF CEMENT
Physical properties
Results
Range
Specific gravity
3.03
3.12-3.19
Normal consistency (%)
32
30-35%
Initial Setting time (mins)
35
30
Final Setting time (mins)
580
600
-
Fly Ash
Fly ash is a by-product of thermal power plants. The particle size in Fly Ash is smooth and spherical and has a size ranging from 10 25 µm. The finer particles in fly ash generally help in improving the fluidity of a concrete mix. The properties of Fly Ash are shown in Table II.
-
Sugarcane Ash
Sugarcane industry produces stalks of sugarcane after extraction of the juice to prepare sugar and molasses. These sugarcane stalks are burnt in the process which has pozzolanic nature. Table II shows the properties of Sugarcane Ash.
-
Kaolin Clay
Kaolin clay is also called Lithomarge clay which generally consists of Aluminum Silicates. It is an important raw material in the industries which manufacture porcelain items. Table II shows the properties of Kaolin Clay.
-
Wood Ash
The Wood Ash used in this study is obtained from the local tobacco industry of Hunsur, Karnataka, India. The Wood Ash (WA) is obtained by burning the Tamrind wood to process and dry the wood. The chemical constituents of the wood ash is tabulated in Table III and the properties of the wood ash is tabulated in Table II.
Materials
Properties
Colour
Consistency
Sp. Gravity
Fly Ash
Greyish Black
140
2.27
Sugarcane Ash
Dull white
38
2.70
Kaolin Clay
Cream White
72
2.40
Wood Ash
White Grey
59
2.20
TABLE II. PHYSICAL PROPERTIES OF MINERAL ADMIXTURES
Table V and Table VI show the mix proportion that was adopted from two different methods. A design target strength adopted was M40.
TABLE V. MIX PROPORTION ARRIVED THROUGH NAN SU METHOD
Materials (Kg/m3)
Mix Containing
Fly Ash
Sugarcane Ash
Kaolin Clay
Wood Ash
Cement
290
290
290
290
Powder
63
155
102
111
Fine Aggregate
961
961
961
961
Coarse Aggregate
743
743
743
743
Water
209
179
194
186
Plasticizer
6.36
8.00
7.06
7.22
Materials (Kg/m3)
Mix Containing
Fly Ash
Sugarcane Ash
Kaolin Clay
Wood Ash
Cement
400
400
400
400
Powder
18
43
28
31
Fine Aggregate
961
961
961
961
Coarse Aggregate
743
743
743
743
Water
192
184
188
186
Plasticizer
7.52
7.98
7.72
7.76
TABLE VI. MIX PROPORTION ARRIVED THROUGH MODIFIED NAN SU
-
Super Plasticizer
The superplasticizer named Fosroc Conplast SP430 DIS is used and its properties are shown in Table IV as mentioned by the manufacturer.
TABLE III. CHEMICAL COMPOSITION OF WOOD ASH
-
ACCEPTANCE TESTS ON SCC MIXES BASED ON EFNARC
GUIDELINES
The laboratory tests are conducted to gauge the requirements of the SCC mix as per the EFNARC [1]. The accepted range of results is represented in Table VII and the test results are tabulated in Table VIII and Table IX for both mixes.
TABLE VII. SCC ACCEPTANCE CRITERIA AS PER EFNARC
Test
Accepted Range
Slump Flow
650 800 mm
V- funnel
6-12 sec
L- box
0.8-1.0
U- box
0-30 mm
Particular
Value
SiO2 (%)
66.3
Al2O3 (%)
4.70
Fe2O3 (%)
2.20
CaO (%)
10.23
MgO (%)
5.32
Na2O (%)
2.7
K2O (%)
1.9
Loss of Ignition
4.78
TABLE
VIII. FRESH
TEST ON
MIXES
PREPARED
THROUGH
NAN SU
METHOD
Mix with
Mix Containing
Slump Flow
V- funnel
L- box
U- box
Fly Ash
700 mm
9 sec
0.9
20 mm
Sugar Cane Ash
725 mm
7 sec
1.0
10 mm
Kaolin Clay
675 mm
11 sec
0.8
24 mm
Wood Ash
690 mm
10 sec
0.9
26 mm
TABLE IV. PROPERTIES OF SUPER PLASTICIZER
Physical properties
Result
Specific gravity
1.2
Colour
Brown liquid
Brand
Fosroc Conplast SP430 DIS
II. MIX PROPORTIONING METHODS
-
Nan Su Method
This method was introduced by Nan Su, et al [7]. This method gives the mix design and proportioning of various concrete ingredients.
