
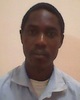
- Open Access
- Authors : Okunlola Babatunde Abraham, Okogbue Emmanuel Chilekwu, Olabanji Olayinka Mohammed, Ewetumo Theophilus, Adeboye Ademola Olumide Christopher
- Paper ID : IJERTV9IS100247
- Volume & Issue : Volume 09, Issue 10 (October 2020)
- Published (First Online): 11-11-2020
- ISSN (Online) : 2278-0181
- Publisher Name : IJERT
- License:
This work is licensed under a Creative Commons Attribution 4.0 International License
Published by : International Journal of Engineering Research & Technology (IJERT)
http://www.ijert.org ISSN: 2278-0181
Vol. 9 Issue 10, October-2020
Design, Construction and Control of a Wireless
Mobile Underwater and Surface Vehicle for
Hydro-Meteorological Parameters Monitoring
Okunlola Babatunde Abraham,
Okogbue Emmanuel Chilekwu
Department of Meteorology and Climate Science
Federal University of Technology, Akure
Ondo State, Nigeria
Ewetumo Theophilus
Department of Physics
Federal University of Technology, Akure
Ondo State, Nigeria
Olabanji Olayinka Mohammed
Department of Mechanical Engineering
Federal University of Technology, Akure
Ondo State, Nigeria
Adeboye Ademola Olumide Christopher
Department of Aerospace Engineering
The Air Force Institute of Technology, Kaduna
Kaduna State, Nigeria
Abstract—The purpose of this research is to develop both surface and underwater vehicles, which can adjust its altitude freely by changing the direction of propulsive forces and making the vehicle flexible when moving in the water with the ability to gather oceanographic data. According to [4], described that using asymmetrical structure would be better for the underwater vehicle. Wireless Mobile Underwater and Surface Vehicle for Hydrological Parameters Monitoring (WMUSVHPM) is a good robotic machine that can be used in a wide area for detailed survey and oceanographic data collection because the vehicle does not have to be connected to the support vessel. It can collect data in three dimensions from the underwater world, meaning that it has the ability to simultaneously measure many parameters in the habitat through the capture of a realistic picture of the natural environment. This would help marine scientists to understand the ocean in new ways. For example, it could use a camera to count fishes within a certain three-dimensional range, and at the same time measure the quality of the water in which the fishes live and also to supersede human to work at hard to access or jeopardizing underwater region to do certain specific tasks like environmental monitoring, water pollution control, offshore oil and gas systems maintenance, pipeline and telecommunication cables surveys, mine detection, oceanographic sampling, and hydrographic surveys. The design, construction, and control of a WMUSVHPM can be divided into three phases. The first phase involves the design and construction of the WMUSV, including the mechanical system, power system, and body of the vehicle. The second phase involves the system identification using an incorporated Global Positioning System (GPS) for the remotely control, simulating the parameters for tracking and positioning control of the vehicle with on-board sensors and software. The third phase involves the design and construction of surface and underwater sensors for sea surface and underwater temperature, turbidity, depth, and data logger for data averaging and archiving. WMUSV unit will be constructed by low-cost material like commercial grade polyvinyl chloride (PVC) pipes.The designed vehicle has 6 degrees of freedom motion simulators control using rotational matrixes. With a reasonable cost, a semi-potable the WMUSVHPM prototype has been designed and simulated by using SolidWorks and assembled with a mechanical system, the module of an electronic system for the development of a controller. Furthermore, the solar panel type used in the construction of this vehicle determines the size of the vehicle and this will be put into consideration in the future design since there are smaller solar panels with high wattage in the market now and will be able to accommodate more sensors. Future development and improvement in the design compared to other AUVs will lead to a more portable design and cheaper in the long run.
Keywords—Micro-controllers; PVC pipes; camera; GPS
I. INTRODUCTION
The applications of underwater vehicles have been impressive in recent years in areas such as marine environment, submarine earthquake, exploration, oceanographic mapping, ocean life and marine resources research, mines clearing operation, cable laying, security inspection, pipeline tracking and deep ocean explorations are carried out. [5]. The collection of ocean data by survey and observation in the actual sea is necessary for studies and development; this is because the ocean has low transparency and the whole deep sea cannot be observed in detail from the surface. Therefore, surveys and observation with the ship are not enough. However, the water pressure cannot step into the deep sea easily because atmospheric pressure increases every 10m diving down into the deep sea.
