
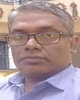
- Open Access
- Authors : T. Raghunathan
- Paper ID : IJERTV11IS070026
- Volume & Issue : Volume 11, Issue 07 (July 2022)
- Published (First Online): 16-07-2022
- ISSN (Online) : 2278-0181
- Publisher Name : IJERT
- License:
This work is licensed under a Creative Commons Attribution 4.0 International License
Upcycycling of Textile Dyeing Industry Effluent Treatment Plant Sludge using Waste Plastic and used Cooking Oil As Binders
T. Raghunathan
Lecturer/Civil Engineering
P.A.C. Ramasamy Raja Polytechnic College, Rajapalayam, Tamil Nadu, India
Abstract- Textile Industry is one of the major contributors of water pollution in Tiruppur region of Tamilnadu. A stringent implementation of effluent treatment plants in major textile industries and Common effluent treatment plants for small scale industries have reduced the problem to some extent. But the sludge thus created from the treatment of textile industry effluent is posing problems of storage and disposal as it contains traces of heavy metals, sulphates and chlorides in heavy concentration. These chemicals and heavy metals again pose a serious challenge to the environment, when sludge is stored in open yards and dumped in landfills. These chemicals again leach into the rain water and surface water. Hence there is a chain of problems posed by both textile industry effluent and treatment plant sludge of textile industry. Hence many researches are going on at global level to encapsulate the sludge into construction or building material. This paper gives an insight into the attempts by various researchers to incorporate the sludge as a inert material into the concrete with various types of binders such as cement, geopolymer and plastic. This research shows small breakthrough in attempt to encapsulate the textile sludge using waste plastic of poly propylene and polyethylene and used oil in various ratios.
Key words Textile Industry, Effluent, Sludge, Plastic,Poly propylene, Polyethylene & Used Oil
-
INTRODUCTION
Textile industries are one of the essential industries which cater to our clothing requirement and also bedding, curtains, car seat covers, etc. Textile industries use various processes dyeing, compacting, knitting, embroidery, bleaching, stitching and finishing to get final products. The dyeing, bleaching and final washing of finished products create effluents which are polluting surface water resources and render the water unsuitable for human use. Hence the Pollution control board stringently asked the industries to create effluent treatment plants to treat the effluents to the level that will make them suitable for disposal into natural water sources. But the main product of the treatment is the sludge, which contains various chemicals such as cadmium, chromium, lead, zinc, copper used for colours in dyeing and sulphates and chlorides above 1000 mg/litre.
textile sludge of 200 tonnes/day are generated in Tirupur[1]. Which is huge volume of waste. Many researchers have tried to work out a composite out of cement binder. But the success rate of the cement concrete or cement based building blocks. The following are the review of literature.
Plastic[18] is very useful modern life almost all gadgets are made of plastic . Most plastic is not recyclable and not biodegradable. Plastic products often break down into microplastics that can pollute ecosystems and harm bio-life. According[19] to the recent United Nations Environment Programme report, the world produces 400 million tonne single-use plastic (SUP) waste annually (47 per cent of the total plastic waste). It is estimated that only
9 per cent of the plastic is getting recycled worldwide. Hence there is lot of scope in recycling the waste plastic into some useful construction material. In this paper Waste plastic such as Poly propylene and Poly ethylene are used as binders along with textile sludge as inert filler.
Used cooking oils are oils and fats that have been used for cooking or frying in the food processing industry, restaurants, fast foods and at consumer level, in households. During frying, several properties of oil are altered, Total Polar Compounds(TPC) are formed on repeated frying. The toxicity of these compounds is associated with several diseases such as hypertension, atherosclerosis, Alzheimers disease, liver diseases. Therefore, it is essential to monitor the quality of vegetable oils during frying. In order to safeguard consumer health, FSSAI has fixed a limit for Total Polar Compounds at 25 percent beyond which the vegetable oil shall not be used.
