
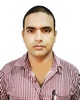
- Open Access
- Authors : Raja Azad Kumar Mishra , Prof. Ashok Kumar Mahapatra , Amit Goshwami
- Paper ID : IJERTV9IS020189
- Volume & Issue : Volume 09, Issue 02 (February 2020)
- Published (First Online): 29-02-2020
- ISSN (Online) : 2278-0181
- Publisher Name : IJERT
- License:
This work is licensed under a Creative Commons Attribution 4.0 International License
Energy Management in Grid Connected Photovoltaic System
Raja Azad Kumar Mishra, Prof. Ashok Kumar Mahapatra , Amit Goshwami
K. K. University Beraunti, Nalanda, Bihar,
Abstract:- The use of renewable energy sources is increasing and will play an important role in the future power systems. The unpredictable and uctuating nature of solar power leads to a need for energy storage as the prevalence increases.
A ve parameter model of PV modules has been implemented in Simulink/Matlab. The parameters of the model are determined by an approximation method using data sheet values. Inputs to the model include light intensity and ambient temperature. The outputs are any measurements of interests as well as power, current and voltage. A maximum power point tracking algorithm is used to keep the voltage at the maximum power point at all times. utilization of a boost converter for control of photovoltaic power using Maximum Power Point Tracking (MPPT) control mechanism is presented. The Perturb and Observe algorithm utilized for MPPT is a generalized algorithm and is easy to model or use as a code. A battery storage system based on li-ion battery is connected with the photovoltaic plant to store the extra energy generated and/or to fulfil the requirement of the connected load at the time of any discontinuity of the grid supply or any load changes in the grid system. The PV plant with MPPT controller and boost converter is integrated into the AC utility grid by DC/AC inverter to control the active and reactive powers for the desired power factor at the connection point.
This work deals with the management of Energy Storage System connected in a microgrid with a PV array and regulate the battery charge, hold and discharge operations using DC-DC bidirectional converter based on the requirement of the Load. The PV array along with the battery and load is simulated for various conditions such as PV supplying and charging the battery, PV supplying only the load, battery supplying the load and PV-Battery both supplying the load. In this dissertation, different cases are simulated, and the results have verified the validity of models and control schemes.
Keywords:- Photovoltaic system; Boost converter; Maximum power point tracking; PI control; Battery storage system; Energy management
Chapter-1 INTRODUCTION
One of the major concerns in the power sector is the day- to-day increasing power demand but the unavailability of enough resources to meet the power demand using the conventional energy sources. Demand has increased for renewable sources of energy to be utilized along with conventional systems to meet the energy demand. Renewable sources like wind energy and solar energy are the prime energy sources which are being utilized in this regard. The continuous use of fossil fuels has caused the fossil fuel deposit to be reduced and has drastically affected
the environment depleting the biosphere and cumulatively adding to global warming.
Solar energy is abundantly available that has made it possible to harvest it and utilize it properly. Solar energy can be a standalone generating unit or can be a grid connected generating unit depending on the availability of a grid nearby. Thus it can be used to power rural areas where the availability of grids is very low. Another advantage of using solar energy is the portable operation whenever wherever necessary.
In order to tackle the present energy crisis one has to develop an efficient manner in which power has to be extracted from the incoming solar radiation. The power conversion mechanisms have been greatly reduced in size in the past few years. The development in power electronics and material science has helped engineers to come up very small but powerful systems to withstand the high power demand. But the disadvantage of these systems is the increased power density. Trend has set in for the use of multi-input converter units that can effectively handle the voltage fluctuations. But due to high production cost and the low efficiency of these systems they can hardly compete in the competitive markets as a prime power generation source.
The constant increase in the development of the solar cells manufacturing technology would definitely make the use of these technologies possible on a wider basis than what the scenario is presently. The use of the newest power control mechanisms called the Maximum Power Point Tracking (MPPT) algorithms has led to the increase in the efficiency of operation of the solar modules and thus is effective in the field of utilization of renewable sources of energy [3], [8].
-
Context and Perspective
Emissions of CO2 and other greenhouse gasses are leading to climate change [23]. The greenhouse eect of CO2 is well understood and it is clear that the emissions must be reduced to avoid undesirable scenarios. To reverse the trend, there is a great need for accelerating the development and implementation of renewable energy technologies.
Use of renewable energy sources is rising at an increasing rate. The global PV capacity is escalating rapidly with an average annual growth for the last decade of 40% [24]. In gure the development of total capacity up to year 2008 is shown. Predictions by IEA state that this trend will continue and that photovoltaics will provide 11% of the global electricity generation by 2050 [24]. Output from PV systems can change rapidly because of cloud movements
and other factors. If these systems are prevalent enough in a power system, problems with voltage and frequency control can arise [26]. On-site energy storage can be used to mitigate these issues.
Both photovoltaic energy and energy storage systems will play a major role in the future energy system. Energy storage technologies was the main theme in the specialization project [30].
Figure 1.1: Global cumulative installed PV capacity from 1992 to 2008 [24]
1.1.1 Status of renewable energy in India
In the present scenario, renewable resources emerge as the best alternative. At present, renewable energy accounts for about 11% of India's installed generation capacity of 152 GW. Much of this capacity is wind-based (about 11 GW), with the share of solar power being only about 6 MW.
India is blessed with an abundance of non-depleting and environmentally friendly renewable resources, such as solar, wind, biomass, hydro and cogeneration and geothermal. Wind energy sector, which has shown tremendous growth in the recent year, dominates the renewable energy sector in India.
Table 1.1: Status of renewable energy in India
India has an abundance of solar radiation, with the peninsula receiving more than 300 sunny days in a year. PV is progressively becoming more attractive, than other renewable sources of power, as its cost declines. The various factors leading to decline in cost includes setting up of large scale plants, integration across the value chain, declining cost of raw material, reducing material consumption and higher efficiency of modules.
Due to its proximity to the equator, India receives abundant sunlight throughout the year. Solar PV solution has the potential to transform the lives of 450 million people, who rely on highly subsidized kerosene oil and other fuels, primarily to light up their homes. Renewable energy source is a practical solution to address the persistent demand supply gap in the power industry. The following features of solar power make it the most viable renewable source of energy for India:
-
Solar energy is available in abundance.
-
Available across the country unlike other renewble sources, which have geographical limitations.
-
Available throughout the year.
-
Decentralized / off-grid applications addressing rural electrification issues.
-
Modularity and scalability.
The PV approach is particularly suited for the geographical and socio-economic features of this country having highly skewed energy distribution between urban and rural areas.
-
-
Problem Description
A simulation model of a general photovoltaic module is to be constructed in Simulink. The inputs to the model should be solar irradiance and ambient temperature. It must be able to operate at the maximum power point to compare the output to measured values with the help of MPPT controller with Perturb and Observe algorithm.
The battery system with the voltage source inverter is to be fed to the AC grid and energy management for the power flow must be done as per the requirement of the system.
-
Literature Review
Several works are going on solar photovoltaic systems. Some of these are discussed below:
Prakasit Sritakaew, Anawach Sangswang, and Krissanapong Kirtikara [1] presented a paper about On the Reliability Improvement of Distribution Systems Using PV Grid-Connected Systems. The purpose of their paper was to examine issues related to the distribution system reliability improvement using photovoltaic (PV) grid- connected systems. The output characteristics of a PV system were experimentally measured. The measured data were used to investigate the effects of PV system installation to improve the distribution system's reliability. The system constraints such as, recovered real power, and loading reduction of the tie line/switch after the installation of PV grid-connected systems are concentrated. Simulation results show that with the action of a tie switch, system losses and loading level of the tie switch can be reduced with proper installation location.