Underwater Vehicles (UVs) are the most difficult types of unconnected to vessel systems, being mobile, with difficult dynamics and non-holonomic kinematics system. They are increasingly being recognized as a keystone technology for projecting human scientific and economic interests into the deep Ocean [9].
Different structures with different sizes of underwater vehicles are developed. Most of design underwater vehicles are torpedo-like form with rationalizing bodies [9], some are in small sizes of AUVs and also, there are some other AUVs that adopt different body shapes. [11].
Since the propulsion system is one of the critical facts for the performance of underwater vehicles because it is the foundation of control layers of the total system. Propulsion devices have different types of examples are; paddlewheel, poles, magnetohydrodynamic drive, sails and oars.
IJERTV9IS100247 www.ijert.org
Published by : International Journal of Engineering Research & Technology (IJERT)
http://www.ijert.org ISSN: 2278-0181
Vol. 9 Issue 10, October-2020
The most common and traditional propulsion methods use for driving underwater vehicles are paddlewheel thruster, it designs with two thrusters installed on the vehicle, one for forwarding motion and the other for downward motion. The disadvantages of using paddlewheel thruster are pronounced, e.g., it is easy to trouble the water around the vehicles. Meanwhile, the increase in used for paddlewheel thrusters, also increase in weight, noise and energy consumption.
The steering strategies of traditional underwater vehicles more than thrusters are used for changing the angular rudders or using differential propulsive forces. Certainly, underwater vehicles can also be used vectored propellers [8].
[2] make used of multi-channel hall-effect thrusters which require vector composition and vector propel. [1] preferred an Autonomous Underwater Vehicle equipped with a vectored thruster. Also, an example of a design vectored propulsion system used on the airplane is vectoring thrusters [7].
The purpose of this research is to develop both surface and underwater vehicles which can adjust its altitude freely by changing the direction of propulsive forces and making the vehicle flexible when moving in the water with the ability to gather oceanographic data. According to the design purpose, the asymmetrical structure would be better for our underwater vehicle as described by [4].
II. METHODOLOGY
A. WMUSV Design
A framework for the design process of the WMUSV is shown in Fig. 1. It can be classified into several stages. The first stage concentrates on the design concept of the WMUSV. The next stages can be divided into two parts; the first part is the development of the mechanical structure. Thus, computer-aided software such as the SolidWorks software is used to draw and animate the WMUSV that are proposed and expected. Another part is the development of the internal and external electrical and electronic design of the WMUSV. The last stage is concluded with its testing, appraisal, and minor adjustment of the design project. The overall design flows of the design and development of WMUSV is shown in Fig. 1.
B. GENERAL DESIGN OF A WMSUV
It is compulsory or essential to have strong background knowledge, fundamental concepts and theory about the processes and physical laws governing the design of underwater robots and how they relate to locomotion in aquatic animals like fishes, sea turtles, and whales in its environment. To achieve this, there are several aspects in WMUSV electrical, electronic and mechanical design need to be looked at closely so that the design will be successful. Therefore, the major design aspects that need to be considered
[6] are identifying types of the material use in design the vehicle body, propulsion, immersing and electric power. Fig. 2 is the method that I using to design a WMSUV.
Fig. 2. Concepts of WMSUV
1) Vehicle Body Design: A WMUSV must provide a pressure body to house its components in a dry, watertight environment. The body must allow components to be easily accessible and maintainable, as well as allowing for modularity in case of future changes or additions [3]. As well as being light and strong, the body should also be corrosion resistant as it will be subjected to a harsh saltwater environment. The spherical body offers the best constructional honesty; however, the shape obstructs the efficient use of the space available as most components and systems are rectangular in shape. The oval rectangular body provides the best alternative for my design, comprising high structural integrity and shape conducive to the housing of electronic components.
2) Submerging: In the instance of an Immersible design vehicle, since the volume of the vehicle remains constant, for the vehicle to move deeper in the water, it must increase the downward force acting upon it, to oppose the buoyant force. It can achieve this either by increasing its mass of the vehicle body via the use of ballast tanks or by using external thrusters. Ballasting is the more common approach for immersing an object. This method is mostly mechanical and involves employing pumps and compressed
IJERTV9IS100247 www.ijert.org
Published by : International Journal of Engineering Research & Technology (IJERT)
http://www.ijert.org ISSN: 2278-0181
Vol. 9 Issue 10, October-2020
air to take in and remove water in the process. The alternative is to use thrusters that point downwards to support the vehicle. This is a much simpler system, but is quite inefficient in terms of power consumption and not suited at great depths. To reduce the size of ballast tanks or the force required by thrusters for the process of immersing, WMUSV is usually designed to have residual buoyancy, i.e. the weight of the designed vehicle is made to be more or less equal to the buoyant force.