It is therefore envisaged to use the three wastes viz. Textile Dyeing Industry effluent treatment plant sludge, waste plastic and used cooking oil to create useful composites
-
LITERATURE REVIEW
-
Cement Based Researches
The Textile ETP sludge[1] up to a maximum of 30% substitution for cement was used to manufacture of non- structural building materials. The addition of sludge to the cement delays the setting process of the building components. Replacement of fine aggregate with sludge[2] in conventional concrete mix affects workability and density of concrete. The increase in the percentage of ETP Sludge[3] in concrete the compressive strength and split tensile strength seems to decrease. the workability of the mix decreases with the increase in the textile ETP sludge content. Addition of textile sludge to concrete[4] affects the strength characteristics of concrete. The Concrete[5] is stable till after 15% replacement of sand with textile and
tannery sludge together based on the strength on 7 th and 28th days. The maximum amount [6] of textile sludge that can be added is in range of 6 to 9% due to the presence of chromium up to the level of 358mg/kg. with an increase in ETP sludge[7] percentages from 5% to 20%,the workability decreases. The ETP sludge[8] can be used effectively a 0.75:1.7 ratio to make brick as it gives compressive strength above 10 N/mm 2 , low water absorption and nil efflorescence. Bricks[9] were prepared by incorporating textile sludge at different proportions (10 40%) and temperature (600, 900 and 1200 °C). About 26 and 50% of energy were saved during firing of 10 and 20% sludge-containing bricks, respectively, compared with pristine clay bricks. Concrete[10] block by replacement of cement with 10, 20, 30, 40, and 50% incinerated textile sludge ash, and the manufactured block.The replacement cement by the ash increases the hydration time reduced, and up to 20%, sludge ash incorporation in the concrete mix design gives the designed compressive strength. Textile sludge [11] was incorporated in fly ash brick manufacturing and it was observed that with increase in sludge content, there is a decrease in compressive strength of bricks. The initial and final setting time [12]of the concrete has increased due to high water absorbing capacity of the sludge. The combination [13] of 10% textile waste sludge along with 3% nano alumina blended cement concrete leads to enhanced strength and durability characteristics as compared to all other concrete specimens and it was found to better eco-friendly construction material. the compressive strength decreases[14] where adding the textile sludge partially replacement of cement, conclude that the use of textile sludge up to a maximum of 30%substitution for cement may be possible in the manufacture of nonstructural building materials. The TES [15] markedly delayed the OPC hydration at the early age, and seriously degraded mechanical strength and TES introduced more weak interfaces in the cement mortar, thus increased the total porosity especially the macropores.
-
Geopolymer Based Researches
Leaching of Salts from Cubes in TDS
300
250
200
150
100
50
0
PPTS 1:4 PPUOTS 2:1:1
The composite[16] shows appreciable reduction of compressive strength with increase in Dyeing Industry Effluent Treatment Plant Sudge(DIETP-S). Typical textile sludge [17] was having high heavy metal contents. The replacement cement by the Textile sludge ash increases the hydration time.
-
-
RESEARCH METHODOLOGY
-
The waste plastic is melted using a heating arrangement for 1 hr not exceeding the melting temperature of the plastic. When waste plastic becomes viscous paste, textile sludge is mixed in various ratios and a resultant composite is cast into moulds of 50 sq.cm. The cubes are tested for density, water absorption and compressive strength.
-
The waste plastic and used oil is melted using a heating arrangement for 1 hr not exceeding the melting temperature of the plastic. When plastic and oil becomes viscous paste, textile sludge is
mixed and a resultant composite is cast into moulds of 50 sq.cm. The cubes are tested for density, water absorption and compressive strength.
-
-
RESULTS AND DISCUSSIONS
TABLE 1: TDS INCREASE IN WATER DUE TO TEXTILE SLUDGE
S.NO
DAY
TDS
1.
0
38 WITHOUT TS
2.
0
500
3.
1
710
4.
2
850
5.
3
1060
6.
4
1300
7.
5
1420
8.