Allen M. Barnett [2] presented a paper about solar electrical power for a better tomorrow. The promise of
solar electricity based on the photovoltaic (PV) effect is well known. Why dont we see these systems all over the world? Consumers in the United States are well-known for their attraction to new technology. Why arent PV systems appearing on roof-tops in the U.S.? The answer may be that grid-connected roof top systems are Too difficult to acquire, Too difficult to integrate with the grid, Too difficult to measure the energy and Too expensive .It is essential that we make PV systems user friendly, while reducing the component and system costs. Our elegant technology must be reduced to practical systems that can be used by the average person – everywhere.
R. Ramkumar & J. E. Bigger [3] presented a paper of photovoltaic systems including a discussion of major U.S. and international activities. After a brief review of system types and output characteristics, various system configurations were discussed and a classification based on photovoltaic (PV) system rating was provided. Modeling, design, and economic Considerations were briefly discussed. The worldwide status of PV system technology was discussed with a view to making an assessment of the future. The assessment presented includes some specific areas for further research and development. Although no major technical barriers are evident the entry of PV, as the level of penetration increases, several key issues identified in this paper will need further consideration. Photovoltaics is still evolving and has not reached its full potential. It is likely to grow for decades to come; however, the rate of growth may depend on several exogenous factors such as cost of conventional energy sources and the peoples desire to improve the global environment.
G. Ofualagba [4] in his paper first explained the reasons for the mounting interest in photovoltaic technology and has provided a quick synopsis of the operation of these technology and their applications and markets. Photovoltaic technology have received increasing attention over the last decade as one response to the challenges of global warming, increasing demand for energy, high fuel costs, and local pollution. This paper describes photovoltaic systems (PV modules, batteries, power conditioning, generators, and pumps) and discusses the photovoltaic markets including on-grid, off grid and water pumping applications N. Jenkins [5] presented a paper about Photovoltaic systems for small-scale remote power supplies. In his article, he considers the technical aspects of using photovoltaic systems for small power supplies where a connection from a main electricity distribution network is not appropriate. The technology of the various components of a photovoltaic system is discussed and the overall system design considered. Typical applications of photovoltaic systems are described.
Souvik Ganguli & Sunanda Sinha [6] presented a paper about Estimation of Grid Quality Solar Photovoltaic Power Generation Potential and its Cost Analysis in Some Districts of West Bengal. The objective of their work was to estimate the potential of grid quality solar photovoltaic power in some districts of West Bengal (Birbhum, Burdwan, Hooghly, Howrah and Kolkata), study the solar radiation level and potential of the above mentioned districts and finally develop a system corresponding to the
potential. Equipment specifications were provided based on the system developed and finally cost analysis was also carried out.
Brig.M.R.Narayaoan, D.V.Gupta, R.C.Gupta & R.S.Gupta
[7] presented a paper about Design, Development and Installation of 100 kW utility grid connected solar PV plants for rural application- an Indian experience. This paper briefly describes tile features of the two power plants, the developmental approach adopted based on "Building Block Philosophy" With 25 KW System as the basic unit with the attendant advantages. It includes the indigenous design and development effort made for grid connected operation and most importantly the special design features incorporated to ensure a very high degree of safety and protection so necessary in the rural areas with predominantly non-literate users. Tile paper is concluded with some important lessons learnt from both the technical and logistics point of view for guiding installation of similar such plants in the remote rural areas in India and other developing countries in the future.Wang Jianqiang & Li Jingxin [8] researched two grid connected photovoltaic power systems. One is 10kW located in Beijing, the other is 100kW located in north of Shanxi province of China. Inverter and its different operation of modes for both the photovoltaic power system were discussed. For 10kW Photovoltaic power system, the single phase transformers less grid-connecting inverters are applied to this system. The inverters have two-stage structure, DCDC and DC-AC, but they often operates only with last DC-AC stage according to the panel string output voltage. For 100kW photovoltaic power system, 3 phase transformer less gridconnecting inverters are used. But they concluded that although all the inverters in two systems have two stage structures, only single stage were designed to work during most of time. Because the system efficiency can be increased availably. So large photovoltaic power system should adopt series-wound panels for high operating voltage and less loss. The research shows the correlation. The output power quality of one inverter of 10kW systems was analyzed, too.
B. Marion,J. Adelstein,K. Boyle and fellows [9] presented a paper about performance parameters for Grid-Connected PV systems. Three performance parameters may be used to define the performance of grid-connected PV systems: final PV system yield Yf, reference yield Yr, and performance ratio PR. The Yf and PR are determined using the nameplate d.c. power rating. The Yf is the primary measure of performance and is expressed in units of kWh/kW. It provides a relative measure of the energy prodced and permits comparisons of PV systems of different size, design, or technology. If comparisons are made for different time periods or locations, it should be recognized that year-to-year variations in the solar resource will influence Yf. The PR factors out solar resource variations by dividing Yf by the solar radiation resource, Yr. This provides a dimensionless quantity that indicates the overall effect of losses and may be used to identify when operational problems occur or to evaluate long-term changes in performance. As part of an operational and
maintenance program, the PR may be used to identify the existence of performance issues.
Chang Ying-Pin & Shen Chung-Huang [10] presented a paper about Effects of the Solar Module Installing Angles on the Output Power. In their paper they discussed that the output power increment of photovoltaic cells is mainly based on two factors. One is decreasing the cell modular temperature and the other is increasing the cells received solar illumination intensity. The former can be simply achieved by maintaining a proper radiating space between the modules and the ground. The later is more complicated. One needs to consider the installation of cell modules and then the maximum power output which can be derived. This paper was theoretically calculated the solar orbit and position at any time and any location. With the estimation of their model on the variation of solar illumination intensity, they can derive the output power of the solar modular cell at any tilt angle and orientation. The simulated results could be utilized in large scale photovoltaic power generation systems when considering placement for optimal installation. It also provides a useful evaluation for the output power of photovoltaic cells mounted on roofs and out walls of buildings. Several grid connected photovoltaic system topologies are used in existing installations.
D.Picault, B. Raison , and S. Bacha [11] presented a paper about proposes evaluation criteria for comparing and choosing topologies compatible with the users demands. After presenting an overview of current architectures used in grid connected systems, five key points for comparison based on topology upgradeability, performance under shaded conditions, degraded mode operation, investment costs and ancillary service participation were discussed. The proposed method can be adapted to the user's particular needs and expectations of the photovoltaic plant. These evaluation guidelines may assist grid-tied PV system users to choose the most convenient topology for their application by weighting the evaluation criteria.
Jinhui Xue , Zhongdong Yin , Qipeng Song, and Renzhong Shan [12] presented a paper about analyze and research of the inverter for Grid connecting photovoltaic system. In their paper the described the Topology of main circuit, control methods, design of passive filter. The important point of their paper was control methods for grid- connecting, PFC, control methods of power direction. Based on the analyzing of SPWM (sinusoidal pulse-width- modulated) technique control method in detail, this paper improves the control means. This paper proposes a neoteric grid-connecting inverter, which synchronizes a sinusoidal AC output current with a utility line voltage, and control the power generation of each photovoltaic battery cell.
Phil Bolduc, David Lehmicke & Joseph Smith [13] presented a paper about performance of a grid connected PV system with energy storage. One kilowatt amorphous photovoltaic system has been operated in a grid-connected mode with energy storage. The purpose of the system development and performance experiment is to investigate the additional value a gridconnected system garners with dispatchable battery energy storage. These values are then weighed against the added cost of the system and
inefficiencies incurred in the charging and discharging of the battery.