3) Propulsion: Some sort of propulsion is required on all underwater vehicles and is usually one of the main sources of power consumption. Most underwater vehicles are use motors for propulsion due to the insufficiency and cost of substitute systems. The location of the thruster effects which degrees of freedom can be controlled. The positioning of the thruster can also affect noise obtrusion with onboard electronic components, as well as propeller to body and propeller to propeller interactions. Propeller to body and propeller to propeller interactions can have unwanted effects on the dynamics of underwater vehicles. When traveling at a constant speed, the thrust produced by the motors is equal to the friction or drag of the vehicle (1).
Where: . . is the water density
. s is the speed
. A is the effective surface area
. CD is the drag coefficient
The propulsion power consumption system increases desperately as the speed of the vehicle increases, because the thruster power is equal to the product of the thruster and the speed, meaning thruster power is a function of speed cubed (2).
Therefore, because a designed WMUSV has a limited energy supply with support of a solar panel to charge the Liteon batteries used to power the thruster for the vehicle. The vehicle must travel at a speed that does not extract too much power, but at the same time does not take too long to complete its mission. Obtaining the ideal speed becomes an optimization problem.
4) Electric Power: Electric power is commonly provided via sealed batteries with the support of electronics. The theoretical arrangement of batteries is to have them connected in parallel not to allow even discharge and to prevent current flow between batteries by putting diodes between each of the batteries. Other protective devices should also be used to prevent excessive current flow in case of short circuits occurring or components malfunctioning like fuse. The restrictive nature of power on design WMUSV influences the types of components and equipment that can be utilized. Electronic components and equipment should be chosen to draw as little power as possible to allow the batteries to provide more than enough time for the vehicle to complete its mission on the water.
III. RESULTS
The WMUSV can be designed in 3D by using computer-aided software and hence, the SolidWorks is 3D mechanical CAD (MCAD) software used for simulation and skeletal framework design. The software enables the user to play around to make any changes or modifications of the model a WMUSV. Actually, this design is finalized after a selected suitable and best design. Figure 4 is the WMUSV that design using SolidWorks software and using the given tools, the adjustment could easily handle. Simulation Project Information (iProperties) tables 1-15.
TABLE 1. PHYSICAL PROPERTIES OF PVC
MATERIALS USED IN DESIGN (WMUSV)
Mass 19.823 kg
Area 25448.715 mm^2
Volume 2525.227 mm^3
Center of Gravity x=-162.683 mm
y=-154.175 mm
z=-1.395 mm
TABLE 2. SIMULATION (GENERAL OBJECTIVE AND
SETTINGS)
Simulation Type
Static Analysis
TABLE 3. MATERIAL(S)
Name PVC-Piping
General Yield Strength 46.530 MPa
Ultimate Tensile Strength 52.360 MPa
Mass Density 1.400 g/cm^3
Stress Poisson’s Ratio 0.400 ul
Young’s Modulus 3.400 GPa
Part Name(s) ISO 21.3×2.0 00000001.ipt
TABLE 4. BEAM MODEL
Nodes 162
Beams 81
Round Tubes 81
TABLE 5. OPERATING CONDITIONS (GRAVITY)
Load Type Gravity
Magnitude 9810.000 mm/s^2
Direction Z
IJERTV9IS100247 www.ijert.org