6
1440
Increase in TDS of water with 0.1 Textile Sludge
2000
1500
1000
500
0
1 2 3 4 5 6 7 8
Series2
Day
PPTS 1:4
PPUOTS 2:1:1
(Initial) 0
50
32
(Instant) 0
70
50
1
130
110
2
190
160
3
253
203
4
253
206
TABLE 2: LEACHING OF SALT FROM CUBES BY TDS
TABLE 3 COMPARISION OF RESULTS
Mix
Dry density Gms/cc
Water Absorption in Percen Tage
Compressive strength N/mm2
PPRS14C RED SOIL
1.5
2.9
12
PPRS14F RED SOIL
1.69
2.4
24
PPTS14
0.88
6.5
24.03
PPTS12
0.86
3.4
20.02
PPUOTS1 2:1:1
1.02
1.4
12.01
PPUOTS2 3:1.5:1.2
0.918
0
8
PPUOTS3 3:1.5:0.9
0.816
0
6
PPUOTS4 3:1.5:0.6
0.88
0
8.01
PPUOTS5 1:3:3
1.18
1.21
0
PEUOTS6 3:1.5:2
.084
0
12.01
PPUOTS7 3:2:2
0.87
0
8
PPUOTS8 2:2:2
0.9
6.4
10
PPPEUOTS9 1:1:1:1
0.74
1.96
10
WATER ABSORPTION IN PERCENTAGE
7
6
5
4
3
2
1
PPRS14C
PPRS14F PPTS14 PPTS12 PPUOTS1 PPUOTS2 PPUOTS3 PPUOTS4
PPUOTS5 PEUOTS6 PPUOTS7 PPUOTS8 PPPEUOTS9
0
2
1.5
1
0.5
0
DENSITY IN GMS PER CC
COMPRESSIVE STRENGTH IN N/MM2
30
25
20
15
10
5
PPRS14C
PPRS14F PPTS14 PPTS12 PPUOTS1 PPUOTS2 PPUOTS3 PPUOTS4
PPUOTS5 PEUOTS6 PPUOTS7 PPUOTS8 PPPEUOTS9
0
PPRS14C
PPRS14F PPTS14 PPTS12 PPUOTS1 PPUOTS2 PPUOTS3 PPUOTS4
PPUOTS5 PEUOTS6 PPUOTS7 PPUOTS8 PPPEUOTS9
-
CONCLUSION
Both Cement and Geopolymer based concrete show lowering of strength with addition of DIETPS. A maximum replacement of upto 20% by weight of filler materials have been done. The optimum percentage is 10 for all types of concrete. The DIETPS already has high concentration of sulphates, chlorides and heavy metals. These interfere with strength and durability. Hence with durability point of view DIETPS is not suitable for use in cement concrete. We must come up with a suitable binder apart from Cement or Geopolymer. PPTS14 Shows highest compressive strength, then other composites show less strength. The addition of used oil gives lower strength and lowest water absorption. Waste plastic may be the apt binder for DIETPS. Hence a lot of scope is there for waste plastic as binder with
DIETPS as filler material. Self-compacting mix can be achieved using higher percent of used oil. It should be noted that lessening the Plastic and increasing used oil gives no binding as happened with PPUOTS5 cube. TDS of TS increased by 500ppm at the instant of mixing in water. But cubes leaching results increased by only 20ppm. At 7 days the TDS of TS in water was 1420ppm but the cubes show only 1/7th of the leaching. After 3rd day of Leaching of salt from cubes as TDS, the value increase was negligible hence leaching almost stopped. This proves the effectiveness of plastic as effective encapsulating and binding material.
REFERENCES
[1] J. Balasubramanian a , P.C. Sabumon a,*, John U. Lazar a , R. Ilangovan b Reuse of textile effluent treatment plant sludge in building materials, Elsevier,Waste Management 26 (2006) 2228 [2] Mr. G.J.Kulkarni Prof. A.K.Dwivedi & Prof. S.S.Jahgirdar Textile Mill Sludege as Fine Aggregate in Concrete, Global Journal of Researches in Engineering Industrial Engineering Volume 12 Issue 2 Version 1.0 Year 2012, Publisher: Global Journals Inc. (USA)Online ISSN: 2249-4596 Print ISSN:0975-5861
[3] Sandesh N U, Varun K and Prashanth V P A study on engineering properties of textile ETP sludge based cement concrete, International Journal of Innovations in Engineering and Technology (IJIET), ISSN: 2319 1058 ,Volume 4 Issue 4 December 2014 [4] Sreedevi Lekshmi1 , Sheeba Sasidharan, EXPERIMENTAL INVESTIGATION ON THE USE OF TEXTILE SLUDGE INCONCRETE, International Journal of Advances in Engineering & Technology, Aug., 2015. ISSN: 22311963, Vol. 8, Issue 4, pp. 559-
565.