Eduardo Román, Ricardo Alonso & Pedro Ibañez [14] presented the paper about the intelligent PVmodule concept, a low-cost high-efficiency dcdc converter with maximum power point tracking (MPPT) functions,control, and power line communications (PLC). In addition, they analyzed the alternativesfor the architecture of grid connected PV systems: centralized, string, and modular topologies. The proposed system, i.e., the intelligent PV module, fits within this last group. Its principles of operation, as well as the topology of boost dcdc converter, are analyzed. Besides, a comparison of MPPT methods is performed, which shows the best results for the incremental conductance method. Regarding communications, PLC in every PV module and its feasibility for grid-connected PV plants are considered and analyzed in this paper. After developing an intelligent PV module (with dcdc converter) prototype, its optimal performance has been experimentally confirmed by means of the PV system test platform. This paper describes this powerful tool especially designed to evaluate all kinds of PV systems.
Grid-connected PV plants, aimed at delivering energy to the grid. However, the cost/kWh of PV energy is still quite high. V. Lughi , A. Massi Pavan , S. Quaia , and G. Sulligoi [15] reported some of the most promising research approaches currently in progress on new PV materials and devices , focusing on the reduction of PV generation cost expected from the technological implementation of such research. Their paper reported the main features and the expected economical effect of two of these researches: the first regards the use of cadmium telluride thin films, the second concerns the development of novel nanostructured PV materials. Large size industrial PV plants could have different characteristics compared to the small ones that, with few exceptions, have been realized until now. The analysis performed in this paper suggests to recommend centralized power electronic conditioning systems together with the use of proper simulation-aided design tools.
Kosuke Kurokawa, Kazuhiko Kato , Masakazu Ito, Keiichi Komoto, Tetsuo Kichim, & Hiroyuki Sugihara [16] presented paper about the cost analysis of very large scale PV system on the world desert. a 100 MW very large scale photovoltaic power generation (VLS-PV) system was estimated assuming that it is installed on the would deserts, which are Sahara, Negev, Thar, Sonora, Great Sandy and Gobi desert. PV array was dimensioned in detail in terms of array layout, support, foundation, wiring and so on. Then generation Cost of the system was estimated based on the methodology of Life-Cycle Cost (LCC). As a result of the estimation, the generation cost was calculated.
M. C. Cavalcanti, G. M. S. Azevedo and fellows [17] presented paper which introduces a comparative study of efficiency for topologies in photovoltaic energy conversion systems. In special, a study of losses was presented and the methodology was used to compare different topologies for grid connected photovoltaic systems in such a way that can be chosen the option of best efficiency. The systems were also tested with photovoltaic generation as well as current harmonic and reactive power compensation
simultaneously. Using the loss models, it is possible to estimate efficiency and to make a comparative study of different conversion systems.
M.J. de Wild-Scholten, E.A. Alsema, E.W. ter Horst &
V.M. Fthenakis [18] presented a paper about a cost and environmental impact comparison of grid connected rooftop and groundbased PV systems. The environmental impact and total system costs have been investigated for roof-top and ground-based crystalline silicon PV systems by using environmental and cost life cycle assessment. Greenhouse gas emissions and other environmental impacts from Balance-OfSystem components are relatively small, in comparison with present-day modules. Frameless laminates are largely preferred from an environmental point of view; the extra impacts from a somewhat heavier mounting structure are more than compensated by the avoided impacts of the frames. In-roof sstems clearly have a lower environmental impact of the Balance-of-System components in comparison to on-roof and ground-based systems.
Evert Nieuwlaar & Erik Alsema [19] gives us idea about environmental aspects of PV power systems. During normal operation, photovoltaic (PV) power systems do not emit substances that may threaten human health or the environment. In fact, through the savings in conventional electricity production they can lead to significant emission reductions. There are, however, several indirect environmental impacts related to PV power systems that require further consideration. The production of present generation PV power systems is relatively energy intensive, involves the use of large quantities of bulk materials and (smaller) quantities of substances that are scarce and/or toxic. During operation, damaged modules or a fire may lead to the release of hazardous substances. Finally, at the end of their useful life time PV power systems have to be decommissioned, and resulting waste flows have to be managed.
José L. Bernal-Agustà & Rodolfo Dufo-López [20] presented a paper about Economical and Environmental Analysis of Grid Connected Photovoltaic Systems in Spain. In this article an economic and environmental study was carried out on PV solar energy installations connected to the Spanish electrical grid system. First fall, an economical study was performed, proposing different scenarios where different values of interest rate and energy tariffs were considered. The following parameters were used to determine the profitability of a PV installation. The Net Present Value and the Pay-Back Period. Furthermore, the environmental benefits of PV systems connected to the grid have been evaluated.
-
Aims and Objectives
The basic objective would be to study Energy management in the Grid connected PV system with the MPPT Controller and successfully implement the MPPT algorithms either in code form or using the Simulink models. Modelling the voltage source converter and the solar cell in Simulink, interfacing both with the MPPT algorithm to obtain the maximum power point operation and connecting the PV system with the AC grid would be of prime importance.
-
Outline of Dissertation
This thesis has been broadly divided into 7 chapters.
The first one being the introduction. Furthermore, it tells about the context and perspective, aims and objectives, problem description.
Chapter 2 is on Photovoltaic technology and PV cells and its types. In addition, it justifies PV module performance curves and elements included in a PV system.
Chapter 3 deals with the maximum power point tracking and study of the various algorithms as well as operation of MPPT controller to be used in the project.
Chapter 4 is on modelling of Grid connected PV system and other sub components included in it.
In chapter 5, the simulation models are presented that are used for various simulations.
Chapter 6 consists of all the simulation outputs. Conclusion and future work are listed in chapter 7.
CHAPTER- 2 PHOTOVOLTAIC TECHNOLOGY
Photovoltaic's offer consumers the ability to generate electricity in a clean, quiet and reliable way. Photovoltaic systems are comprised of photovoltaic cells, devices that convert light energy directly into electricity. Because the source of light is usually the sun, they are often called solar cells. The word photovoltaic comes from photo meaning light and voltaic which refers to producing electricity. Therefore, the photovoltaic process is producing electricity directly from sunlight. Photovoltaic are often referred to as PV.
2.1 Photovoltaic Cells
A device that produces an electric reaction to light, producing electricity. PV cells do not use the sun's heat to produce electricity. They produce electricity directly when sunlight interacts with semiconductor materials in the PV cells.
Figure 2.1: Photovoltaic cell
A typical PV cell made of crystalline silicon is 12 centimeters in diameter and 0.25 millimeters thick. In full sunlight, it generates 4 amperes of direct current at 0.5 volts or 2 watts of electrical power [25].
-
Basic theory of photovoltaic cell
Photovoltaic cells are made of silicon or other semi conductive materials that are also used in LSIs and transistors for electronic equipment. Photovoltaic cells use two types of semiconductors, one is P-type and other is N- type to generate electricity [27].
When sunlight strikes a semiconductor, it generate pairs of electrons (-) and protons (+).
Figure 2.2: Basic theory of photovoltaic cell 1
When an electron (-) and a proton (+) reach the joint surface between the two types of semiconductors, the former is attracted to N-type and the latter to the P-type
semiconductor. Since the joint surface supports only one way traffic, they are not able to rejoin once they are drawn apart and separated.
Figure 2.3: Basic theory of photovoltaic cell 2
Since the N-type semiconductor now contains an electron (-), and P-type semiconductor contains a proton (+), an electromotive (voltage) force is generated. Connect both
electrodes with conductors and the electrons runs from N- type to P-type semiconductors, and the proton from P-type to N-type semiconductors to make an electrical current.
Figure 2.4: Basic theory of photovoltaic cell 3
-
Series and parallel connection of PV cells
Solar cells can be thought of as solar batteries. If solar cells are connected in series, then the current stays the same and the voltage increases [27].
Figure 2.5: Series connection of cells
If solar cells are connected in parallel, the voltage stays the same, but the current increases.