Published by : http://www.ijert.org International Journal of Engineering Research & Technology (IJERT) ISSN: 2278-0181 Vol. 9 Issue 10, October-2020
TABLE 6. RIGID LINKS TABLE 10. OPERATING CONDITIONS (FORCE 6)
Name Displacemen t Rotation Parent Node Child Node(s)
X -axis Y -axis Z -axis X -axis Y -axis Z -axis
Rigid Link:1 fixed fixed fixed fixed fixed fixed Node:35 Node:161, Node:55
Rigid Link:2 fixed fixed fixed fixed fixed fixed Node:38 Node:150, Node:58
Rigid Link:3 fixed fixed fixed fixed fixed fixed Node:39 Node:155, Node:45
RigidLink:4 fixed fixed fixed fixed fixed fixed Node:42 Node:158, Node:48
Force:6
Load Type Force
Magnitude 10.000 N
Beam Coordinate System No
Angle of Plane 0.00 deg
Angle in Plane 180.00 deg
Fx 0.000 N
Fy 0.000 N
Fz -10.000 N
Offset 80.000 mm
TABLE 7. CROSS SECTION(S)
Geometry Properties Section Area (A) 121.265 mm^2
Section Width 21.300 mm
Section Height 21.300 mm
Section Centroid (x) 10.650 mm
Section Centroid (y) 10.650 mm
Mechanical Properties Moment of Inertia (I x ) 5706.905 mm^4
Moment of Inertia (I y ) 5706.905 mm^4
Torsional Rigidity Modulus (J) 11413.810 mm^4
Section Modulus (W x ) 535.860 mm^3
Section Modulus (W y ) 535.860 mm^3
Torsional Section Modulus (W z ) 1071.719 mm^3
Reduced Shear Area (A x ) 61.065 mm^2
Reduced Shear Area (A y ) 61.065 mm^2
TABLE 11. OPERATING CONDITIONS (FORCES 7-8)
Force:7-8
Load Type Force
Magnitude 10.000 N
Beam Coordinate System No
Angle of Plane 0.00 deg
Angle in Plane 180.00 deg
Fx 0.000 N
Fy 0.000 N
Fz -10.000 N
Offset 60.000 mm
TABLE 8. OPERATING CONDITIONS (FORCES 1-4)
Force:1-4
Load Type Force
Magnitude 10.000 N
Beam Coordinate System No
Angle of Plane 0.00 deg
Angle in Plane 180.00 deg
Fx 0.000 N
Fy 0.000 N
Fz -10.000 N
Offset 70.000 mm
TABLE 12. OPERATING CONDITIONS (FORCES 9-10)
Force:9-10
Load Type Force
Magnitude 35.000 N
Beam Coordinate System No
Angle of Plane 0.00 deg
Angle in Plane 180.00 deg
Fx 0.000 N
Fy 0.000 N
Fz -35.000 N
Offset 500.000 mm
TABLE 9. OPERATING CONDITIONS (FORCE 5)
Force:5
Load Type Force
Magnitude 10.000 N
Beam Coordinate System No
Angle of Plane 0.00 deg
Angle in Plane 180.00 deg
Fx 0.000 N
Fy 0.000 N
Fz -10.000 N
Offset 60.521 mm
TABLE 13. OPERATING CONDITIONS (FORCES 11-12)
Force:11-12
Load Type Force
Magnitude 15.000 N
Beam Coordinate System No
Angle of Plane 0.00 deg
Angle in Plane 180.00 deg
Fx 0.000 N
Fy 0.000 N
Fz -15.000 N
Offset 300.000 mm
IJERTV9IS100247 www.ijert.org
Published by : International Journal of Engineering Research & Technology (IJERT)
http://www.ijert.org ISSN: 2278-0181
Vol. 9 Issue 10, October-2020
TABLE 14. REACTION FORCE AND MOMENT ON CONSTRAINTS RESULTS
Constraint Name Reaction Force Reaction Moment
Magnitude Components (Fx,Fy,Fz) Magnitude Components (Mx,My,Mz)
Fixed Constraint:7 8.479 N -665.147 N mm
53.377 N 22.739 N 711.348 N mm 238.002 N mm
47.542 N -83.366 N mm
Fixed Constraint:6 9.466 N 710.184 N mm
62.264 N -24.417 N 786.444 N mm 324.754 N mm
56.490 N 93.099 N mm
Fixed Constraint:2 -10.030 N -630.858 N mm
63.739 N 22.513 N 733.625 N mm -358.013 N mm
58.781 N 109.778 N mm
Fixed Constraint:1 -7.997 N 696.731 N mm
54.399 N -22.336 N 747.496 N mm -250.553 N mm
48.952 N -102.656 N mm
Fixed Constraint:4 -5.161 N 699.519 N mm
52.958 N 34.615 N 920.349 N mm 479.947 N mm
39.746 N 356.883 N mm
Fixed Constraint:3 5.876 N -634.091 N mm
52.342 N -34.085 N 878.916 N mm 463.405 N mm
39.287 N -394.561 N mm
Fixed Constraint:8 5.372 N -664.052 N mm
52.717 N -34.153 N 901.389 N mm -493.081 N mm
39.796 N 358.340 N mm
Fixed Constraint:5 5.746 N 667.144 N mm
53.568 N 35.125 N 903.699 N mm -465.518 N mm
40.033 N -393.553 N mm
TABLE 15. STATIC RESULT SUMMARY