[5] Dr.N.Vasudevan1 M.P.Raj2, Reuse of Textile and Tannery Sludge in Concrete Fine Aggregates, IJSRD – International Journal for Scientific Research & Development| Vol. 4, Issue 07, 2016 | ISSN (online): 2321-0613 [6] Baskar.R and Meera Sheriffa Begum.K.M (2006), Characterization and reuse of textile effluent treatment plant, Journal of the University of Chemical Technoloy and Metallurgy, 41, 4, 2006,473-478
[7] S.K.Gowtham, G.L.Bharanitharan, STUDY ON STRENGTH OF CONCRETE CONTAINING EFFLUENT TREATMENT PLANTWASTE, InternationalResearch Journal of Engineering and Technology (IRJET) e-ISSN: 2395-0056 Volume: 08 Issue: 03 | Mar 2021 www.irjet.net
[8] M.Gunavel, S.Kowsalya, M. Lakshmi priya, M. Lubaba Shahathiya,R. Harivarshana Experimental Study on Strength of Brick Using ETP Sludge and Cement International Journal of Advance Research and Innovation, ISSN 2347 3258, Volume 6, Issue 4 (2019) 1-3
[9] Dawit Alemu Beshah, Girum Ayalneh Tiruye & Yedilfana Setarge Mekonnen Characterization and recycling of textile sludge for energy-efficient brick production in Ethiopia, Environmental Science and Pollution Research volume 28, pages1627216281 (2021) [10] Esubalew Kasaw, ZelalemAdane, GemedaGebino, NakachewAssefa, AberaKechi, KetemaAlemu, "Incineration of Textile Sludge for Partial Replacement of Cement in Concrete Production: A Case of Ethiopian Textile Industries", Advances in Materials Science and Engineering, vol. 2021, ArticleID 9984598, 6 pages, 2021. https://doi.org/10.1155/2021/9984598 [11] S MuraliKrishnan, V R Giridev ,Utilization of Textile Effluent
Waste Sludge in Brick Production , ,
https://www.fibre2fashion.com/industry-article/4916/utilization-of- textile-effluent-waste-sludge-in-brick-production
[12] R. Srinivasprabhu, V.J. Ahilsaravanan, M. Aravindh, S. Naveenkumar, S. Sarankumar, Experimental Study on Sludge from Common Effluent Treatment Plant as a Partial Replacement of Fine Aggregate in Concrete , International Journal of Scientific & Engineering Research Volume 10, Issue 3, March-2019 ISSN 2229-5518
[13], Praveenkumar T. R. , Manigandan, S. Gemede, Habtamu Fekadu , Prabu, V. , Balamoorthy, Dhivya Rath, Badrinarayan, Effective utilization of waste textile sludge composite with Al2O3 nanoparticles as a value-added application Applied Nanoscience, Online First, Pub Date:July 2021,DOI:10.1007/s13204-021-02001-4 [14] Jayakumar .P .T1, Ram Kumar .V .R2, Suresh Babu. R3, Mahesh Kumar .M4s , Experimental Investigation on Paver Blocks using Steel Slag as Partial Replacement of Aggregate and Sludge as Partial Replacement of Cement International Journal of Science andResearch (IJSR), India Online ISSN: 23197064,
Volume 2 Issue 5, May 2013 www.ijsr.net,
[15] ZhanBao JianJiang-ShanLiXuanDong XingPoon, Recycling hazardous textile effluent sludge in cement-based construction materials: Physicochemical interactions between sludge and cement, ELSEVIER, Journal of Hazardous Materials, Volume 381, 5 January 2020, 121034 [16] Raghunathan T, A Study on Geopolymer with Dyeing Industry Effluent Treatment Plant Sludge, https://doi.org/10.31142/ijtsrd19165 [17] Esubalew Kasaw, Zelalem Adane,3 Gemeda Gebino,1 Nakachew Assefa,2 Abera Kechi,1 and Ketema Alem, Incineration of Textile Sludge for Partial Replacement of Cement in Concrete Production: A Case of Ethiopian Textile Industries, Advances in material science and Engineering, Hindawi publications, Volume 2021 |Article ID 9984598 | https://doi.org/10.1155/2021/9984598 [18] https://scienceexchange.caltech.edu/topics/sustainability/plastic- waste-pollution