-
Modified Nan Su Method
Vilas V. Karjinni et.al [8] proposed a Mixture Proportion Procedure for SCC. This method of mixed design highlighted the limitations of the Nan Su et.al method. Vilas V et.al introduced the correction factor for the cement content to make the Nan Su et.al method suitable for SCC design for grades less than M50.
TABLE IX. FRESH TEST ON MIXES PREPARED THROUGH MODIFIED NAN SU
Mix with
Mix Containing
Slump Flow
V- funnel
L- box
U- box
Fly Ash
740 mm
8 sec
0.8
25 mm
Sugar Cane Ash
760 mm
7 sec
1.0
15 mm
Kaolin Clay
710 mm
10 sec
0.9
28 mm
Wood Ash
720 mm
9 sec
0.8
mm
-
-
TEST ON HARDEND PROPERTIES
The concrete specimens were cured for a period of 7,14 and
28 days and were tested for compressive strength and flexural strength and split tensile strength in accordance with IS: 516-1959 [9] and IS: 5816-1999 [10]. The compressive strength results are tabulated in Table X and Table XI. The flexural strength results are tabulated in Table XII and Table
-
The Split tensile strength results are tabulated in Table XIV and Table XV.
TABLE X. COMPRESSIVE STRENGTH OF SCC PREPARED THROUGH
NAN SU METHOD
Mix with
Compressive Strength (MPa)
7 Days
14 Days
28 Days
Fly Ash
24.50
30.50
33.00
Sugar Cane Ash
26.00
31.50
35.50
Kaolin Clay
23.50
29.50
32.00
Wood Ash
19.50
25.00
28.50
TABLE XI. COMPRESSIVE STRENGTH OF SCC PREPARED THROUGH
MODIFIED NAN SU METHOD
Mix with
Compressive Strength (MPa)
7 Days
14 Days
28 Days
Fly Ash
30.50
36.50
40.50
Sugar Cane Ash
33.50
39.50
41.50
Kaolin Clay
31.00
34.00
40.00
Wood Ash
26.00
32.50
36.00
TABLE XII. FLEXURAL STRENGTH OF SCC PREPARED THROUGH
NAN SU METHOD
Mix with
Compressive Strength (MPa)
7 Days
14 Days
28 Days
Fly Ash
3.15
3.50
3.60
Sugar Cane Ash
3.20
3.60
3.75
Kaolin Clay
3.00
3.50
3.50
Wood Ash
2.75
3.20
3.30
TABLE XIII. FLEXURAL STRENGTH OF SCC PREPARED THROUGH
MODIFIED NAN SU METHOD
Mix with
Compressive Strength (MPa)
7 Days
14 Days
28 Days
Fly Ash
3.60
3.95
4.10
Sugar Cane Ash
3.75
4.00
4.20
Kaolin Clay
3.55
3.70
3.95
Wood Ash
3.20
3.40
3.80
TABLE XIV. SPLIT TENSILE STRENGTH OFSCC PREPARED THROUGH
NAN SU METHOD
Mix with
Compressive Strength (MPa)
7 Days
14 Days
28 Days
Fly Ash
1.80
2.15
2.20
Sugar Cane Ash
1.90
2.25
2.30
Kaolin Clay
1.70
2.20
2.15
Wood Ash
1.20
1.50
1.90
TABLE XV. SPLIT TENSILE STRENGTH OF SCC PREPARED THROUGH
MODIFIED NAN SU METHOD
Mix with
Compressive Strength (MPa)
7 Days
14 Days
28 Days
Fly Ash
2.25
2.50
2.70
Sugar Cane Ash
2.35
2.65
2.80
Kaolin Clay
2.10
2.35
2.50
Wood Ash
1.85
2.15
2.30
-
DISCUSSIONS ON THE RESULTS
-
Mix Proportion
In both methods of mix design, the consistency of the finer materials is the main factor that determines the quantity of powder in the mix. Adopting Nan-Su et al and the Modified Nan Su method of mix design, will reduce the number of trails to achieve the perfect SCC mix to meet the EFNRAC guidelines.