A. Skeletal Frame Work
Name Minimum Maximum
Displacement 0.000 mm 0.414 mm
Forces Fx -38.028 N 35.584 N
Fy -41.099 N 35.146 N
Fz -20.992 N 58.267 N
Moments Mx -3881.387 N mm 4156.414 N mm
My -3709.118 N mm 5707.585 N mm
Mz -1900.289 N mm 2777.495 N mm
Normal Stresses Smax -0.362 MPa 18.264 MPa
Smin -18.551 MPa 0.006 MPa
Smax(Mx) 0.000 MPa 7.757 MPa
Smin(Mx) -7.757 MPa -0.000 MPa
Smax(My) -0.000 MPa 10.651 MPa
Smin(My) -10.651 MPa 0.000 MPa
Saxial -0.480 MPa 0.173 MPa
Shear Stresses Tx -0.583 MPa 0.623 MPa
Ty -0.576 MPa 0.673 MPa
Torsional Stresses T -2.592 MPa 1.773 MPa
The initial structure of the design vehicle is making the mechanical parts mostly the skeletal frame using SolidWorks is 3D mechanical CAD (MCAD) software and made from PVC pipes materials, chosen especially for its lightweight characteristic as well as its resistance to corrosion which helps protect the vehicle against the harsh salt water and chlorine environment in which it is subjected to. Fig. 5 shown the maximum bending action point. Fig. 6 shown the maximum and minimum of moment forces action on WMUSV (Mx, My and Mz direction). Fig. 7 shown the maximum and minimum of normal stress acting on WMUSV. Fig. 8 shown the maximum and minimum of bending stress acting on WMUSV Smax (Mx). Fig. 9 shown the maximum and minimum of axial stress (Saxial) and torsional stress (T) acting on WMUSV. Fig. 10 shown the maximum and minimum of shear stress (Ty and Tx) acting on WMUSV. Fig. 11 shown deformation of stress analysis at bottom of WMUSV. Fig. 12 shown deformation of stress analysis at towards the back of WMUSV. Fig. 13 shown strain analysis at 100m below the water surface. Fig. 14 shown the effect of surface pressure on WMUSV at 0m depth. Fig. 15 shown the effect of Pressure on WMUSV at 100m depth. Fig. 16 shown the estimated level at which the WMUSV remains buoyant when M = 45kg. Fig. 17 shown the part of the WMUSV that displaces enough Water in order to Achieve Buoyancy (3). Fig. 18 shown buoyancy level when M = 66.8kg by increasing the water inside the two tanks
(4) and (5). Fig. 19 shown the submerged part of the WMUSV when buoyancy is reached (6) and (7). As well as supporting the two tanks for buoyancy control and four motors for upward and downward motion, the structure of the frame allows for the simple mounting of external devices and components. The design took into account the possible need for additional components in the later and for that reason enough space is available on the frame. The regularly and skeletally simple nature of the frame design contributed to the relatively uncomplicated position of the thrusters with the centers of drag for increased dynamic stability. Also, the nature of the frame also allowed the thrusters to be easily mounted in positions where they would minimize potential magnetic interference with onboard electronic devices.
Fig. 4. Shows the complete side view of the WMUSV using SolidWorks is 3D mechanical CAD (MCAD) software.
Where:
.
is Buoyancy force
.
is Volume of displaced fluid
.
is gravity =9.8m/s
.
is density of the sea water = 1025kgm3
Where:
.
is Mass of pumped water
.
is density of the sea water = 1025kgm3
.
is Volume of water =0.02125
IJERTV9IS100247 www.ijert.org
Published by : International Journal of Engineering Research & Technology (IJERT)
http://www.ijert.org ISSN: 2278-0181
Vol. 9 Issue 10, October-2020
Where:
.
is Total mass of the vehicle after water intake
.
is Mass of the vehicle
.
is Mass of pumped water
Where:
.
is Total mass of the vehicle after water intake
.