Figure 2.6: Parallel connection of cells
As we know those Solar cells are combined to form a module to obtain the voltage and current (and therefore power) desired.
-
Types of Photovoltaics cells
There are essentially two types of PV technology, crystalline and thin-film. Crystalline can again be broken down into two types:
-
Monocrystalline Cells – These are made using cells cut from a single cylindrical crystal of silicon. While monocrystalline cells offer the highest efficiency (approximately 18% conversion of incident sunlight), their complex manufacturing process makes them slightly more expensive.
-
Polycrystalline Cells – These are made by cutting micro- fine wafers from ingots of molten and recrystallized silicon. Polycrystalline cells are cheaper to produce, but there is a slight compromise on efficiency (approximately 14% conversion of incident sunlight).
Thin film PV is made by depositing an ultra thin layer of photovoltaic material onto a substrate. The most common type of thin-film PV is made from the material a-Si (amorphous silicon), but numerous other materials such as CIGS (copper indium/gallium diselenide) CIS (copper indium selenide), CdTe (Cadmium Teluride), dye- sensitized cells and organic solar cells are also possible.
-
Photovoltaic modules
PV cells are the basic building blocks of PV modules. For almost all applications, the one-half volt produced by a single cell is inadequate. Therefore, cells are connected together in series to increase the voltage. Several of these series strings of cells may be connected together in parallel to increase the current as well. These interconnected cells and their electrical connections are then sandwiched between a top layer of glass or clear plastic and a lower level of plastic or plastic and metal. An outer frame is
attached to increase mechanical strength, and to provide a way to mount the unit. This package is called a "module" or "panel". Typically, a module is the basic building block of photovoltaic systems. PV modules consist of PV cells connected in series (to increase the voltage) and in parallel (to increase the current),so that the output of a PV system can match the requirements of the load to be powered. The PV cells in a module can be wired to any desired voltage and current. The amount of current produced is directly proportional to the cell's size, conversion efficiency, and the intensity of light.
-
Photovoltaic Module Performance
To insure compatibility with storage batteries or loads, it is necessary to know the electrical characteristics of photovoltaic modules. As a reminder, "I" is the abbreviation for current, expressed in amps. "V" is used for voltage in volts, and "R" is used for resistance in ohms.
-
The standard V-I characteristic curve of Photovoltaic Module
A photovoltaic module will produce its maximum current when there is essentially no resistance in the circuit. This would be a short circuit between its positive and negative terminals. This maximum current is called the short circuit current, abbreviated I(sc). When the module is shorted, the voltage in the circuit is zero.
Conversely, the maximum voltage is produced when there is a break in the circuit. This is called the open circuit voltage, abbreviated V(oc). Under this condition the resistance is infinitely high and there is no current, since the circuit is incomplete [28]. These two extremes in load resistance, and the whole range of conditions in between them, are depicted on a graph called a I-V (current-voltage) curve. Current, expressed in amps, is on the vertical Y-axis. Voltage, in volts, is on the horizontal X-axis as in Figure.
Figure 2.7: The standard V-I characteristic curve of Photovoltaic Module
As you can see in above Figure, the short circuit current occurs on a point on the curve where the voltage is zero. The open circuit voltage occurs where the current is zero. The power available from a photovoltaic module at any point along the curve is expressed in watts. Watts are calculated by multiplying the voltage times the current (watts = volts × amps, or W = VA).
At the short circuit current point, the power output is zero, since the voltage is zero.
At the open circuit voltage point, the power output is also zero, but this time it is because the current is zero.
There is a point on the "knee" of the curve where the maximum power output is located. This point on our example curve is where the voltage is 17 volts, and the
current is 2.5 amps. Therefore the maximum power in watts is 17 volts times 2.5 amps, equaling 42.5 watts.
The power, expressed in watts, at the maximum power point is described as peak, maximum, or ideal, among other terms. Maximum power is generally abbreviated as "I (mp)." Various manufacturers call it maximum output power, output, peak power, rated power, or other terms. The current-voltage (I-V) curve is based on the module being under standard conditions of sunlight and module temperature. It assumes there is no shading on the module.
-
Impact of solar radiation on V-I characteristic curve of Photovoltaic Module
Standard sunlight conditions on a clear day are assumed to be 1000 watts of solar energy per square meter (1000 W/m2). This is sometimes called "one sun," or a "peak sun." Less than one sun will reduce the current output of the module by a proportional amount. For example, if only one-half sun (500 W/m2) is available, the amount of output current is roughly cut in half.
Figure 2.8: Change in Photovoltaic module voltage and current on change in solar radiation
For maximum output, the face of the photovoltaic modules should be pointed as straight toward the sun as possible.
-
Impact of temperature on V-I characteristic curve of Photovoltaic Module
-
Module temperature affects the output voltage inversely. Higher module temperatures will reduce the voltage by
0.04 to 0.1 volts for every one Celsius degree rise in temperature (0.04V/0C to 0.1V/0C). In Fahrenheit degrees, the voltage loss is from 0.022 to 0.056 volts per degree of temperature rise.
Figure 2.9: A Typical Current-Voltage Curve for a Module at 25°C (77°F) and 85°C (185°F)
This is why modules should not be installed flush against a surface. Air should be allowed to circulate behind the back of each module so it's temperature does not rise and reducing its output. An air space of 4-6 inches is usually required to provide proper ventilation.
-
Photovoltaic Array
Desired power, voltage, and current can be obtained by connecting individual PV modules in series and parallel combinations in much the same way as batteries. When modules are fixed together in a single mount they are called a panel and when two or more panels are used together, they are called an array. Single panels are also called arrays. When circuits are wired in series (positive to
negative), the voltage of each panel is added together but the amperage remains the same. When circuits are wired in parallel (positive to positive, negative to negative), the voltage of each panel remains the same and the amperage
of each panel is added. This wiring principle is used to build photovoltaic (PV) modules. Photovoltaic modules can then be wired together to create PV arrays.
Figure 2.10: PV cells are combined to create PV modules, which are linked to create PV arrays
-
Elements Included In A System Of Photovoltaic System
The main elements that can be included in a system of photovoltaic conversion are [4]: Batteries, Photovoltaic Modules, Loads DC and AC, Load Regulators, Invertors, Converters.
-
Batteries: Normally they have been considered as a simple element of storage of electrical energy. Batteries are often sold with a PV system. The primary purpose is to store the electricity not immediately used, which could be used at some later time. With net metering, the value of batteries is less because the utility grid basically acts as a storage facility. For a reliable generation system that can function independent of the utility grid, however, batteries may be a viable component to the total system. Back-up generators may be included in a system to provide power when the PV system is not operating, and are generally included when systems are not grid connected. Neither batteries nor generators are eligible for rebate money.
-
Solar panel: The solar panel is the power source of all photovoltaic installation. It is the result of a set of photovoltaic cells in series and parallel. Solar panel gives power to battery or inverter through charge controller (Regulator).
-
Regulator: It is the element to protect the battery against to risking situations as overloads and over discharges. The theoretical formulation of the model can be simple, although it is necessary to consider the peculiar discontinuities of the model and the inter performance with the rest of the analyzed models.
-
Inverter: The inverter allows transforming the DC current to AC. A photovoltaic installation that incorporates
an inverter can belong to two different situations, based on the characteristics of the alternating network. In first an isolated system, where the inverter is the element of the network and has to feed the set of loads and in second situation the inverter is connected to the public network, to which it sends the energy generated by the system.
-
Converter: The positioning of a converter between the panels and the batteries will improve the whole photovoltaic installation, allowing different controls from the system. Depending on the applied regulation, the panels will contribute to the maximum energy given to the system or the optimal energy for their operation, assuring an efficient charge of the battery.