The cement content in the Modified Nan Su method is more than that of the Nan Su method as the modification factor is adopted.
-
Compressive Strength
The compressive strength test results show that all the mixes which were prepared by adopting the Nan Su method failed to attain the target design strength of 40 MPa. The compressive strength of the SCC mixes prepared with the Modified Nan Su method with admixtures like Fly Ash, Sugarcane Ash, Kaolin Clay and Wood Ash is 18.51%, 14.45%, 20% and 20.83% more than the mixes prepared with the Nan Su method with the same admixtures respectively.
The SCC prepared with the Nan Su method containing Sugarcane Ash had better compressive strength gain than all other mixes with about 35.50 MPa. The compressive strength achieved by the SCC mix containing Sugarcane Ash reported compressive strength that is 7.5%, 10.9% and 24.5% more than the SCC mix containing Fly Ash, Kaolin clay and Wood Ash respectively.
Unlike the SCC mix prepared by adopting the Nan Su method, the SCC mixes were designed by adopting the Modified Nan Su method that achieved the target designed strength of 40 MPa except with the mix containing Wood Ash.
The SCC prepared with the Modified Nan Su method containing Sugarcane Ash had better compressive strength gain than all other mixes with about 41.00 MPa for 28 days of curing. The compressive strength achieved by the SCC mix containing Sugarcane Ash reported a compressive strength that is 2.5%, 3.75% and 15.27% more than the SCC mix containing Fly Ash, Kaolin clay and Wood Ash respectively.
-
Flexural Strength
The flexural strength of the SCC mixes prepared by the Modified Nan Su method is higher than the mixes prepared by the Nan Su method. The flexural strength gain is alike to that of Compressive strength in which the mixes containing Sugarcane Ash showed better flexural strength than the other mixes. In the case of mixes produced with the Nan Su method, the flexural strength of the mix with Sugarcane ash is 4.16%, 7.14% and 13.63% higher than that SCC mix containing Fly Ash, Kaolin clay and Wood Ash respectively. Whereas in the case of the mixes produced with the Modified Nan Su method the flexural strength of the mix with Sugarcane ash is 1.2%, 8.10% and 17.64% higher than that SCC mix containing Fly Ash, Kaolin clay and Wood Ash respectively.
The flexural strength of the SCC mixes prepared with the Modified Nan Su method with admixtures Fly Ash, Sugarcane Ash, Kaolin Clay and Wood Ash is 8.86%, 6.25%, 5.40% and 2.94% higher than the mixes prepared with the Nan Su method with the same admixtures respectively.
-
Split Tensile Strength
The Split Tensile Strength of the SCC mixes prepared by the Modified Nan Su method is higher than the mixes prepared by the Nan Su method. The split tensile strength gain has a similar pattern as that of Compressive strength and flexural strength in which the mixes containing Sugarcane Ash showed better split tensile strength than the other mixes. In the case of mixes produced with the Nan Su method, the flexural strength of the mix with Sugarcane ash is 4.34%,
6.52% and 17.39% more than that of SCC mix containing Fly Ash, Kaolin clay and Wood Ash respectively. Whereas in the case of the mixes produced with the Modified Nan Su method the flexural strength of the mix with Sugarcane ash is 3.57%, 10.71% and 17.85% more than that of SCC mix containing Fly Ash, Kaolin clay and Wood Ash respectively.
The flexural strength of the SCC mixes prepared with the Modified Nan Su method with admixtures like Fly Ash, Sugarcane Ash, Kaolin Clay and Wood Ash is 18.51%, 17.85%, 14.00% and 17.39% more than the mixes prepared with the Nan Su method with the same admixtures respectively.