is Mass of the vehicle
.
is density of the sea water = 1025kgm3
Therefore, the force needed to keep the vehicle upward thrust stable is
. Fig. 6. Shown the Maximum and Minimum of Moment Forces action on UWV (Mx, My and Mz direction) of (4156Nmm, -3881Nmm), (5708Nmm, -3709Nmm) and (2777Nmm, -1900Nmm) A, B and C respectively
Fig. 7. Shown the Maximum and Minimum of Normal Stress acting on WMUSV (Smax between -0.36 Mpa to 18.26 MPa) and (Smin between -18.55MPa to 0.01MPa) for A and B respectively
IJERTV9IS100247 www.ijert.org
Published by : International Journal of Engineering Research & Technology (IJERT)
http://www.ijert.org ISSN: 2278-0181
Vol. 9 Issue 10, October-2020
Fig. 10. Shown the Maximum and Minimum of Shear Stress (Ty and Tx) acting on WMUSV (Ty) between -0.5755 Mpa to 0.673 Mpa and (Tx) between -0.5827 MPa to 0.6227 MPa) A and B respectively
IJERTV9IS100247 www.ijert.org
Published by : International Journal of Engineering Research & Technology (IJERT)
http://www.ijert.org ISSN: 2278-0181
Vol. 9 Issue 10, October-2020
IJERTV9IS100247 www.ijert.org
Published by : International Journal of Engineering Research & Technology (IJERT)
http://www.ijert.org ISSN: 2278-0181
Vol. 9 Issue 10, October-2020
B. WMUSV Dimension
Figure 20 Shown the First Angle Projection and Dimensioning of design Wireless Mobile Underwater and Surface Vehicle (WMUSV). Figure 22 shown the layout of component outside the design WMUSV. Once the skeletal frame of a WMUSV is done, the next process is the fiber process. The designed vehicle has 6 degrees of freedom motion simulators control using rotational matrixes. Three spatial coordinates, x, y and z; and three attitude defining Euler angles which is the rotation angle about the three Cartesian axes, roll (f) pitch (.) and yaw (.) Fig. 21.
Fig. 22. Layout of Component Outside the Design WMUSV
C. Fibre-reinforced plastics (FRP)
Once the skeletal frame of a WMUSV is done, the next process is the fiber process. Fig. 23. shown the process of the skeletal frame made up of PVC pipe enclosed with fiber-reinforced plastics to make the desired design following the design using the software. Fig. 24. shows the hardware of WMUSV that the finalized result for the design and construction of a WMUSV. The control device is functioned as well as the project expected. The thrusters for the vehicle work well controlled by manual and auto controller. It just for rotate clockwise and anticlockwise for WMUSV moving forward, backward, upward, and downward.
IJERTV9IS100247 www.ijert.org
Published by : International Journal of Engineering Research & Technology (IJERT)
http://www.ijert.org ISSN: 2278-0181
Vol. 9 Issue 10, October-2020
B.E
IV.
C.
Fig. 24. The Hardware of WMUSV that the Finalized Result for the Design and Construction of a WMUSV
IV. FACTORS AFFECTING WMUSV PERFORMANCES
The various forces act on an underwater vehicle that needs to be considered for better performances. These include an increase in the mass of the vehicle, environmental factors and water pressure. The pressure is another important factor for underwater vehicles that need to be taken into deliberation in the design process.
A. Increase in the Mass
The first phenomenon that affects underwater vehicles is to increase the mass of the vehicle. When a body of the vehicle moves underwater, the immediate surrounding fluid speeds up along with the body of the vehicle. This affects the dynamics of the vehicle in such a way that the force required to speed up the water can be modeled as increasing the mass. Increase the mass is a fairly significant effect and is related to the mass and inertial values of the design underwater vehicle.
B. Environmental Forces
Environmental distraction can affect the motion and stability of a design underwater vehicle. This is particularly true for an underwater vehicle where water turbulent, ocean waves, ocean currents, and even wind can upset the underwater vehicle. Especially, when the vehicle is immersed, the effect of ocean wind and waves can be largely ignored. The most important upset then for underwater vehicles are ocean currents. Using the pool, we can control environment forces and the effect of these environmental forces is minimal.