-
Load: It is the component responsible to absorb this energy and transform it into work.
-
-
Types of PV System
PV technology was first applied in space, by providing electricity to satellites. Today, PV systems can be used to power just about anything on Earth. On the basis working operation PV systems operate in four basic forms [29].
-
Grid Connected PV Systems – These systems are connected to a broader electricity network. The PV system is connected to the utility grid using a high quality inverter, which converts DC power from the solar array into AC power that conforms to the grid's electrical requirements. During the day, the solar electricity generated by the system is either used immediately or sold off to electricity supply companies. In the evening, when the system is unable to supply immediate power, electricity can be bought back from the network.
Figure 2.11: Grid Connected PV System
-
Standalone Systems: PV systems not connected to the electric utility grid are known as Off Grid PV Systems and also called stand-alone systems. Direct systems use the PV power immediately as it is produced, while battery storage systems can store energy to be used at a later time, either at night or during cloudy weather. These systems are used in
isolation of electricity grids, and may be used to power radio repeater stations, telephone booths and street lighting. PV systems also provide invaluable and affordable electricity in developing countries like India, where conventional electricity grids are unreliable or non-existent.
Figure 2.12: Standalone PV System
-
Hybrid System: A hybrid system combines PV with other forms of power generation, usually a diesel generator. Biogas is also used. The other form of power generation is usually a type which is able to modulate power output as a
function of demand. However more than one form of renewable energy may be used e.g. wind and solar. The photovoltaic power generation serves to reduce the consumption of non renewable fuel.
Figure 2.13: Hybrid PV System
-
Grid Tied with Battery Backup PV system: Solar energy stored in batteries can be used at nighttime. Using net metering, unused solar power can be sold back to the grid.
With this system, you will have power even if your neighborhood has lost power.
Figure 2.14: Grid Tied with Battery Backup PV System
-
-
We Prefer Grid Connected PV System
Because as day by day the demand of electricity is increased and that much demand cannot be meeting up by the conventional power plants. And also these plants create pollution. So if we go for the renewable energy it will be better but throughout the year the generation of all renewable energy power plants. Grid tied PV system is more reliable than other PV system. No use of battery reduces its capital cost so we go for the grid connected topology. If generated solar energy is integrated to the conventional grid, it can supply the demand from morning to afternoon (total 6 hours mainly in sunny days) that is the particular time range when the SPV system can fed to grid. As no battery backup is there, that means the utility will continue supply to the rest of the time period. Grid- connected systems have demonstrated an advantage in natural disasters by providing emergency power capabilities when utility power was interrupted. Although PV power is generally more expensive than utility- provided power, the use of grid connected systems is increasing.
CHAPTER 3
MAXIMUM POWER POINT TRACKING
The efficiency of a solar cell is very low. In order to increase the efficiency, methods are to be undertaken to match the source and load properly. One such method is the Maximum Power Point Tracking (MPPT). This is a technique used to obtain the maximum possible power from a varying source. In photovoltaic systems the I-V curve is non-linear, thereby making it difficult to be used to power a certain load. This is done by utilizing a boost converter whose duty cycle is varied by using a MPPT algorithm.
A boost converter is used on the load side and a solar panel is used to power this converter.
-
Methods of MPPT
The MPPT methods can be categorized as direct or indirect. The indirect methods can also be classied as quasi seeking since there is no actual seeking, but only approximation by some other method. Direct methods use measurements of the photovoltaic voltage (Vpv) and
current (Ipv) and obtaining the operating point by changing the voltage based on their response to obtain the MPP. There are many methods used for maximum power point tracking, a few are listed below:
-
Perturb and Observe method
-
Incremental Conductance method
-
Parasitic Capacitance method
-
Constant Voltage method
-
Constant Current method
-
Perturb and Observe method
This method is the most common. In this method very less number of sensors are utilized. The operating voltage is sampled and the algorithm changes the operating voltage in the required direction and samples /. If / is positive, then the algorithm increases the voltage value towards the MPP until / is negative. This iteration is continued until the algorithm finally reaches the MPP. This algorithm is not suitable when the variation in the solar irradiation is high. The voltage never actually reaches an exact value but perturbs around the maximum power point (MPP).
-
Incremental Conductance method
This method uses the PV array's incremental conductance
/to compute the sign of /. When /is equal and opposite to the value of I/V (where /=0) the algorithm knows that the maximum power point is reached and thus it terminates and returns the corresponding value of operating voltage for MPP. This method tracks rapidly changing irradiation conditions more accurately than P&O method. One complexity in this method is that it requires many sensors to operate and hence is economically less effective.
P=V*I (1)
Differentiating w.r.t voltage yields;
/d=()/ (2)
/ = (/) + (/V)
(3)
/ = + (/)
(4)
When the maximum power point is reached
/=0. Thus the condition would be;
the
slope
/=0
(5)
+ (/)=0
(6)
/= /
(7)
/ = (/) + (/V)
(3)
/ = + (/)
(4)
When the maximum power point is reached
/=0. Thus the condition would be;
the
slope
/=0
(5)
+ (/)=0
(6)
/= /
(7)
3.1.5 Constant Current method .
-
Parasitic Capacitance method
This method is an improved version of the incremental conductance method, with the improvement being that the effect of the PV cell's parasitic union capacitance is included into the voltage calculation.
-
Constant Voltage method
-
This method which is a not so widely used method because of the losses during operation is dependent on the relation between the open circuit voltage and the maximum power point voltage. The ratio of these two voltages is generally constant for a solar cell, roughly around 0.76. Thus the open circuit voltage is obtained experimentally and the operating voltage is adjusted to 76% of this value.
Similar to the constant voltage method, this method is dependent on the relation between the open circuit current and the maximum power point current. The ratio of these two currents is generally constant for a solar cell, roughly around 0.95. Thus the shot circuit current is obtained experimentally and the operating current is adjusted to 95% of this value.
The methods have certain advantages and certain disadvantages. Choice is to be made regarding which algorithm to be utilized looking at the need of the algorithm and the operating conditions. For example, if the required algorithm is to be simple and not much effort is given on the reduction of the voltage ripple then P&O is suitable. But if the algorithm is to give a definite operating point and the voltage fluctuation near the MPP is to be reduced then the IC method is suitable, but this would make the operation complex and more costly.
3.2 Flow Chart of MPPT Algorithms
Two of the most widely used methods for maximum power point racking are studied here. The methods are:
-
Perturb & Observe Method.
-
Incremental Conductance Method.
The flow charts for the two methods are shown below. Flow chart for perturb & observe:
Figure 3.1: Flowchart of the Perturb and Observe MPPT algorithm
Flow chart of incremental conductance method:
Figure 3.2: Flow chart of incremental conductance method
These two algorithms are implemented using the Embedded MATLAB function of Simulink, where the codes written inside the function block are utilized to vary certain signals with respect to the input signals.
CHAPTER-4
MODELING OF GRID CONNECTED PV SYSTEM
-
Modeling of PV Module
The simplest model to represent a PV module is the ideal diode model presented as Rs-model and Rp-model.
Rs-model has four unknown parameters and is known as the Single diode four-parameter model. Similar to the ideal diode model, this model is very simple and requires minimal computation power. The accuracy is better than the ideal diode model, but it still exhibits some serious deciencies, particularly with temperature variations. This model is by far the most widely used in PV system simulation.
Figure 4.1: Rs-Model (Single diode four parameter model)
The Rp-model, or single diode ve parameter model, adds a shunt resistance (Rp) to the four parameter model and therefore considers the leakage current to the ground. Figure 4.2 shows the equivalent circuit and equation shows the current-voltage (I-
V) characteristics. This model is used for implementation in Simulink/MATLAB in this thesis.