-
-
CONCLUSIONS
-
-
The Nan Su method and Modified Nan Su method can be adopted to achieve the desirable fresh properties to meet the EFNARC standards to ensure viscosity, the ability to fill and the passing of the Self Compacting Concrete mixes.
-
The quantity of mixing water and the superplasticizer is dependent on the quantity of cement and admixtures in the mix.
-
The Strength gain in the mixes prepared with the Modified Nan Su method is better than the mixes prepared with the Nan Su method. This may be due to the higher cement and lesser admixture content in the Modified Nan Su method.
-
The Sugarcane Ash can be considered an effective partial replacement for cement as it provided better strength than the other admixtures.
-
Fly Ash and Kaolin clay can also be used as a partial replacement for cement as there is not much reduction in the strength.
properties of self consolidating concrete, The IES Journal Part A: Civil & Structural Engineering, Vol 7, 2014, pp. 229-242.
[13] Netravati T Shepur, B.Shivakumaraswamy, Sahana and G. K, S.Vijaya, Experimental Study on Strength Compacting Concrete by Incorporating Metakaolin and Polypropylene Fiber, International Journal of Engineering Research & Technology (IJERT), Vol. 3 Issue 7, July 2014 [14] M. Fadee, R.Mirhosseini, R. Tabatabaei and M.J. Fadaee, Investigation on using copper slag as part of cementations materials in self compacting concrete, Asian Journal of Civil Engineering, Vol. 16, 2015, pp. 368-381. [15] T.Adhavanathan and V.Vinoth, Experimental Investigation of Self Compacting Concrete by using Copper Slag and Fly ash, International Journal for Scientific Research & Development, Vol. 3, 2015, pp. 384- 389. [16] K. S. Jhansirani and A. Jagannathan, Studies on Effect of Mineral Admixtures on Durability of Self Compacting Concrete, European Journal of Advances in Engineering and Technology, Vol.2, 2015, pp. 87-94. [17] Daniel C, Joel Shelton J, Vincent Sam Jebadurai S and Arun Raj E, Studies on High Strength Self Compacting Concrete with Copper Slag for M30 grade, International Journal of Research in Engineering and Technology, Vol. 5, 2016, pp. 74-78.REFERENCES
[1] European Federation of National Associations Representing for Concrete, Specification and Guidelines for Self-Compacting Concrete, 2009, United Kingdom. [2] IS 12269: 2013, Specification for 53 Grade ordinary Portland cement, Bureau of Indian Standards, and New Delhi, India. [3] IS 4031- 4:988, Methods of Physical Tests for Hydraulic Cement, Part-4: Determination of consistency of standard cement paste. Bureau of Indian Standards, New Delhi, India. [4] IS 4031- 5:1989, Methods of Physical Tests for Hydraulic Cement, Part-5:Determination of Initial and Final setting times, Bureau of Indian Standards, New Delhi, India. [5] IS 4031- 6:1988, Methods of Physical Tests for Hydraulic Cement, Part-6: Determination of Compressive strength of Hydraulic Cement, Bureau of Indian Standards, and New Delhi, India. [6] IS 383:1970, Specification for Coarse and fine aggregates from natural sources for concrete, Bureau of Indian Standards, New Delhi, India. [7] Nan Su, Kung-Chung Hsub, His-Wen Chai, A simple mix design method for self-compacting concrete, Cement and Concrete Research 31 (2001) 17991807. [8] Vilas V. Karjinni, Shrishail B. A, "Mixture proportion procedure for SCC,"Indian Concrete Journal, June 2009, pp:35-41. [9] IS 516: 1959, Methods of tests for Strength of Concrete, Bureau of Indian Standards, New Delhi, India. [10] IS 5816: 1999, Splitting Tensile Strength of Concrete-Method of test, Bureau of Indian Standards, New Delhi, India. [11] Christos G. Fakitsas., Panagiota Aleni A., Papakonstantinou., PanousD. Kjousis., Am Asce and Athina Savva Effect of recycled concrete aggregate on compressive and shear strength of high-strength- – Self- compacting concrete, ASCE., Sept 2011.
[12] Iman Afshoon and Yasser Sharifi., Ground copper slag as a supplementary cementing material and its influence on the fresh