C. Pressure
As with air, underwater pressure is occurred by the weight of the medium, in this case, water acting upon a surface. The pressure is usually estimated as an absolute or ambient pressure that is, absolute implies the total pressure and ambient being of a relativistic nature. At sea level, pressure due to air is 14.7 psi or 1 atm. For every 10m of depth, pressure increases by about 1atm, and hence, the absolute pressure at 10m underwater is 2 atm. The increase in pressure as depth increases is significant and underwater vehicles must be structurally capable of withstanding a relatively large amount of pressure if they are to survive.
V. CONCLUSION
This study has shown the mechanical and electrical structures of the project have been well discussed and shown in above. After that, the research result and problem finding also have been described. Therefore, based on the research made, a brief project conclusion of the development process and the design of the actual WMUSV are given. Wireless Mobile Underwater and Surface Vehicle for Hydrological
Parameters Monitoring (WMUSVHPM) are robotic submarines. They are a part of the emerging field of autonomous and unmanned vehicles and are primarily used as low-cost reconnaissance tools. WMUSV are valued for both them expand ability and replace ability; they can be deployed in hazardous environments without risking human divers.
Economically, the potential for cheap scalability makes WMUSV ideal for large scale and long-term data collection tasks. This research aims to design and construct an WMUSV as a test bed platform for a variety of research in underwater technologies especially involving small-scale and low-cost underwater robots. The prototype that will be developed will have a fixed mechanical system, having a modular electronic system that allows development of various controllers, recording devices, sensors module and internet facilities for archive hydrological data.
It also can be used for testing and learning conventional and advanced control algorithms and techniques to other underwater systems. With a limited budget a small WMUS vehicle has been developed. The mechanical structure is
IJERTV9IS100247 www.ijert.org
Published by : International Journal of Engineering Research & Technology (IJERT)
http://www.ijert.org ISSN: 2278-0181
Vol. 9 Issue 10, October-2020
produced. Future development and improvement with show that this compared to other autonomous and unmanned vehicles (AUVs) projects, smaller and cheaper concept will succeed.
REFERENCES
[1] Alam, K., Ray, T. and Anavatti, S. G. (2014). “Design and Construction of an Autonomous Underwater Vehicle,” Neuro Computing, no. 142, pp. 16-19, 2014.
[2] Duchemin, O., Lorand, A., Notarianni, M., Valentian, D. & Chesta,
E. (2007). Multi-Channel Hall-Effect Thrusters: Mission Applications and Architecture Trade-Offs, 30th International Electric Propulsion Conference, Florence, Italy.
[3] Gonzalez L.A., “Design, Modelling and Control of an Autonomous Underwater Vehicl,” Bachelor of Engineering Honours Thesis, The University of Western Australia, 2004.
[4] Guo, S., Lin, X. & Hata, S. (2009). A Conceptual Design of Vectored Water-jet Propulsion System, International Conference on Mechatronics and Automation, 2009. ICMA 2009, IEEE, pp.1190-1195.
[5] Jianguo Wu, Chaoying Chen and Shunxin Wang, Hydrodynamic Effects of a shroud Design For a Hybrid-Driven Underwater Glider,Sea Technology,2010, Vol.51, No.6,pp.45-47
[6] Hsu S., Mailey C., Montgomery C., Moody R., “Autonomous Underwater Vehicle— “Camera” ,” Duke & NC state university.
[7] Lazic, D. & Ristanovic, M. (2007). Electro-hydraulic Thrust Vector Control of Twin Rocket Engines with Position Feedback via Angular Transducers, Control Engineering Practice 15(5): 583–594.
[8] Miller, T. F., Gandhi, F. S. and Rufino, R. J. (2014). “Morphing Hull Concept for Underwater Vehicles,” Ocean Engineering, no. 92, p. 92–102, 2014.
[9] Puzai, N. M., Ayob, A. F. and Arshad M. R. (2016). A Review on Recent Advancements in Unmanned Underwater Vehicle Design Journal of Ocean, Mechanical and Aerospace 2016 -Science and Engineering-, Vol.31.
[10] Sangekar, M., Chitre, M. & Koay, T. (2009). Hardware Architecture for a Modular Autonomous Underwater Vehicle STARFISH, OCEANS 2008, IEEE, pp. 1–8.
[11] Sgarioto, D. and Madden, C. (2014). “Full-scale maneuvering trials for the Wayamba Unmanned Underwater Vehicle,” Underwater Technology, vol. 32, no. 2, pp. 67-79, 2014.
IJERTV9IS100247 www.ijert.org