Figure 4.2: Rp-Model (Single diode five parameter model)
(1)
The Rp-model is insuciently accurate when dealing with low irradiation levels. This model is based on the assumption that the recombination loss in the depletion region is absent. In a real solar cell this loss is signicant and the single diode model cannot be used to accurately model this eect.
-
Modeling of Boost Converter
Boost converter steps up the input voltage magnitude to a required output voltage magnitude without the use of a transformer. The main components of a boost converter are an inductor, a diode and a high frequency switch. These in a co-ordinated manner supply power to the load at a voltage greater than the input voltage magnitude. The control strategy lies in the manipulation of the duty cycle of the switch which causes the voltage change.
Figure 4.3: Circuit Diagram of DC-DC boost converter
There are two modes of operation of a boost converter. Those are based on the closing and opening of the switch. The first mode is when the switch is closed; this is known as the charging mode of operation. The second mode is when the switch is open; this is known as the discharging mode of operation.
In charging mode of operation; the switch is closed and the inductor is charged by the source through the switch. The charging current is exponential in nature but for simplicity is assumed to be linearly varying. The diode restricts the flow of current from the source to the load and the demand of the load is met by the discharging of the capacitor.
In discharging mode of operation; the switch is open and the diode is forward biased. The inductor now discharges and together with the source charges the capacitor and meets the load demands. The load current variation is very small and in many cases is assumed constant throughout the operation.
During continuous conduction mode of operation this converter has two intervals of boost operation. We shall do steady state analysis i.e. inductor volt-second balance and capacitor charge balance in both the intervals. Then by applying small ripple approximation we can easily design the boost converter as per requirements.
-
Modeling of Battery Storage System
-
Simple Linear Battery Model
One of the most commonly used battery models is shown in gure. This model consists of only a DC voltage (V0) and a constant resistance (Rinternal). The main advantage with this model is its simplicity and easy extraction of parameters. Only two measurements are needed: One open circuit measurement at full charge to determine V0 and another measurement with a connected load to calculate Rinternal.
Figure 4.4: Circuit diagram of a simple linear battery model
This model can be suitable if the state of charge is not considered or the battery is assumed to have unlimited energy. The model does not take into account the eects of varying state of charge and is therefore not suitable if the available voltage at dierent charge levels is of interest. This model can be suitable if the state of charge is not considered or the battery is assumed to have unlimited energy. The model does not take into account the eects of
varying state of charge and is therefore not suitable if the available voltage at dierent charge levels is of interest.
-
State of charge dependent resistance model
A small modication of the model outlined can be made by including a variable resistor that changes value based on the state of charge (SOC). The equivalent circuit shown in gure is based on equation 1.
Figure 4.5: Circuit diagram of SOC dependent battery model
E = V0 (Rb + K/SOC)*Ibatt (1)
The model is very simple and can be accurate over a large part of the SOC range. The K/SOC-resistance adds a sharp reduction in voltage when the state of charge is low. The rise in voltage when the state of charge approaches 1 is absent and this model therefore is very inaccurate in that range.
This model was abandoned because the voltage characteristics was not modelled accurately and the implementation suered some problems with algebraic loops and instability.
-
Controlled voltage source model
-
Accurate modelling of a battery is a very complex process that requires knowledge of the electrochemical processes
within. For crude energy simulation purposes, a model that accounts for the varying voltage that is available based on the SOC can be sucient.
The model presented in this section uses only the SOC as a state variable. The voltage is modelled by a controlled voltage source that is dependent on the SOC as shown in equation 2. The explanation of the variables in the following equations and circuit diagrams is available.
E = E0 K*{Q0/( Q0 Q)} + Aexp BQ (2)
The variable Q represents the actual battery charge and the variable Q0 is the rated battery capacity. The SOC is therefore the relation Q/Q0. The actual battery charge is modelled by integrating the battery current and adding the start charge as shown in equation used in figure below.
Figure 4.6: Circuit diagram of the battery model with a non-linear controlled voltage source
CHAPTER-5 SIMULINK IMPLEMENTATIONS
The implementation is very exible because of this ease of modication. In fact, it is so exible that a script could prompt a user for the input data sheet values for the solar module he or she wants to simulate together with other optional variables like number of PV modules in a string and the script can dene the variables necessary and runa simulation with available irradiance data. To produce all
the gures and results in this paper, several congurations of PV module models, other systems and battery models must be constructed. Some of the blocks implemented in Simulink are not modied for dierent simulation cases and include: Battery module, PV module, MPPT controller, and DC-DC converter. These systems are copied into dierent simulation cases and are only modied by the parameter values dened in the scripts that run the simulations.
-
Implementation of PV module
Figure 5.1: Photovoltaic module model structure
The solar cell was modeled in the single diode format. This was modelled using the Sim Power System blocks in the MATLAB library. The Simulink model is as shown.
Figure 5.2: Simulation Diagram of a Temperature-dependent PV Array
A controlled current source is utilized to drive the solar cell. The control signal is provided by the Ilg generator unit. The Ilg generator takes into account the number of
series connected, number of parallel connected solar cells and the temperature to determine the input signal from the solar cell.
Figure 5.3: Simulation Diagram of a Diode of PV Array
-
Implementation of Boost Converter
The simulink model for the DC/DC boost converter is as shown in figure:
Figure 5.4: Simulation Diagram of Boost Converter
-
Implementation of Voltage Source Inverter and its controller
Inverters are used to convert DC current into AC currents in PV systems. Different types of inverters produce a different quality of electricity. So, the user must match the power quality required by your loads with the power
quality produced by the inverter. Major discrepancies exist between power generation with PV modules and the requirements of the public grid. The job of the inverter is to connect the systems with each other and to feed the solar power into the grid with the highest possible efficiency.
Figure 5.5: Simulation Diagram of VSC Controller
-
Implementation of Complete Model of Grid Connected PV System
The detailed model contains:
-
PV array delivering a maximum of 150 kW at 1000 W/m2 sun irradiance.
-
5-kHz boost converter increasing voltage from PV natural voltage (272 V DC at maximum power) to 500 V DC. Switching duty cycle is optimized by the MPPT controller that uses the Perturb and Observe and Proportional Integral Regulator technique.
-
1980-Hz (33*60) 3-level 3-phase VSC. The VSC converts the 500 V DC to 260 V AC and keeps unity power factor.
-
10-kvar capacitor bank filtering harmonics produced by VSC.
-
100-kVA 260V/25kV three-phase coupling transformer.
-
Utility grid model (25-kV distribution feeder + 120 kV equivalent transmission system).
-
For this detailed model, the electrical circuit is discretized at 10 micro seconds sample time, whereas sample time used for the control systems is 100 micro seconds.
Figure 5.6: Complete Simulation Diagram of Grid Connected PV System
CHAPTER-6
SIMULATION RESULTS AND DISCUSSIONS
-
Solar Irradiation and Ambient Temperature
The simulation has been carried out in 12 hours for a smooth day with the variable solar irradiance and ambient temperature. Following are the input data signals for the PV array to generate the suitable amount of energy.
Figure 6.1: Input Data for Solar Irradiance and Temperature
-
PV Module and MPPT Controller
The simulation of a PV cell was done using MATLAB/SIMULINK. The PV and IV curves from the simulation are as shown.
The parameters were obtained for a generalized solar cell. The plot is similar to the theoretically known plot of the solar cell voltage and current. The peak power is denoted by a circle in the plot. PV and IV plots for the three different conditions are being defined for the PV array, i.e.,
-
PV and IV curves for PV array at constant solar radiation of 1000W/m^2.
-
PV and IV curves for PV array at constant ambient temperature of 25deg.C.
-
PV and IV curves for PV module at constant ambient temperature of 25deg.C.
Few 1-D lookup tables are being used in the modeling of the PV array. The data used is as follows in the tables below:
S.NO.
Rs (ohms)
Rp (ohms)
Vt (V)
Iph (A)
Isat (A)
1.
0.012
215.4
28.2
472.3
1.29e-8
2.
0.010
102.4
30.8
476.8
4.2e-7
3.
0.009
39.1
33.4
483.9
7.9e-6
4.
0.010
23.3
35.9
491.1
9.7e-5
5.
0.014
16.3
38.5
498.3
8.6e-4
Table 6.1: 1-D lookup table data for PV array design parameters
Figure 6.2: PV and IV Curves of PV Array at 1000W/m2
Figure 6.3: PV and IV Curves for PV Array at 250C
Figure 6.4: PV and IV Curves for PV Module at 250C
The simulation results for the duty cycle (D) which is being defined by the use of P&O algorithm in MPPT algorithm for getting the maximum power point tracking in the PV module.
Figure 6.5: Irradiance, Temperature and Duty cycle Curves for PV Module
The simulation results for the output voltage, output current, diode current and output generated power from the module is as follows. The output voltage from PV module is typically around 500V and output current with respect to the load connected to it, is varying between the range of 50A-300A as per the input data conditions. The output
power generated from the PV module is the product of voltage and current and is is ranging up to 1.5*10^5W. The diode current is the current drawn by the semiconductor diode and is inversely proportional to the output current from the PV module.
-
-
Battery Module
Figure 6.6: Output Voltage, Current, Diode Current and Power Curves for PV Module
below the battery nominal voltage. Finally, the third
The parameters of the equivalent circuit can be modified to represent a particular battery type, based on its discharge characteristics. A typical discharge curve is composed of three sections, as shown in the figure. The first section represents the exponential voltage drop when the battery is charged. Depending on the battery type, this area is more or less wide. The second section represents the charge that can be extracted from the battery until the voltage drops
section represents the total discharge of the battery, when the voltage drops rapidly.
When the battery current is negative, the battery will recharge following a charge characteristic as shown below in the figure. The exponential voltage increases when battery is charging, no matter the SOC of the battery. When the battery is discharging, the exponential voltage decreases immediately.
Figure 6.7. Discharge Characteristics of Battery Module
The SOC of the battery is being varied as per the requirement and system conditions. The State-Of-Charge of the battery (between 0 and 100%). The SOC for a fully charged battery is 100% and for an empty battery is 0%.
Figure 6.8: SOC, Current and Voltage Characteristics of Battery Module (SOC: 100%)
Figure 6.9: SOC, Current and Voltage Characteristics of Battery Module (SOC: 90%)
-
Voltage Source Converter
The use of the Three-Level Bridge block in an AC-DC converter consisting of a three-phase IGBT-based voltage sourced converte (VSC). The converter is pulse-width modulated (PWM) to produce a 500 V DC voltage (+/- 250
V). The VSC is controlled in a closed loop by two PI regulators in order to maintain a DC voltage of 500 V at the load while maintaining a unity input power factor for the AC supply.
Figure 6.10: Reference Voltage, Maximum Voltage and Modulation Index Curves of VSC
Figure 6.11: Line to Line Voltage Output Curve of VSC
Figure 6.12: Id and Iq Current Curves of VSC Controller
-
Energy Management between PV System and AC Grid
An electrical storage element generates expensive investment and operation costs with strong operating constraints. In this context and considering that subventions are restricted in the short-term future, the objective is to reduce operation costs by managing the
power flows in the system. This work deals with power flows management for grid connected PV systems with storage (GPVS) with a focus on optimal scheduling.
Simulation results for the reference phase voltage, current and 3 phase voltage at AC grid is as shown in the figure below.
Figure 6.13: Line voltage, Line current and Three Phase Voltage at AC Grid
The energy storage will improve the availability and reliability of the power system. There are many energy storage devices are used in the electrical power system such as battery, flywheels, ultra-capacitor and fuel cell. Applications of the storage device power generation and the load requirements, for example battery is used as solar photovoltaic generation, flywheels are used at the shaft of the wind mills and ultra capacitors are used in the transmission line to reduce the line loses in the electrical power system. In this thesis, the main parameter of managing the energy storage is state of charge in the
battery; its operation depends upon the load and the source. The state of charging and discharging occurs when the solar generation not capable enough to supply the power or during the peak time of the demand.
In the grid connected system, proper switching operations can be performed by using the embedded MATLAB function, this leads the system as uninterrupted power supply to the load. The maximum energy from the solar generation and storage device gives supply to the load; the minimum energy is drawn from the grid.
Figure 6.14: Power Flows between Grid and PV Battery System using EMS (SOC: 100%)
Power at Grid Power generation from PV array Power flow from battery to grid
When the state of charge of battery is 0.9, the battery is not fully charged. So, it will first charge itself with full capacity and then, will supply power to the grid.
The energy management is performed as per the system requirements. In this model, the priority is being set for the power flows and herein, the first priority is given to the
charging of the battery for the energy reserve purpose to maintain the continuity of the supply and second priority is given to the grid. That is why the battery will always remain fully charged and after that the power will be supplied to the grid.
Figure 6.15: Power Flows between Grid and PV System using EMS (SOC: 90%)
Parameters |
Notations |
Values |
Rated Power |
Pmpp |
85W |
Voltage at mpp |
Vmpp |
54.7V |
Current at mpp |
Impp |
5.58A |
Open circuit voltage |
Voc |
64.2V |
Short circuit current |
Isc |
5.96A |
Current coefficient |
Ki |
0.003516A/deg.C |
Voltage coefficient |
Kv |
-0.177V/deg.C |
Number of cells |
Ncells |
96 |
Nominal operating cell temp |
Tnoct |
25 deg.C |
Reference cell temp |
Tref |
320.15 K |
Reference irradiance |
Ir0 |
1000 W/m2 |
Battery current |
Ibatt |
2.8261A |
Battery terminal voltage |
Vbatt |
500V |
SOC State of charge, number between 0 and 1 |
– |
0.9-1.0 |
Terminal resistor, independent of SOC |
Rb |
0.76923 ohms |
Parameters |
Notations |
Values |
Rated Power |
Pmpp |
85W |
Voltage at mpp |
Vmpp |
54.7V |
Current at mpp |
Impp |
5.58A |
Open circuit voltage |
Voc |
64.2V |
Short circuit current |
Isc |
5.96A |
Current coefficient |
Ki |
0.003516A/deg.C |
Voltage coefficient |
Kv |
-0.177V/deg.C |
Number of cells |
Ncells |
96 |
Nominal operating cell temp |
Tnoct |
25 deg.C |
Reference cell temp |
Tref |
320.15 K |
Reference irradiance |
Ir0 |
1000 W/m2 |
Battery current |
Ibatt |
2.8261A |
Battery terminal voltage |
Vbatt |
500V |
SOC State of charge, number between 0 and 1 |
– |
0.9-1.0 |
Terminal resistor, independent of SOC |
Rb |
0.76923 ohms |
Power at Grid Power generation from PV array Power flow from battery to grid The table 6.2 explains the design parameters and outputs of the PV system:
Table 6.2: Design Parameters and Outputs of PV System
CHAPTER 7 CONCLUSION AND FUTURE SCOPE
-
Conclusion
In this thesis, a Simulink implementation based on the ve parameter diode PV model has been constructed. The eects of varying model parameter values and the eect of different solar light intensity and ambient temperature has been demonstrated.
Maximum power point tracking using the perturb and observe algorithm has been implemented. Some
weaknesses with this tracking method has been exposed, and these include wrong reactions to changing inputs, slow voltage reaction, oscillation around MPP and a limited amount of perturbations per data point in these simulations. The maximum power point tracking implementations successfully keeps the voltage close to the maximum power point most of the time. The constructed model of photovoltaic modules is a exible tool for simulation of dierent PV module types. When MPPT is used there is no need to input the duty cycle, the algorithm iterates and decides the duty cycle by itself. But if MPPT had not been
used, then the user would have had to input the duty cycle to the system. When there is change in the solar irradiation the maximum power point changes and thus the required duty cycle for the operation of the model also changes. But if constant duty cycle is used then maximum power point cannot be tracked and thus the system is less efficient. The various waveforms were obtained by using the plot mechanism in MATLAB. There is a small loss of power from the solar panel side to the boost converter output side. This can attributed to the switching losses and the losses in the inductor and capacitor of the boost converter. This can be seen from the plots of the respective power curves.
The current model is designed in a way that it cn be easily extended by adding more specialized constraints for reducing the cost of electricity consumption and maximizing availability. For example, in countries where power outages is an issue, constraints specific to power blackouts can be integrated by using energy management system. In the end, Energy Management System by changing the state of charge (SOC) of battery module is performed with the help of battery controller and the simulation results are verified.
-
Scope for Future Work
-
Improvement to this work can be made by tracking the maximum power point in changing
environmental conditions by different algorithms using other techniques. Environmental change can be change in solar irradiation or change in ambient temperature or even both.
-
Further study can be made using optimization methods such as Neural Network, Genetic Algorithms, Particle Swarm Optimization etc. to achieve maximum power at grid.
REFERENCES
-
P.Sritakaew & A.Sangswang, On the Reliability Improvement of Distribution Systems Using PV Grid-Connected Systems. IEEE Asia Pacific Conference on Circuits and systems. pp. 1354 – 1357, 2006.
-
Allen M. Barnett, Solar electrical power for a better tomorrow. Photovoltaic Specialists IEEE Conference, Page(s): 1 8, 1996.
-
R. Ramkumar & J. E. Bigger, Photovoltaic Systems. Proceedings of IEEE. Volume: 81, Page(s): 365 377, 1993.
-
G. Ofualagba, Photovoltaic Technology, Applications and Market, IEEE Conference on Power and Energy society general meeting – conversion and delivery to electrical energy, Vol.21, Page(s): 1 5, 2008.
-
N. Jenkins, Photovoltaic systems for small-scale remote power supplies, IET Journals. Volume: 9, Page(s): 89 96, 1995.
-
Souvik Ganguli and Sunanda Sinha, A Study and Estimation of Grid Quality Solar Photovoltaic Power Generation Potential in some districts of West Bengal. National Conference on Trends in Instrumentation & Control Engineering, Thapar University, Patiala, Page(s): 522-528, 29-30th Oct., 2009.
-
Brig.M.R.Narayaoan, D.V.Gupta, R.C.Gupta & R.S.Gupta, Design, Development and Installation of 100 kW utility grid connected solar PV plants for rural application- an Indian experience. IEEE first world conference on Photovoltaic Energy conversion. Volume: 1. Page(s): 1073 1076, 1994.
-
Wang Jianqiang & Li Jingxin, Design and Experience of Grid- connecting Photovoltaic Power System, IEEE International Conference on Sustainable Energy Technology, Page(s): 607 – 610, 2008.
-
B. Marion,J. Adelstein,K. Boyle and fellows, Performance Parameters for GridConnected PV Systems, Photovoltaic Specialists IEEE Conference, Page(s): 1601 – 1606, 2005.
-
Chang Ying-Pin & Shen Chung-Huang, Effects of the Solar Module Installing Angles on the Output Power. 8th International conference on Electronic Measurement and Instruments. Page(s): 1- 278 – 1-282,2007.
-
D. Picault, B. Raison, and S. Bacha, Guidelines for evaluating grid connected PV system topologies. IEEE International Conference on Industrial Technology. Page(s): pp. 1-5, 2009.
-
Jinhui Xue , Zhongdong Yin , Qipeng Song, and Renzhong Shan, Analyze and Research of the inverter for Gridconnecting photovoltaic system, Third IEEE International Conference on Electric Utility Deregulation and Restructuring Power Technologies, Page(s): 2530 2535, 2008.
-
Phil Bolduc, David Lehmicke & Joseph Smith, Performance of a grid connected PV system with energy storage. IEEE Photovoltaic Specialists conference. Page(s): 1159 1162, 1993.
-
Eduardo Román, Ricardo Alonso & Pedro Ibañez, Intelligent PV Module for GridConnected PV Systems, IEEE Transactions on Industrial electronics, Vol.53.No.4, Page(s): 1066 1073, August 2006.
-
V. Lughi , A. Massi Pavan , S. Quaia , and G. Sulligoi, Economical Analysis and Innovative Solutions for Grid Connected PV Plants, International Symposium on Power Electronics, Electrical Drives, Automation and Motion, Page(s): 211 216, 2008.
-
Kosuke Kurokawa, Kazuhiko Kato , Masakazu Ito, Keiichi Komoto, Tetsuo Kichim, & Hiroyuki Sugihara The cost analysis of very large scale PV system on the world desert. Photovoltaic Specialists IEEE Conference, Page(s): 1672 1675, 2002. 17. M.
C. Cavalcanti, G. M. S. Azevedo and fellows , Efficiency Evaluation in Grid Connected Photovoltaic Energy Conversion Systems, Photovoltaic Specialists IEEE Conference, Page(s): 269 275, 2005.
-
M.J. de Wild-Scholten, E.A. Alsema, E.W. ter Horst & V.M. Fthenakis, A cost and environmental impact comparison of grid connected rooftop and ground-based PV systems from site www.clca.columbia.edu/…/21%20EUPVSC%20%20deWild%20et% 20al%20%20Cos t%20and%20environmental%20impact%20comparison.pdf
-
Evert Nieuwlaar & Erik Alsema, Environmental aspects of PV power systems, Report on the IEA PVPS Task1 Workshop, 25-27 June 1997, Utrecht The Netherlands. Report no. 97072, December 1997.
-
José L. Bernal-Agustà & Rodolfo Dufo-López, Economical and Environmental Analysis of Grid Connected Photovoltaic Systems in Spain. Journals paper on renewable energy, Vol.31, Issue 8, Page(s): 1107-1128, July 2006.
-
Mummadi Veerachary, "Control of TI-SEPIC Converter for Optimal Utilization of PV Power", IICPE, 2010 New Delhi.
-
M. Berrera, A. Dolara, R. Faranda and S. Leva, Experimental test of seven widely-adopted
-
MPPT algorithms, 2009 IEEE Bucharest Power Tech Conference, June 28th – July 2nd, Bucharest, Romania.
-
Intergovernmental Panel On Climate Change. Climate change 2007: The physical science basis. Agenda, 6(07):333, 2007.
-
The international energy agency (iea). Technology roadmap: Solar photovoltaic energy,
http://www.iea.org/publications/freepublications/ publication/pv_roadmap.pdf.
- [http: Solar Electric Systems] Chapter Three Introduction to Solar Electric Systems available at www.kysolar.org/ky_solar_energy_guide/chapters/Chapter_3_PVint ro.pdf
-
T.D. Hund, S. Gonzalez, and K. Barrett. Grid-tied pv system energy smoothing. In Photovoltaic Specialists Conference (PVSC), 2010 35th IEEE, pages 002762002766, June 2010.
- [http: Series and Parallel connection] Series and Parallel Wiring available at www.termpro.com/articles/spkrz.html.
-
From site www.polarpowerinc.com.
-
From site www. Solartradingpost.com.
-
Havard Breisnes Vika. Literature study of energy storage technologies – with a simulation case of smes and battery energy storage,tet 4520 – specialization project, ntnu, december 2013.